精益生產(chǎn)模式過時(shí)了嗎?它到底面臨著怎樣的困境?豐田能否妥善解決召回背后的問題?對(duì)中國企業(yè)而言,還要不要采用“精益生產(chǎn)模式”?豐田召回事件發(fā)生后,人們的第一反應(yīng)往往是去關(guān)注讓豐田取得巨大成功和聲譽(yù)的“精益生產(chǎn)模式”。記者對(duì)話汽車專家鐘師,試圖找到答案。
記者:豐田精益生產(chǎn)模式強(qiáng)調(diào)在生產(chǎn)過程中進(jìn)行質(zhì)量監(jiān)控和管理,并誕生了“拉繩停止生產(chǎn)”的模式,而不是在生產(chǎn)結(jié)束后檢驗(yàn),因而次品率一直是行業(yè)里最低的。但以管理見長的豐田這次卻偏偏出現(xiàn)了800萬輛的質(zhì)量問題,您認(rèn)為豐田的哪個(gè)環(huán)節(jié)出了問題?這是汽車大制造不可避免的問題嗎?
鐘師:TPS(豐田生產(chǎn)方式)的起源是圍繞著整車制造環(huán)節(jié)的全方位的精益管理,現(xiàn)在已經(jīng)延伸到研發(fā)環(huán)節(jié)和供應(yīng)鏈環(huán)節(jié)等。全球所有的汽車巨頭或多或少都曾不斷卷入到召回事件中,豐田也不例外,從召回角度看,這次的豐田大規(guī)模召回事件與其他企業(yè)并沒有本質(zhì)的不同,表象的差異之處在于,豐田的產(chǎn)銷量達(dá)到同行中最大,車型種類也最多,從壓縮成本上通過多種車型共用通用性零部件做得也最徹底,這樣一來,一旦某一部件因設(shè)計(jì)或工藝上存在缺陷,或者對(duì)供應(yīng)鏈管理控制上有任何疏漏,波及到的車型數(shù)量會(huì)比其他企業(yè)更大,對(duì)消費(fèi)者的影響也更大。
全球化整車制造和零部件供應(yīng),各種車型的零部件大比例地通用化,這是任何企業(yè)要成為全球巨頭的必經(jīng)之路,但也是具有一定的管理風(fēng)險(xiǎn)的,所以這對(duì)汽車巨頭企業(yè)是一個(gè)極大的管理挑戰(zhàn),這種難度已經(jīng)超出了幾十年前所形成的TPS的概念范疇。
記者:豐田的精益生產(chǎn)作為全球企業(yè)的標(biāo)桿管理模式,在經(jīng)歷這次召回事件后,您認(rèn)為這種模式本身過時(shí)了嗎?
鐘師:TPS的哲理和精髓至今還是行業(yè)中的“圣經(jīng)”和從業(yè)人員的必修讀本,問題在于TPS的目標(biāo)是針對(duì)每一座工廠如何實(shí)行效率最大化和成本最低化,幾十年前形成的TPS不可能完全適用于當(dāng)今汽車巨頭企業(yè)如何在全球化過程中的全面精益管理,時(shí)代不同,工具不同,面臨著新問題和新挑戰(zhàn)必須啟用新的解決方式,但在企業(yè)快速擴(kuò)張的過程中,確實(shí)來不及沉淀總結(jié)歸納出更新的解決方案,因此,對(duì)單體工廠的管理,TPS思想仍然有效,對(duì)企業(yè)全球化經(jīng)營,TPS已力不從心。
豐田所做的,正是大眾、通用等巨型企業(yè)也正在做的,即車型平臺(tái)化,零部件通用化,無非豐田剛成為行業(yè)最大,出的問題也會(huì)最大,豐田面臨的問題其他企業(yè)也無法回避。這次事件是個(gè)警鐘,所有做全球化經(jīng)營車車企都應(yīng)自省、自糾,防患于未然。
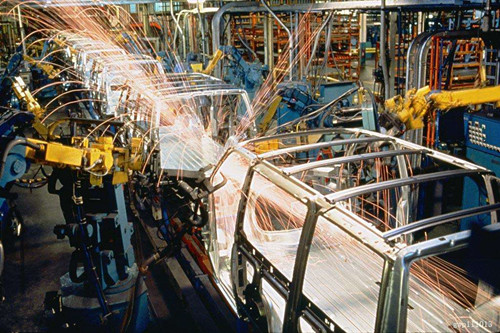
記者:精益生產(chǎn)目前在中國車企中推廣的現(xiàn)狀如何?哪些企業(yè)做得比較好?目前來看,在實(shí)施過程中碰到的主要問題有哪些?
