從根本上講,杜絕浪費(fèi)任何一點(diǎn)材料、人力、時(shí)間、空間、能量和運(yùn)輸?shù)荣Y源,是豐田精益生產(chǎn)方式最基本的概念。
豐田公司一直把浪費(fèi)歸結(jié)為:過多、過早制造造成的浪費(fèi);直接導(dǎo)致庫存的浪費(fèi);質(zhì)量問題造成的浪費(fèi);生產(chǎn)線上等待造成的浪費(fèi);物件搬運(yùn)造成的浪費(fèi);加工造成的浪費(fèi);多余動(dòng)作造成的浪費(fèi)。這些浪費(fèi)主要發(fā)生在生產(chǎn)現(xiàn)場。在生產(chǎn)現(xiàn)場,解決了所有的浪費(fèi)問題,就達(dá)到了精益化生產(chǎn)方式的目的,也就能實(shí)現(xiàn)利潤的最大化。TPS使得豐田的生產(chǎn)成本壓到了最低。
一汽集團(tuán)副總經(jīng)理安德武曾告訴記者,在一汽豐田廠房參觀,他發(fā)現(xiàn)整個(gè)車間里竟然沒有一把扭矩扳手。豐田的人員解釋說,在標(biāo)準(zhǔn)化培訓(xùn)中,員工已經(jīng)能夠用普通扳手解決扭矩扳手的問題,再配備扭矩扳手已經(jīng)是浪費(fèi)了。也正是因?yàn)槿绱?,今?月開始,一汽集團(tuán)在生產(chǎn)部大規(guī)模開展了《推進(jìn)TPS工作方案》,推廣對象包括解放、紅旗、馬自達(dá)6、豐田越野車等分公司的生產(chǎn)線。
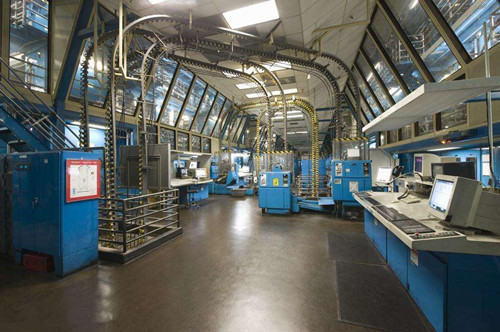
TPS到底有多神?
一汽給出的實(shí)例是:以庫存管理為例,一汽豐田平均庫存為1.5天,而解放的平均庫存為1.5個(gè)月,是一汽豐田的30倍,僅此一項(xiàng)解放的財(cái)務(wù)成本一年就要多花1.8億元。
另外一個(gè)流傳頗廣的例子是:改善前的紅旗生產(chǎn)車間里,裝備一輛紅旗的輪胎至少走動(dòng)60米,耗時(shí)90秒,用豐田方式改善后,裝備一輛車少走了31米,節(jié)約52秒。按照每日裝配55輛計(jì)算,一天少走1750米,少耗時(shí)38分鐘。這樣,每個(gè)班組從11個(gè)人減少到9人,生產(chǎn)時(shí)間從14分鐘降低到9分鐘,班產(chǎn)從30輛提高到45輛。但是與此同時(shí),豐田精益生產(chǎn)方式在中國并不被所有人認(rèn)同。
對接沖突
事實(shí)上,不僅是在中國,TPS的對接沖突在豐田走向全球的同時(shí)就廣泛存在。其最根本的原因在于日本資源匱乏土壤中產(chǎn)生的TPS與其他國家的文化注定有沖突。但是,在歐美國家,由于豐田是獨(dú)資廠,很多問題就相對容易解決。但是,對一汽豐田和廣汽豐田而言,情況卻有很大不同。執(zhí)行TPS的一個(gè)直接結(jié)果是,生產(chǎn)時(shí)最大限度地利用人力,原來10個(gè)人干的活現(xiàn)在6個(gè)人就能干,這樣,事實(shí)上也就造成一批工人下崗。這也是豐田TPS“中國水土不服”說法的起源。
即使是在大野耐一時(shí)代,TPS也提倡修改工具和提高設(shè)備,完成精益化生產(chǎn),也就是說,TPS顯然必須武裝成更現(xiàn)代化的設(shè)備才能保證生產(chǎn)。在中國,顯然沒有達(dá)到這樣的標(biāo)準(zhǔn)。和日本及歐美國家不同,中國的勞動(dòng)力成本低下,設(shè)備不足的問題就可能用加強(qiáng)工人勞動(dòng)強(qiáng)度的辦法來解決。
天津一汽豐田一位內(nèi)部人士向記者透露:在天津工廠,一部分工人們雖然表面上沒有什么反應(yīng),但事實(shí)上都在消極地抵抗TPS。在第二工廠,一些汽車零配件甚至在從儲(chǔ)備倉庫運(yùn)往總裝車間的過程中,就會(huì)丟失。雖然一汽豐田和豐田中國事務(wù)所公關(guān)部門都否認(rèn)這樣的事件在發(fā)生,但是,這些丟失的汽車零配件卻屢屢在北京等地的汽配城中出現(xiàn),并以低于豐田4S店一倍甚至幾倍的價(jià)格銷售。該人士稱,和其他合資汽車工廠的工人相比,工人們認(rèn)為自己“干的多,掙的少”。另一方面,站在豐田的立場上,部分中國工人的業(yè)務(wù)素質(zhì)是TPS在中國推行的一大門檻。“豐田有自身的問題,但是,有些工人還有‘吃大鍋飯’的心理?!必S田中國投資有限公司一位不愿意透露姓名的中層管理人士說到。他解釋,TPS加劇了員工之間的競爭,一汽豐田也長年在招工人,年齡大的工人顯然面臨被淘汰的命運(yùn),他們的怨言自然很多,質(zhì)疑TPS的聲音也就很多。他認(rèn)為,問題不在于TPS,而在于TPS和中國文化銜接時(shí)出了問題。
從最早進(jìn)入中國制造業(yè)到現(xiàn)在,豐田TPS精益生產(chǎn)方式在成為國內(nèi)企業(yè)學(xué)習(xí)的榜樣已有不短時(shí)間。每個(gè)國內(nèi)企業(yè)都希望通過學(xué)習(xí)TPS,提高自己的生產(chǎn)能力,形成具有自己企業(yè)特色的生產(chǎn)方式。然而國內(nèi)企業(yè)能否學(xué)到豐田精益生產(chǎn)方式的精髓,達(dá)到他們的水平,這個(gè)還需要國內(nèi)企業(yè)認(rèn)真對待,堅(jiān)持探索。
文章來自網(wǎng)絡(luò),版權(quán)歸作者所有,如有侵權(quán)請聯(lián)系刪除