豐田汽車(chē)公司在成本管理方面的經(jīng)驗(yàn)為不同行業(yè)所借鑒。不久前,筆者與豐田通商(新加坡)公司負(fù)責(zé)汽車(chē)零部件和附件業(yè)務(wù)的部門(mén)經(jīng)理趙軍民先生探討一個(gè)話題:日本的人工成本并不比歐美國(guó)家低,其資源成本也不會(huì)比歐美優(yōu)越,可是日本車(chē)的價(jià)格怎么可以比歐美車(chē)便宜那么多?而且還賺錢(qián)不少?
趙先生以自己對(duì)豐田公司的理解,講了這樣一番話:“以豐田公司的JIT(Just In Time)為例,它幫助公司實(shí)現(xiàn)了準(zhǔn)零庫(kù)存,這對(duì)企業(yè)成本的影響非常之大。對(duì)一家生產(chǎn)企業(yè)而言,庫(kù)存的資金占用以及相應(yīng)的成本都是非常高昂的。”
關(guān)于成本的控制,如何降低成本,趙先生進(jìn)一步介紹說(shuō),“豐田控制成本最厲害的一點(diǎn),在于它不是單單從某一個(gè)方面去控制,而是對(duì)整個(gè)供應(yīng)鏈的所有環(huán)節(jié)加以控制。例如,很多企業(yè)常通過(guò)控制員工工資降低成本,然而,人工成本在整個(gè)成本鏈中所占的比例非常低。即使有些企業(yè)里員工工資的比例可以高達(dá)總體成本的10%,如果每個(gè)員工的工資降低5%,總體成本也只能降低0.5%。然而,如果整個(gè)供應(yīng)鏈的每個(gè)環(huán)節(jié)降低5%,那么總體成本也就降低了5%。那就是非常了不起的結(jié)果了。”
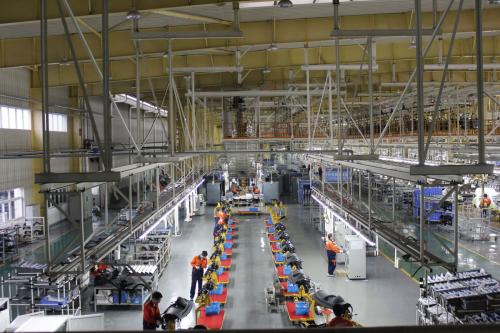
豐田的成功,以至日本汽車(chē)公司的成功,并不只是依靠控制生產(chǎn)過(guò)程或人工,而是通過(guò)控制整個(gè)供應(yīng)鏈的成本而得以實(shí)現(xiàn)的。
以下我們特別介紹豐田公司關(guān)于成本管理方面的一些策略,希望能對(duì)國(guó)內(nèi)塑膠企業(yè)制定成本戰(zhàn)略提供一些啟示。
精益生產(chǎn)
著名的精益生產(chǎn)方式是上個(gè)世紀(jì)80年代豐田公司提出的,基本思想就是Just In Time (JIT),即“只在需要的時(shí)候,按需要的量,生產(chǎn)所需的產(chǎn)品”。但隨著時(shí)間的推移,豐田公司不斷用新的內(nèi)容來(lái)充實(shí)這個(gè)生產(chǎn)方式。
全球車(chē)身生產(chǎn)線(GBL)被許多人認(rèn)為是豐田盈利的秘密武器。它不僅能夠使豐田實(shí)現(xiàn)全球生產(chǎn)設(shè)備、生產(chǎn)工藝流程、質(zhì)量管理三個(gè)標(biāo)準(zhǔn)的統(tǒng)一,而且還能夠根據(jù)不同國(guó)家?guī)垐?chǎng)需求的變化,適量安排生產(chǎn),減少庫(kù)存,節(jié)省開(kāi)支。這條生產(chǎn)線最被人稱(chēng)道的優(yōu)點(diǎn)就是,能夠最大限度地減少成本,提高收益。在這條生產(chǎn)線上,可以進(jìn)行8種車(chē)型的生產(chǎn),而且安裝成本比原來(lái)減少50%,改裝生產(chǎn)新車(chē)型的成本也減少70%,為豐田節(jié)約了大量的成本。
隨后,豐田提出了CCC21(21世紀(jì)成本競(jìng)爭(zhēng)構(gòu)造)計(jì)劃,計(jì)劃把新車(chē)型的關(guān)鍵零部件成本削減30%。
