Standardized Work or Kaizen? Yes
標(biāo)準(zhǔn)作業(yè)還是改善?孰重!
by John Y. Shook? 李兆華 譯
December 12, 2018
https://www.lean.org/LeanPost/Posting.cfm?LeanPostId=986
I encountered a familiar paradox a couple of times this month. You can think of it as a twist on Art Smalley’s Four Types of Problems model. Or you can think of it as a never ending search for balance.
這個(gè)月我?guī)状斡龅揭粋€(gè)熟悉的似是而非說法,你也可把它想象成如Art Smalley的4種問題模式般的糾結(jié)(孰先孰后?),或者你也可以把它想象成一個(gè)無止境地尋求其間的平衡。
At an old-line manufacturing operation in the US Midwest: “We need to break through our constant firefighting and aim for major innovation.” Meanwhile, just one huddle board over, “We’re not ready for improvement, we can’t even maintain the standards we have today.”
在一個(gè)美國中西部傳統(tǒng)的制造業(yè)者認(rèn)為:「我們需從不斷的救火中脫身,并尋求重大的創(chuàng)新。」而同時(shí),面對(duì)種種阻礙又發(fā)覺「我們尚未準(zhǔn)備好改善,我們甚至無法維持我們既有的標(biāo)準(zhǔn)。」
At a large American hospital: “We have so many problems and, worse, we don’t even have clear standards. We need basic stability before we can think of improvement.” Meanwhile, just one huddle board over, “We need to solve some very big problems at the system level before we even bother with the little things.”
一個(gè)大型美國醫(yī)院認(rèn)為:「我們有許多問題,更糟的是我們甚至沒有明確的標(biāo)準(zhǔn)。在思考能做什么改善之前,我們需要基本的穩(wěn)定?!雇瑯拥模诿鎸?duì)種種阻礙時(shí)也發(fā)覺,「在我們傷腦筋于小事之前,我們需要先解決一下系統(tǒng)上的大問題?!?/span>
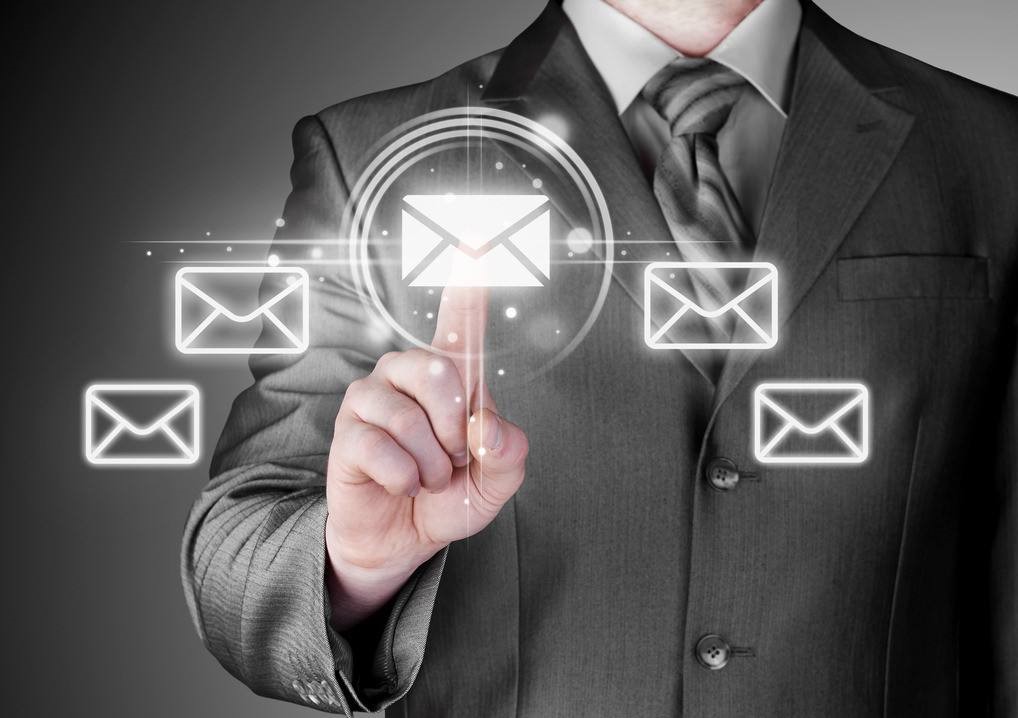
Where do these different views come from? Partly, it’s a matter of starting point – what you see tends to depend on where you sit. But, don’t forget to add a healthy dose of personal predilection. Many lean folks LOVE to quote over and over (and over) the Taiichi Ohno observation (Henry Ford said it, too, and no doubt many others) that “there is no kaizen without standards.”
