01歷史比較
1、精益生產歷史
20世紀初,從美國福特汽車公司創立第一條汽車生產流水線以來,大規模的生產流水線一直是現代工業生產的主要特征。
大規模生產方式是以標準化、大批量生產來降低生產成本,提高生產效率的。
這種方式適應了美國當時的國情,汽車生產流水線的產生,一舉把汽車從少數富翁的奢侈品變成了大眾化的交通工具,美國汽車工業也由此迅速成長為美國的一大支柱產業,并帶動和促進了包括鋼鐵、玻璃、橡膠、機電以至交通服務業等在內的一大批產業的發展。
大規模流水生產在生產技術以及生產管理史上具有極為重要的意義。
但是第二次世界大戰以后,社會進入了一個市場需求向多樣化發展的新階段,相應地要求工業生產向多品種、小批量的方向發展,單品種、大批量的流水生產方式的弱點就日漸明顯了。
為了順應這樣的時代要求,由日本豐田汽車公司首創的精益生產,作為多品種、小批量混合生產條件下的高質量、低消耗進行生產的方式在實踐中摸索、創造出來了。
1950年,日本的豐田英二考察了美國底特律的福特公司的轎車廠。
當時這個廠是世界上最大而且效率最高的制造廠,每天能生產7000輛轎車,比日本豐田公司一年的產量還要多。
豐田英二對這個龐大企業的每一個細微之處都做了審慎的考察。他在寫給豐田總部的報告中說:“那里的生產體制還有些改進的可能”。
戰后的日本經濟蕭條,缺少資金和外匯。怎樣建立日本的汽車工業?
照搬美國的大量生產方式,還是按照日本的國情,另謀出路,豐田選擇了后者。
日本的社會文化背景與美國是大不相同的,日本的家族觀念、服從紀律和團隊精神是美國人所沒有的,日本沒有美國那么多的外籍工人,也沒有美國的生活方式所形成的自由散漫和個人主義的泛濫。
日本的經濟和技術基礎也與美國相距甚遠。
日本當時沒有可能全面引進美國成套設備來生產汽車,而且日本當時所期望的生產量僅為美國的幾十分之一。“規模經濟”法則在這里面臨著考驗。
豐田英二和他的伙伴大野耐一進行了一系列的探索和實驗,根據日本的國情,提出了解決問題的方法。
經過30多年的努力,終于形成了完整的豐田生產方式,使日本的汽車工業超過了美國,產量達到了1300萬輛,占世界汽車總量的30%以上。
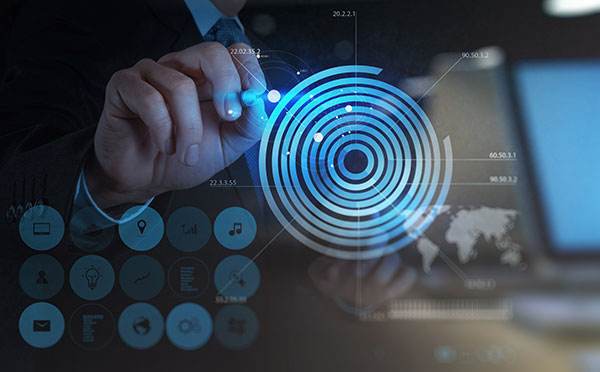
制造、電子、計算機、飛機制造等工業中。
豐田生產方式是日本工業競爭戰略的重要組成部分,它反映了日本在重復性生產過程中的管理思想。
豐田生產方式的指導思想是,通過生產過程整體優化,改進技術,理順物流,杜絕超量生產,消除無效勞動與浪費,有效利用資源,降低成本,改善質量,達到用最少的投入實現最大產出的目的。
日本企業在國際市場上的成功,引起西方企業界的濃厚興趣,西方企業家認為,日本在生產中所采用的方式是其在世界市場上競爭的基礎。
80年代以來,西方一些國家很重視對豐田生產方式的研究,并將其應用于生產管理。
首先推廣應用的是美國的通用汽車,接著其他的汽車公司和其他產業的公司也開始實施精益生產。
隨著各國對精益生產的理解和應用,加之由于市場的快速變化,迫使企業生產需要做出快速響應,
這樣,在精益生產的基礎上,發展了敏捷制造(AM)思想,敏捷制造系統是以精益生產的設備,全面生產維護(TPM)以及設備各組合部之模塊化為基礎建立起來的高柔性生產系統。
敏捷制造能對顧客的多樣化和個性化的需求做出快速的反應,以滿足顧客需求。目前,國際上一些專家把敏捷制造的優勢大致歸納如下:
