大量生產方式是一種通過實現零件間的可通用性與可互換性,并最大限度地進行專業職能分工,以采用專門的工裝模具、機械設備或流水線大批量生產標準化產品的生產方式。這一生產方式誕生于20世紀初的美國福特公司。這一生產方式的發明,徹底顛覆了工業發展的歷史,人類社會徹底告別了“手工作坊”式的單件生產方式,極大地提高了生產效率,降低了制造成本,促使以規模經濟為基礎的現代商業市場的形成,同時也極大地促進了美國乃至全球工業的整體發展。第二次世界大戰以后,大量生產方式正式成為了世界工業的主導生產模式。然而,在上世紀60年代以后,伴隨著市場競爭的日益激烈化以及消費者需求的日漸多元化,大量生產方式開始不斷暴露出它的以下弊病:
產品品種過于單一,無法滿足消費者日益多樣的需求
人員專業分工過細,職能部門間的橫向溝通變得較為困難
產品開發與制造過程中存在大量排隊等待的“在制品”,客戶響應速度緩慢
產品庫存量大,積壓大量流動資金
正是由于以上的原因,導致大量生產方式僅能適用于需求種類單一、穩定且巨大,并且呈現“供不應求”的市場環境。而在當今的市場環境下,人類社會“生產能力小于市場需求”這一難題已經基本解決,消費者對于產品的需求已經日益個性化與多樣化,大量生產方式漸漸喪失了原有的競爭優勢。企業要滿足消費者需求的這一變化趨勢,就不得不增強生產柔性,以實現多品種小批量的生產模式。正是在這一背景下,精益生產方式應運而生,并且迅速在全球范圍內得到了推廣與應用。
精益生產方式是一種以客戶需求為導向,通過在組織內各層級使用多技能員工,建立針對客戶及其產品的跨職能業務團隊,加強內部信息流動,并使用通用性與柔性更強的設備或生產線快速生產種類繁多的產品的生產方式。這一生產方式同大量生產方式在思維上最大的不同,即在于對浪費的正確認識。在使用大量生產方式的傳統企業中,很多司空見慣的活動,如果放在精益企業中,都會被認作為“浪費”。在精益企業里,對于浪費活動的定義需要包含以下三條原則:
未使產品發生物理或化學變化的活動
客戶不愿意為其買單的活動
未能一次做對的返工活動
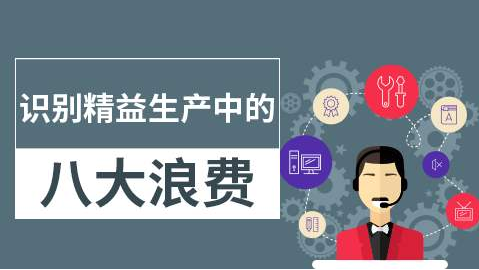
在使用大量生產方式的傳統企業中,為了片面提高設備利用率,降低單件制造成本,很多以上活動(比如非瓶頸工序的滿負荷運轉、減少換型頻次、增大加工批量等),都不會被視作“浪費”,這也導致了傳統企業的供應鏈“端到端”過程中存在大量的過量生產、庫存、等待、搬運等浪費活動,這些浪費活動導致了企業交付周期的延長,資金周轉能力的下降,進而影響了企業的整體盈利能力。而精益企業更熱衷于不斷發現并消除以上的浪費活動,壓縮產品交付周期,提升資金周轉能力,并最終促成企業整體盈利能力的提升。
總之,大量生產方式和精益生產方式在思維方式上的區別就在于對浪費的正確認識,這也就是精益生產方式在當下正日益取代大量生產方式的原因。
本文為冠卓咨詢原創文字作品,任何人或組織不得對本文進行篡改,轉載或以盈利為目的行為,一經發現,將負法律責任。