這些不同的看法是來自于何方?有一部分是從哪里開始的問題,根據(jù)你的所在,看到不同的趨勢(shì)。但是別忘了加上一些自己的偏好。許多精益中人喜歡大野耐一一直重復(fù)著的觀察(亨利 福特與其他許多人也都說過),「沒有標(biāo)準(zhǔn),即無法改善!」
It is less noted but equally true that “there is no maintenance of standards without kaizen.” (There is no steady state. Anywhere, ever. You are either progressing or declining. Get used to it. For more on this, click here to see my 2009 series of posts about standardized work.)
一樣正確,但卻少被注意的是「若無改善,即無法維持標(biāo)準(zhǔn)。」(任何地方、任何時(shí)候都沒有穩(wěn)定的狀態(tài),你得習(xí)慣于要不是在進(jìn)步,就是在退步。你可在2009年的連結(jié)中找到我更多的論。2009 series of posts about standardized work.)
The fact is that you want both, and you can’t have much of one without a roughly equal dose of the other. But, the timing of emphasizing one (maintaining standards) versus the other (improvement or kaizen) typically varies greatly over time. And, over time, while you’d like to see them appearing in equal dosages, most of the time one will be outweighing the other. It’s like a teeter-totter. With a kid on each side, bouncing each other up and down. Then they get the idea to try to balance each other. They can do it if they’re roughly the same size. If not, they can adjust by scooting themselves up or down their side of the teeter totter. But, it takes some finagling. And before long, one of them will break formation and they’ll teeter again.
事實(shí)上,你想要兩者,你無法得到一方多些,卻不得不得到相同的另一方。但是要強(qiáng)調(diào)的是一方(維持標(biāo)準(zhǔn))或另一方(改進(jìn)或改善)的時(shí)機(jī)卻有很大的差異。長期來說,你會(huì)看到兩者似乎是一樣的重要,但大部分的時(shí)間里,他們的比重并不一樣。它就像一個(gè)蹺蹺板,小孩分據(jù)兩邊,彼此上下彈跳。他們想要試著讓蹺蹺板獲得平衡,如果他們的體重相近,則容易做到。如果不是這樣,他們可以調(diào)整他們?cè)谲E蹺板上的位置,但這需要一些技術(shù)。不久,其中一人可能又會(huì)破壞平衡,他們又開始上下彈跳了。
This is true even at Toyota. When Toyota brought its production and management systems to North America, the emphasis of kaizen versus standardized work varied substantially between NUMMI, which came first, and the plants in Kentucky and Ontario. It varied with the problem that needed solving. At NUMMI, the workforce was a grizzled assemblage of ex-GM or Ford UAW members. These folks had habits, formed from many years of working in the old Detroit Three system. Engineers would design the work, workers would try to do the work as designed, whether the design was good or not. When it wasn’t designed well the workers would come up with workarounds of one sort or other. Sometimes the workaround was a good improvement (kaizen, even), other times it was just a patch. A way to get through the day without hurting yourself, or without the discrepancy from the process design intent (if there really was one) being discovered by a supervisor or quality inspector. As a result, the steps being performed out on the plant floor were a cacophony – far from the ideal harmonious symphony – of work procedures that resulted in the poor quality (and poor productivity) that US automakers were famous for at the time. Workers weren’t asked for their ideas or contributions and workers didn’t offer them. Just do your job. Make it look like it’s the job as designed by engineering. And do it over and over, all day every day, year after year.