①由于快捷生產系統各組合部分都盡量模塊與標準化,因而可以易于安裝和重組,以減少設備的制造時間,同時也縮短了設備交貨期;
②降低了與所加工產品的關聯程度(可周期性設計);
③提高了生產單元的標準化程度;
④簡化工具、夾具的支撐點;
⑤可以生產樣品,試生產及正式批量生產以適應產量變化;
⑥可以在購置設備時逐步投資;
⑦設備使用時具有更強的柔性,可轉換性也增強;
⑧可以低成本改造設備,以適應產品轉型;
⑨易于轉產其他產品。
1990年,精益生產(LeanProduction)的英文概念由美國麻省理工學院中的國際汽車組織(IMVP)在經歷了5年的汽車行業調查后而提出的。
而實際上早在六七十年代日本的豐田汽車公司已經在這方面進行了研究與實踐,提出了所謂的“豐田生產方式(TPS)”,這實際上就是精益生產的雛型。
在90年代初各先進工業國紛紛研究精益生產:
德國亞亨大學在原來研究的“獨立制造島”的基礎上提出了精益屋的模型,其它如英國、芬蘭、瑞典等國的企業亦成功地進行了精益改造,
盡管所冠名稱不一定就叫精益生產,但它本質上就是精益生產,而且也從汽車業發展到了其它行業。美國在20世紀90年代中,也在航空業中開始了飛機首創計劃(LeanAircraftInitiative)的研究。
這個研究的中心也是在麻省理工學院宇航系,斯隆管理學院和機械系則在精益理論上作了研究。
當《改變世界的機器》面世以來,精益生產便得以在全球廣泛傳播和被光為學習。緊接著,《精益思想》便說明了怎樣實施精益生產。
今井正明的《改善》以及《現場改善》也講解了精益生產的思想體系和實施方法。
大野耐一的《豐田成功經營的精髓》更是詳細說明了精益管理體系的思想來源和發展。
02六西格瑪歷史

在70年代,Motorola面對日本嚴峻的挑戰,其主席Bobgalvin決定在品質上改善,來迎戰日本高品質的挑戰。
在1981年,他要求其產品必須在五年內有10倍的改善。
于1987年,Motorola建立了六西格瑪的概念,基于統計學上的原理,六西格瑪代表著品質合格率達99.9997%或以上。
換句話說,每一百萬件產品只有3.4件次品,這是非常接近“零缺點”的要求。
六西格瑪計劃要求不斷改善產品、品質和服務,他們制定了目標、工具和方法來達到目標和客戶完全滿意(TotalCustomerSatisfaction)的要求。
在過程上他們提供了黑帶(BlackBelt)和綠帶(GreenBelt)的有經驗工程人員和顧問推行整個計劃,并成為品質改善的先鋒。
Motorola的“七步驟方法”(SevenStepMethod),“不斷改善”(ContinuousImprovement)和客戶完全滿意(TotalCustomerSatisfaction)都是取材自TQM(全面優質管理概念)。
他們提出新設計文化,簡化生產步驟,采用機械臂、通用網絡等來達到他們5“九”(99.999%)品質要求。
三年后該公司的六西格瑪質量戰略取得了空前的成功:產品的不合格率從百萬分之6210(大約四西格瑪)減少到百萬分之32(5.5西格瑪),在此過程中節約成本超過20億美金。
隨后即有德儀公司和聯信公司(后與霍尼韋爾合并)在各自的制造流程全面推廣六西格瑪質量戰略。
但真正把這一高度有效的質量戰略變成管理哲學和實踐,從而形成一種企業文化的是在杰克?韋爾奇領導下的通用電氣公司。
