會長和我講過,一個車間標準化是建立在5S基礎上的。簡單一句卻讓我思考很多,要做任何事都要有個開始,做好標準化要建立起車間的5S管理,有個目標,做到標準化車間,還有對中間過程的思考。所以,一個車間想要做到標準化,一定要先知道當前是一個什么狀態,工人的對標準化有概念嗎?標準化能給他們帶來實地的好處嗎?這些問題需要一個專業的團隊去管理,有至少5年的IE或精益生產的工作經驗的4-5個工程師,讓他們去評估,例如一年后車間的標準化狀態。
接下來,我會詳細描述一下在國企工作時,如何推進標準化。
一般國企車間,尤其是重工業車間,在設備和角落里都有灰和油污,工人操作區域也有很多不知道用不用的東西,搬運路線混亂,有設備使用說明,但是沒有工人作業的SOP。可以概括以下3點:
1. 材料成品倉庫,半成品庫和動線規劃不合理;
2. 在線工裝治具架子或柜子擺放不合理
3. 工人操作手法,換線工法,沒有SOP
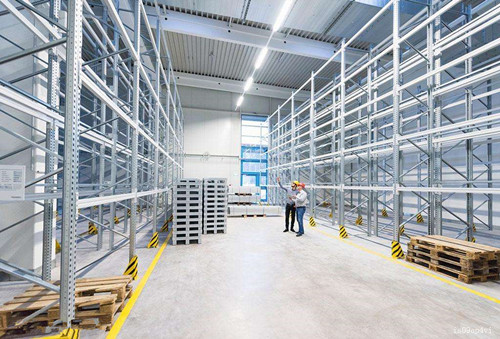
這3點是從面看到點的順序來進行的,所以IE工程師們要先了解整個車間的流程運轉,他們的材料倉,物料辦公室,車間,半成品庫,成品庫,垃圾房,不合格品存放區及功能區辦公室的規劃,用CAD畫個工廠平面圖,4個工程師仔細研習路徑的最短路。或許要搬倉庫,功能區甚至設備,但一定要有一定機動性,不要認為這是最后一次改善了,把所有的線材固定的牢不可破,把倉庫用鋼筋水泥牢牢封鎖,這些不利于有更加優化方案時的變更。或許有人會要求為什么不把未來可能的變動考慮進去,這樣就可以固定了。
但是,我認為,這類看似把事情要求做到極致的人是生產車間的一種威脅,因為生產活動是一項復雜的流程,未來的事情是不可預測,我寧愿要一些見到小問題就可以馬上行動,馬上解決,天天盯住生產線,最后還能把經驗留在紙面的工程師,也不要在天天冥思苦想,為防止未來錯誤的工程師。因為未來不可預知,我們只能通過一個個小的PDCA來解決這些問題,可以在車間內安裝“安東系統”,一個可以快速反應生產問題的系統,便于車間的管理。
然后從面的維度看到線。管理很容易忽略在生產線工裝治具柜子的擺放,因為大多數國企管理者看到生產線和產品,對這些配備的東西,關注很少。這導致柜子的背面窩藏了灰和泥,甚至幾年前的夾具,產品也能找出來。工裝治具從箱子拿出或放入的困難也會讓工人無意間破壞器具。此時,很有必要推行5S,會長在一次討論中說過,推行好前3個S是基礎。我個人很認同這個觀點,3S能做到精益工程師們設定的目標狀態,也是很難的挑戰。一般工人都不會把整理整頓清掃車間各個角落作為自己工作的一部分,這就需要領導們有這個意識,做好3S是工人工作的一部分,是作為績效考核的一部分評估標準。至于,用什么管理方法和工具,我是預測不了的,如同上一段所講,一切管理方法都是要到現場去看才會有對策。但是我會建議管理者們,對3S的管理工作一定要形成日常工作的一部分,除非天災地害,否則不可動搖。
再看SOP,國內企業很少關注工人的操作手法,操作區域的照度,溫度,有的只是“第一步,按紅按鈕,第二步,按藍按鈕,第三步把線裝上……”如流水賬一般,有人會不經意地說:不就是那么做嘛?但是如果深入問,左手做這件事的時候,右手在做什么工作,彎腰的動作是工人問題還是產線設計問題。
類似我問的這些可以問很多很多,精益工程師一樣可以,把人充分利用好,使其有節奏地完成工作,從一人一機實現一人兩機,減少一個工人。有人看到這些方法后可能會走極端,對減人樂此不疲,但是前面說到了“ 有節奏地完成工作”,工人的勞動強度一定要考量,超負荷會引起質量問題,如何恰當的實現減人又不影響質量,才是一個好的SOP樣板。在SOP的制作實現我們期待的目標狀態后,大多數管理者都會看產能問題,或者單位人均產出。
在工程師設定班產量后,管理者都會在一個特定時段去現場看一看是否達標。或者第二天問前一天是否達標,通常實現產能目標后便不再過問。我認為,管理者忽視了每一個產品是否按SOP 標準操作生產出來的。實際生產中有可能出現上午出現異常,導致產能損失,在線班長為達成目標會在下午甚至擠中午吃飯時間去做事,最后也完成了當天的目標。但這是很嚴重的問題遮掩現象,導致管理者對此失去控制,會出現產品質量問題,工人情緒問題。所以一個好的SOP和執行對車間極為重要。
上面3點是我個人的淺見之談。文章里我一直說“狀態”這個詞,因為狀態是一個未來車間生產情形的描述,而且有種狀態應該保持的,沒能保持住狀態,則是后退的。如果把“狀態”換成“目標”,結果會是這樣,一旦車間熱火朝天的完成目標后,很有可能出現倒退,因為目標是一個工程概念,如同完成一項技術研究,完成后投入車間即可,他不會出現倒退。但是,做標準化是一種管理工作,做就是進步,不做不會保持,而是會倒退。
文章來自網絡,版權歸作者所有,如有侵權請聯系刪除