即使在豐田,當(dāng)豐田向北美導(dǎo)入其生產(chǎn)與管理系統(tǒng)時(shí)也是這樣,它對(duì)首先的NUMMI,與其后的肯塔基Kentucky與安大略O(shè)ntario,對(duì)改善與標(biāo)準(zhǔn)作業(yè)的強(qiáng)調(diào)有相當(dāng)大的不同。那是因?yàn)樗麄円鉀Q的問題不同。在NUMMI其勞動(dòng)力是高齡的前通用或福特的工會(huì)會(huì)員。他們有其慣性,僵化于長期在底特律三大系統(tǒng)中的工作方式。工程師會(huì)設(shè)計(jì)工作方法,不論這方法好或不好,作業(yè)者就試著照著所設(shè)計(jì)的方法去工作。如果工作設(shè)計(jì)得不好,作業(yè)者就會(huì)想辦法權(quán)變一下。有時(shí)候權(quán)變是好的改進(jìn)(或改善),但有時(shí)候它卻只是應(yīng)付性的補(bǔ)綴,只要這方法過得了今天,不要受傷就好,或者不要與其原來的期待有所偏差(如果真有這樣的方法),而不會(huì)被班長或質(zhì)量檢查員發(fā)現(xiàn)就好了。結(jié)果在現(xiàn)場(chǎng)的作業(yè)步驟充斥著不協(xié)調(diào),作業(yè)節(jié)奏根本不和諧,導(dǎo)致當(dāng)時(shí)美國汽車制造商聞名的質(zhì)量不良(與低落的生產(chǎn)力)。作業(yè)者不會(huì)被征求意見或是被要求協(xié)助,當(dāng)然作業(yè)者也不會(huì)提出。只要把你的工作作好就好了。大家就裝著是照著工程部門所設(shè)計(jì)的方法工作。整天的重復(fù)著、每天、每年。
So, entering into that environment at the former GM Fremont plant, Toyota stressed the importance of kaizen, both the term and the fact of it. If you see a problem or opportunity, take action (NOW!) to make a change. Don’t sweat too much over the change, don’t chase tons of data and get stuck in analysis paralysis (no overwrought ROI calculation, please), just try and adjust.
所以當(dāng)豐田進(jìn)入NUMMI,前通用費(fèi)利蒙工廠時(shí),強(qiáng)調(diào)改善的字義與內(nèi)涵的重要性。那就是,當(dāng)你看到問題或機(jī)會(huì)時(shí),立刻(不遲疑地!就是現(xiàn)在?。┎扇⌒袆?dòng)來改變。別想一次做太多的改變,別想得到太多數(shù)據(jù)而陷入分析癱瘓(請(qǐng)別過度沈溺于投資報(bào)酬率的計(jì)算),盡管去試驗(yàn)與調(diào)整。
'So, what is your starting place? Are you stuck in stability, the effort of striving for a stable condition that never comes? Or are you making random change for the sake of change that leads to problems repeating over and over?'
因此,什么是你的起點(diǎn)?你是深陷于穩(wěn)定的迷思之中,努力于永遠(yuǎn)無法達(dá)成的穩(wěn)定狀況嗎?或者你只是為改變而做些凌亂的改善,導(dǎo)致問題不斷地重復(fù)出現(xiàn)。
I recall, very early on, a fierce argument breaking out between some workers and engineers. “It’s all about kaizen and continuous improvement,” said one. “No, don’t fix it if it ain’t broke!” argued the other. To the surprise (at that time, early 1984, none of us knew what to expect as TPS was introduced on a large scale for the first time to an American workforce) of a Japanese Toyota manager I was close to, the stances taken by the protagonists was the opposite of what he expected. It was the worker who was all for “continuous improvement” and the engineer who didn’t want to “fix it if it ain’t broke.”
