中國中小企業易“短壽”,這是不爭的事實。
從20世紀年80代末到90年代初,中國市場創造了世界經濟發展上的一些神話?!叭辍?、“巨人”、“飛龍”和“太陽神”等一大批企業以令人咋舌的速度日長夜大,成為名噪一時的“企業巨人”,然而,這些“明星”們如今大都風光不在,人們用“只領風騷兩三年”來表達對這些昔日“經濟恐龍”的惋惜,據有關部門調查顯示,目前,我國68%的中小企業的生命周期都不超過5年。然而,現在市場環境卻還在進一步惡化。利潤空間越來越小,很多企業都低于5%了;但是原材料等價格卻一直在上升,過去三年中,很多原材料的價格就翻了一倍多;勞動力成本也在快速上升,比如在深圳地區,過去的五年中,人工成本已上升50%;加上人民幣升值對出口加工企業也是很大的成本的壓力,很多企業可以說是在水深火熱中了。中小企業如何在現在激烈競爭的環境下生存下來,并壯大發展呢?我認為通過實施精益生產,可以很好地解決這個問題。
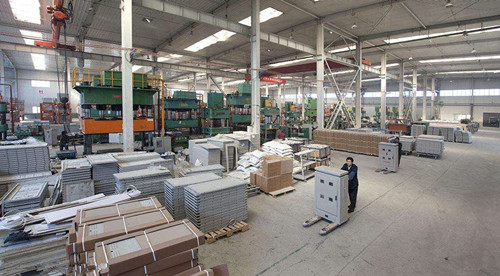
豐田汽車公司從一個很小的作坊式的企業,卻能成長成為汽車行業的領先者,其主要因素就是由于豐田汽車公司實行是是一種與傳統大批量生產方式完全不同的方式-豐田生產方式(精益生產在豐田的叫法)。從豐田公司的成功,我們可以有很多借鑒。
豐田公司在1937成立的時候,只是個年產量只有4000輛的手工作坊式的工廠,整個日本汽車市場都有是美國的通用和福特的天下。尤其是在1949年,日本轉入戰后經濟恢復期,豐田更面臨著極大的生存危機,當時日本汽車業的勞動生產率還不到美國的九分之一。但是豐田生產方式的創始人-大野耐一認為,并不是美國人付出了日本人10倍的體力,一定是日本人在生產中存在嚴重的浪費和不合理現象。只要消除了這些現象,勞動生產率就應該成為現在的10倍。這種理念就是以后發展成的最具革命性的生產管理方式-豐田生產方式的出發點,而支撐這種思想的的兩大支柱是“JIT”和“自動化”。從此,豐田走向一種徹底消除浪費,創造價值之路。到了1982年,與美國通汽車相比,勞動生產率的比例完全顛倒過來了,這一年,通用人均生產6輛汽車,而豐田卻達到了55輛。人均創利,通用汽車是人均利潤是1400美元,而豐田汽車人均利潤是14000美元。現在的豐田繼續保持著良好的發展勢頭,2006年的盈余高達140億美元,比美國三大汽車公司贏利總和還高。
其實我國的中小企業現在的處境跟豐田成立之初很類似,都是在買方市場多品種,小批量的環境下激烈的市場競爭,企業決勝的核心是質量,成本,交貨期,和服務。所以很有必要研究豐田是如何在當初其實更惡劣的市場環境下生存發展的。豐田生產方式之所以能對豐田的發展起那么大的作用,是因為其里面的理念是跟我們傳統的管理思維是不一樣,更符合現代的市場環境,主要體現在下面幾點:
1.小批量也能實現低成本。而傳統上我們認為只有大批量才能降低成本,這其實是個錯覺。通過消除浪費,增加增值率,小批量也能實現低成本。
2.高品質也能實現低成本。而傳統上我們認為高品質意味著高投入和高成本。通過運用一些防錯設計,團隊作業,目視管理等精益工具,可以實現低成本,高品質。
3.設備并不要追求新,高速度,合適就好。只要能按客戶需求的節拍生產就行。而傳統上我們認為設備越新越好,速度越快越好。設備新/高意味著產能也大,若客戶的需求沒有增加,設備新/高只會增加折舊,維護等的費用。即便現在的豐田,一些五六十年代的設備還在繼續使用著。
4.交貨期越短,成本越低,傳統上我們對認為交貨期對成本的影響不大。其實交貨期的財務杠桿作用很大的,一般來說,交貨期縮短50%,間接制造成本,管理費用就可以下降20%。
以上幾點,其實有個共同的地方,其實是不追求硬件的投入,而是要充分發揮人的作用。通過消除浪費,使成本下降,人的價值創造率上升。
現代企業競爭的核心是人,我國中小企業想要實現基業長青,其實也是要靠發揮人的作用,而不是靠增加硬件的投入來實現的?,F在的市場競爭的核心主要是在成本,質量,交貨期,服務這幾個方面。通過實施精益生產可以在這幾個方面得到很大的改善。
文章來自網絡,版權歸作者所有,如有侵權請聯系刪除