該公司在1996年初開始把六西格瑪作為一種管理戰略列在其三大公司戰略舉措之首(另外兩個是全球化和服務業),在公司全面推行六西格瑪的流程變革方法。
而六西格瑪也逐漸從一種質量管理方法變成了一個高度有效的企業流程設計、改造和優化技術,繼而成為世界上追求管理卓越性的企業最為重要的戰略舉措,這些公司迅速運用六西格瑪的管理思想于企業管理的各個方面,為組織在全球化、信息化的競爭環境中處于不敗之地建立了堅實的管理和領導基礎。
六西格瑪改善方法論的典型步驟是D-定義、M-測量、A-分析、I-改善、C-控制;而用于研發設計的典型步驟是D-定義、M-測量、A-分析、D-設計、V-驗證或I-識別、D-設計、O-優化、V-驗證。
其后,六西格瑪在GE取的成功更是將其推向了學習熱潮。
從歷史來看,精益生產有著近70年的歷史,從而形成了至今完善的管理系統。Motorola在提出六西格瑪概念至今,也有了20年的歷史。
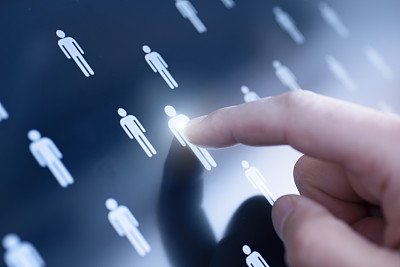
03思想系統比較
1、精益生產的起源歷史環境就注定了它是一種系統的管理方法。從50年代豐田英二參觀了福特當時世界最大的汽車生產廠后,“價值”二字就變成了精益生產的核心。
在希望“工廠每天的每一個工作都在創造價值”的思想支撐下,七大浪費(超量生產、不良品、庫存、搬運、多余的動作、等待、多余的工序)被提了出來,而此七大浪費,簡單到可以使一線員工很容易就理解其工作中的浪費,而公司高層管理者,則又可以從戰略層面來進行消除七大浪費的活動。
豐田公司為了使自己的小工廠能快速應對市場的需求和反應,從50年代起,就堅持實行按照客戶定單來生產,這便是后來拉動生產的思想起源。
只有按照客戶定單從事生產活動,才不會有多余的庫存。
當供應商被要求進行也按照這樣的方式進行生產時,戰略供應鏈從這個時候便開始建立起來了,直至后來發展到讓客戶參與設計的管理活動中來。
為了消除七大浪費,于是JIT(JustInTime)的生產方式被提了出來,并在豐田得以成功的運用,快速換模并是JIT里面誕生的一個有效工具。
JIT在消除庫存(含在制品)和生產平衡方面有著與傳統流水方式截然不同的效果。
為了改善質量和降低成本,QCC活動開始在工廠進行,并取得了很好的效果,當QCC被全面推廣,應用到操作員級別的時候,全面質量控制(TQC)和零缺陷(ZD)運動被全面展開,品質管理的七大手法也在這個時候被得以運用到極致。
隨后將TQM的思想又運用到提高設備效率之上,TPM在日本電裝取得的成績使TPM又成為了精益生產系統中一個強大的管理工具。
整個精益生產的思想都是圍繞著“價值”來思考,“價值流設計”是在八十年代被豐田公司用來進行供應鏈改善的工具。
以“價值流”為核心的精益生產方式在工廠運營管理、銷售和供應商管理方面整合成為強有力的戰略供應鏈。
而支撐精益生產得以不斷創新和延續的一個核心便是“持續不斷的改善”,在日語里常用“Kaizen”一詞來表達這個意思。
正如豐田社長渡邊捷昭所說“豐田公司內部并不是提倡用數字和條條框框進行管理的。
因為,豐田畢竟是從日本發展起來的,管理過程中的量化流程是西方的東西,我們更強調一種思維,即持續研究和創新的思維。”
文章來自網絡,版權歸作者所有,如有侵權請聯系刪除
“感謝冠卓咨詢老師對項目組的全程輔導,通過做項目我們學會了如何用系統科學的方法分析研究問題;開闊了我們的視野并讓我們的管理人員明白了團隊協作的重要性。”
———北京某公司總經理 蘇先生