我回想起很早期(在1984年初,我們不知道對(duì)于首次如此大規(guī)模的對(duì)美國勞動(dòng)力導(dǎo)入豐田生產(chǎn)方式,應(yīng)有什么期待?。谀承┳鳂I(yè)者與工程師之間,曾發(fā)生過的激烈爭(zhēng)論。有人說:「得進(jìn)行改善與持續(xù)改進(jìn)」。另一個(gè)人認(rèn)為:「不!若沒壞掉,就不必修理」。我所熟悉的日本豐田課長對(duì)這對(duì)話的主角的預(yù)料完全相反。作業(yè)者想要「持續(xù)改進(jìn)」,而工程師卻不想「修它,除非它壞掉了」。
In that environment, overall, the experienced UAW workers knew how to perform a job to the engineering specs as provided them. What was needed, and had been missing when GM ran the place, was a kaizen mindset amongst everyone – workers, supervisors, and engineers alike. That was the problem we had chosen to solve.
當(dāng)時(shí)的狀況,是有經(jīng)驗(yàn)的UAW作業(yè)者知道如何達(dá)成被要求的工程規(guī)格。需要什么?但當(dāng)通用營運(yùn)這工廠時(shí),卻錯(cuò)過了!應(yīng)該是在每個(gè)人---作業(yè)者、班長、與工程師-心中都有的改善企圖,這是當(dāng)時(shí)被我們選擇要解決的問題。
In Kentucky, on the other hand, the workforce was a diverse assemblage of individuals from a wild variety of work environments. From school teachers to grocery store cashiers, most had never worked in the auto industry. So the first order of business was to get everyone up to speed learning the fundamentals of performing a factory job. With these conditions, simply performing the work to a basic standard was already a stretch goal, and an absolutely critical one.
但另一方面在肯塔基,勞動(dòng)力是由來自于各種不同工作環(huán)境的人所組成。從學(xué)校老師到雜貨店的收銀員,大部分的人都不曾在汽車產(chǎn)業(yè)工作過。所以最急迫的問題,是讓每個(gè)人都能快速地學(xué)習(xí)如何執(zhí)行工廠工作的基本事項(xiàng)。在此狀況下,光是要他們能夠根據(jù)基本的標(biāo)準(zhǔn)執(zhí)行工作,都是一個(gè)有難度的目標(biāo),但也是非常重要的目標(biāo)。
That’s why, to this day, if you encounter an ex-NUMMI employee and then an ex-Kentucky or Ontario employee, you’ll likely hear a different nuance in their language, and you may notice an associated mindset, regarding standardized work and kaizen. The gap is one that is easily bridged on the surface, usually by invoking the aforementioned adage of Mr. Ohno’s – “without standards, there is no kaizen” – an invocation that usually works well enough.
這就是為什么直到今天,當(dāng)你遇到前NUMMI員工或前肯塔基或是安大略的員工時(shí),你會(huì)聽到他們言談中微細(xì)的差異,同時(shí)你會(huì)注意到這反映在他們對(duì)標(biāo)準(zhǔn)作業(yè)與改善的心態(tài)。其間的差異可以很容易地在表面予以連結(jié),只要提起大野先生所說的:「沒有標(biāo)準(zhǔn),即無法改善。」經(jīng)常就能說得通了。
But, in fact, the difference in nuance derives from a different starting place which does indeed matter. The difference in spirit of “don’t overanalyze, just try” versus “first gather baseline data and develop your hypothesis to test against” is easy to ignore or trivialize. So, what is your starting place? Are you stuck in stability, the effort of striving for a stable condition that never comes? Or are you making random change for the sake of change that leads to problems repeating over and over?? Back to the teeter totter. Don’t expect perfect balance. Even as that balance is precisely what you strive for. I hope that doesn’t sounds too “zen,” but I think that is indeed the spirit that helps keep us on the road to continuous improvement without end. Specific steps and approaches depend on your starting place versus your desired end goals (back to the Lean Transformation Framework and Art Smalley’s Four Types of Problems). Balance: don’t expect to achieve it, but don’t stop striving for it.