鐘師:相對(duì)來說,對(duì)于精益生產(chǎn)的重視和實(shí)踐,合資企業(yè)普遍比國內(nèi)企業(yè)做得要好,合資企業(yè)中日系企業(yè)比歐美系汽車做得要好,因?yàn)闅W美企業(yè)早在上世紀(jì)的八九十年代就開始認(rèn)真研究TPS,盡量縮短與日本企業(yè)的效率與成本上的競(jìng)爭差距。中國企業(yè)相對(duì)而言管理粗放,由于車市幾次爆發(fā)性的增長,機(jī)會(huì)多多,國內(nèi)車企著重盡快擴(kuò)張,搶占市場(chǎng)良機(jī),一時(shí)顧不上對(duì)企業(yè)實(shí)施全面的精益管理。我認(rèn)為,只有等到市場(chǎng)滯漲,企業(yè)成本壓力越來越大,企業(yè)只能壓縮制造和管理成本時(shí),才會(huì)真正重視精益管理。
記者:中國汽車銷量已經(jīng)超越美國成全球第一,中國車企的生產(chǎn)量也超過了日本,作為汽車大國,中國在汽車生產(chǎn)管理上您覺得適合采用哪種模式?
鐘師:表面上看,由于經(jīng)濟(jì)危機(jī)導(dǎo)致西方車市暫時(shí)下挫,中國新車產(chǎn)銷量暫時(shí)成為世界第一,但是要看到中國新車產(chǎn)銷量中,乘用車中合資品牌占據(jù)大頭,高端商用車上采用外國先進(jìn)部件的比例也更高。從產(chǎn)業(yè)價(jià)值鏈上看,中國本土整車企業(yè)和零部件企業(yè)仍處在弱勢(shì)地位。企業(yè)管理的粗放型依然普遍,跑冒滴漏了許多利潤,品牌溢價(jià)能力差,產(chǎn)品銷售獲利能力就低,總之,企業(yè)的盈利能力不足,品牌價(jià)值提升需要許多年的積淀,無法一蹴而就,只有先靠管理上求效益,所以精益生產(chǎn)和管理對(duì)現(xiàn)階段的中國車企仍然很重要。
記者:您對(duì)精益生產(chǎn)模式的前景怎么看?
鐘師:精益生產(chǎn)方式的思想是放之四海而皆準(zhǔn)的,其精髓就是提高生產(chǎn)效率、杜絕浪費(fèi)、降低可變成本,達(dá)到企業(yè)經(jīng)營的利益最大化,現(xiàn)在精益管理思想已被擴(kuò)展到企業(yè)研發(fā)環(huán)節(jié)、供應(yīng)鏈環(huán)節(jié)和流通環(huán)節(jié),甚至已擴(kuò)散到任何服務(wù)貿(mào)易領(lǐng)域和政府行政管理領(lǐng)域。精益管理思想已經(jīng)成為跨行業(yè)的先進(jìn)管理思想。但是不同國家、不同組織機(jī)構(gòu)和不同企業(yè)還得根據(jù)自身情況來量體裁衣,落實(shí)精益管理,也不能生搬硬套學(xué)表面。
文章來自網(wǎng)絡(luò),版權(quán)歸作者所有,如有侵權(quán)請(qǐng)聯(lián)系刪除