搞精益生產,一定會用到建議系統。但是從管理實踐上來說,運用成功的并不多。大概歸納一下,主要是以下幾個原因。
1、忽視中國人和日本人思維方式的不同,硬搬日本人那一套。
2、負責的人沒經驗,不知如何下手,掛幾個建議箱,收集各種意見而已。
3、咨詢工程師,沒有實際運營經驗,憑想象做事。
舉個例子,我見過一個工廠,顧問公司的工程師說要收集員工建議,于是他們就掛了好多建議箱,規定員工每周必須提交兩個改善建議。第一次收來了幾百條建議。整理以后,里面20多條說廁所里要養盆花;30多條說食堂每天要供應魚頭;還有說工廠門口的樹不好看要砍掉,等等等等。。。這些建議不應對,則以后沒人再提建議,全部應對要占用大量的管理資源,本來很好的一個事情,變成了打自己的臉。
這個工廠的老板和他聘請的顧問,根本就沒搞清楚建議系統怎么運行的,就望文生義,以為掛個建議箱,制定處理建議的程序,建議系統就能好好運行了。實際上這樣的建議系統還不如沒有。
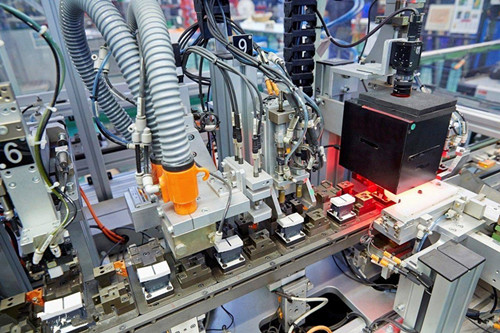
下面再說說,我所知道的運行良好的建議系統。
首先,建議系統建立前,員工和管理者必須是經過TPS知識培訓的,只是在不同崗位,培訓的范圍不同。第二,建議是指定范圍的。第三,前期是要有老師充分引導,第四、有些建議的方法是指定的。
建議的范圍,不要望文生義,不單是指在什么事情上的建議,而且改善的方法也有限制,否則改善很可能會倒退。在初期,提什么樣的建議,都是管理者指定的,養成習慣以后,再放開提建議。
初期管理者指令性的要求提出建議,范圍一般如下:
1、跟部門KPI相關的。如下一季度,部門生產力指數上升20%,DCT時間降低20%,庫存周轉率增加一倍。我要改善什么?這時,部門把任務分解給下面的小部門,為了完成KPI,下面每個小部門必須提出幾個建議。這些建議里面,使用方法是指定的,必須是豐田的改善十二種工具。
2、跟CT有關的。我們改善,一般會盡量縮短CT,拉長TT。這種建議就會分解給各班組。其他生產支援的部門,如管設備的部門,建議就是換模時間縮短,更好的保養方法等等,也歸到這一類。
3、跟安全有關的。
4、其他改善無關的,都交給行政部門處理。
這里很容易看出,沒有前期培訓,初期指導,必然會走偏。我現在所見過的顧問公司的人,一般都是工程師出身,沒有實際運營經驗,在這種事情上沒有指導的能力。所以,大部分建議系統,最后都不了了之。
文章來自網絡,版權歸作者所有,如有侵權請聯系刪除