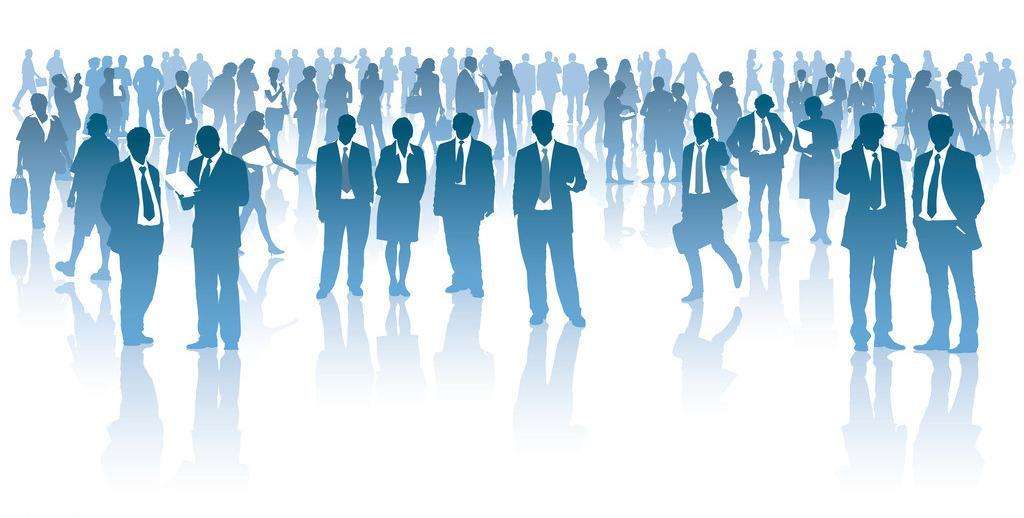
但是事實(shí)上,言談中細(xì)微的差異源自于很重要的不同的起點(diǎn)。「別過度分析,就去試吧!」與「首先取得基本數(shù)據(jù),作出假設(shè)再去試驗(yàn)?!沟牟顒e常被忽略或低估。因此,什么是你的起點(diǎn)?你是身陷于穩(wěn)定的迷思之中,努力于永遠(yuǎn)無法達(dá)成的穩(wěn)定狀況嗎?或者你只是為改變而做些凌亂的改善,導(dǎo)致問題不斷地重復(fù)出現(xiàn)。讓我們?cè)倩氐杰E蹺板。別期待完美的平衡。即使你努力于精確地平衡。我希望這不會(huì)聽起來有點(diǎn)像是禪學(xué),但我想的確是這樣的精神,幫助我們維持在無止境的持續(xù)改善正道上。所需的步驟與方法得視你的起點(diǎn)與你想達(dá)到的目標(biāo)(回歸精益轉(zhuǎn)型框架與Art Smalley的Four Types of Problems)。平衡:別認(rèn)為你做得到,但也別停止追求。
文章來自網(wǎng)絡(luò),版權(quán)歸作者所有,如有侵權(quán)請(qǐng)聯(lián)系刪除
感謝冠卓咨詢老師對(duì)項(xiàng)目組的全程輔導(dǎo),通過做項(xiàng)目我們學(xué)會(huì)了如何用系統(tǒng)科學(xué)的方法分析研究問題;開闊了我們的視野并讓我們的管理人員明白了團(tuán)隊(duì)協(xié)作的重要性。
——北京某電器公司