有一個(gè)例子被媒體廣為宣傳:豐田的設(shè)計(jì)師深入研究了大多數(shù)汽車(chē)的車(chē)門(mén)把手,通過(guò)和供應(yīng)商合作,他們把這些把手上的零件從34個(gè)減少到5個(gè),結(jié)果采購(gòu)成本節(jié)約了40%。而且,安裝只需3秒,節(jié)約了75%的時(shí)間。
此外,日本豐田汽車(chē)公司總裝廠與零部件廠家之間的平均距離大約為95公里,日產(chǎn)汽車(chē)公司總裝廠與零部件廠的平均距離大約為180公里,而通用公司則將近700公里。近距離很大程度上降低了物流成本,成為日本汽車(chē)公司供應(yīng)鏈管理上的一大優(yōu)勢(shì)。

消滅浪費(fèi)
豐田公司認(rèn)為,企業(yè)在成本控制這道坎上,通過(guò)原料成本的控制是有限的,而且在鋼材、油價(jià)等各方面因素的綜合影響下,企業(yè)之間成本控制的差別不會(huì)很大。而在生產(chǎn)流程中杜絕浪費(fèi)來(lái)控制成本,有巨大的發(fā)揮空間。
豐田一直把消滅浪費(fèi)作為成本控制的有力武器。在豐田內(nèi)部,浪費(fèi)一般歸結(jié)為:過(guò)多、過(guò)早制造造成的浪費(fèi);直接導(dǎo)致庫(kù)存的浪費(fèi);質(zhì)量問(wèn)題造成的浪費(fèi);生產(chǎn)線上等待造成的浪費(fèi);對(duì)象搬運(yùn)造成的浪費(fèi);加工造成的浪費(fèi);多余動(dòng)作造成的浪費(fèi)。這些浪費(fèi)主要發(fā)生在生產(chǎn)現(xiàn)場(chǎng)。
豐田剛開(kāi)始實(shí)施“精益生產(chǎn)”的時(shí)候,當(dāng)時(shí)汽車(chē)行業(yè)的老大是推崇規(guī)模經(jīng)濟(jì)效應(yīng)的福特。但是豐田的想法和福特完全不一樣,豐田看到的是一個(gè)更大的范圍。“擁有那么多的庫(kù)存,需要人手去管理,或者必須在生產(chǎn)的某一環(huán)節(jié)中等待,這些都增加了成本。尤其如果客戶不需要的話,就會(huì)造成巨額浪費(fèi)。”在豐田看來(lái),單位成本低只是在生產(chǎn)領(lǐng)域。但是對(duì)整個(gè)公司的供應(yīng)鏈來(lái)說(shuō),之后所付出的成本遠(yuǎn)遠(yuǎn)要高于規(guī)模經(jīng)濟(jì)所節(jié)約的成本。
事實(shí)也證明,豐田“精益生產(chǎn)”使其超越福特成為世界第二大汽車(chē)廠商。目前雖然豐田產(chǎn)量還未能趕上通用,但利潤(rùn)卻已經(jīng)是通用汽車(chē)的10倍。
步入21世紀(jì),當(dāng)歐美汽車(chē)制造商紛紛嘗試“以兼并重組增實(shí)力”的強(qiáng)攻戰(zhàn)術(shù)推進(jìn)全球戰(zhàn)略時(shí),豐田卻反其道而行之,推出“CCC21(21世紀(jì)成本競(jìng)爭(zhēng)力建設(shè)計(jì)劃)”,在設(shè)計(jì)、生產(chǎn)、采購(gòu)和固定費(fèi)用四個(gè)方面推行“大規(guī)模壓縮成本運(yùn)動(dòng)”。這個(gè)計(jì)劃實(shí)際上還是繼續(xù)秉承豐田汽車(chē)賴(lài)以發(fā)展的精益生產(chǎn)方式理念。
文章來(lái)自網(wǎng)絡(luò),版權(quán)歸作者所有,如有侵權(quán)請(qǐng)聯(lián)系刪除