首先聲明,這個不是討論法規規定每周上班幾小時的工時!
我記得開始工作(IE工程師)的第一份任務就是在產線做作業工時量測,現在回憶起來還歷歷在目。當時很努力的想要在新任務上展現自己所學,一方面是自己在大三的專題是做工時相關的題目,同時也覺得這個是個很簡單的任務,應當可以給老板一些好印象!經過了3個月的奮戰,才發現自己小看了這個任務的難度與重要程度。
3個月?真的不夸張,我花了3個月的時間,最后只是把標準和實際有什么差別搞清楚了,但是一點都不遺憾,因為這3個月的基本馬步,給了我未來二十多年的制造管理工作中對于工時有了基礎的認知。所以今天就來聊一聊標準工時與實際工時之間一些容易混淆的觀念。
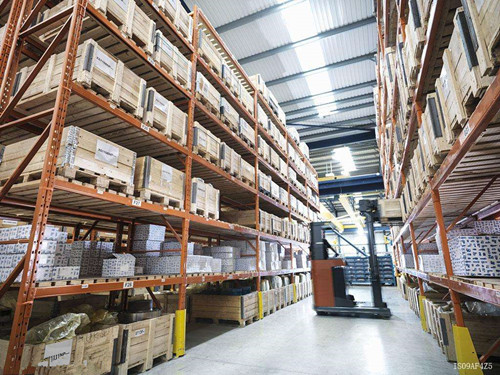
不準怎么可以成為標準?
常常聽到有人說:單位的IE不知道在干什么?標準工時一點都不準!這個是最常被挑戰的問題了!所以先很快的科普一下,什么叫做標準工時?
現代對標準工時最一般定義是:「標準工時乃指對于必要之能力受過充分訓練的作業人員,在適當的速度和作業環境下執行作業所需要的時間。」
所謂標準時間,乃是在下列條件下,完成一單位作業所需的時間:
1.? 采用標準作業方法與設備
2.? 在標準化的作業條件下
3.? 作業者均具備制程所要求的熟練度與適應度
4.? 在不妨害生理健康的情況下
5.? 以企業所認定的正常作業速度,完成一個單位作業量所需的時間
在定義里面完全沒有提到標準就是要“準”,能夠做到一秒不差就叫做好!在標準的設定中本來就有所謂必要的寬放(如生理與疲勞),關鍵是合理認定的“適當”。所以第一件該說清楚的就是設定標準的目的本來就不是要求“準”,但是要求合理,既然目標是合理,就應該是可以有機會達成(作業人員在上述定義的條件下可以做到)。但事實往往不盡如人意,任何一個因子都可能使得實際作業無法達到(當然也可能超出)。而這也就造成了當實際與標準有了差異時,不明白其原理的人會認為標準一點都不準。有一些沒認清管理目的的工程師,受到這個“不準”的壓力,就開始以誤用實際工時的某種平均方式來形成標準,甚至為了要準,還加上很大的寬放值,來達到準的目的。拋棄了原來在標準工時的設定下應該有的“合理”。

一個持續改善的過程
與其說是標準,其實更像是階段性的管理目標。
1. 標準工時的起點:
大家想想你所在的企業,當一個產品生成第一版的標準工時是在什么時候?較規范企業應該是在開發的PVT(量產能力確認)階段,或是新產品導入(NPI)的階段,當時可能很多的生產作業還在變化就開始設立標準,即使變化還是很多,也一定會先依過去經驗先預估一版或是以實際的生產數據以統計的方式來產生一版,這兩個方式并沒有錯誤,因為在新產品導入階段,關注的重點是:如何讓產線可以快速的進入量產!
標準工時會隨著作業內容不斷的調整與修正,目的也是希望協助產線能逐步穩定形成合理的作業規范。產品導入量產前,標準工時是隨著制程作業的調整一直改變的,企業管理能力較佳的的體現就是:新產品導入的時間很短(標準工時也會隨之穩定下來)。
2. 標準工時的持續精進:
接下來就是進入量產階段,此時的管理關注是:如何確保交貨能夠有效的達成,也開始進入效率與成本的檢討。
既然新產品導入量產了,合理的標準已經建立,工時管理的重點:不是消滅差異而是管理差異。為何實際作業有差異的發生?這些差異如何被有效的分析(管理),此時各種改善手法與工具才上場。
找到造成差異的原因(例如:作業手法,治工具,設備參數或穩定等等),這才啟動現場的持續改善活動,確定是標準真的不合理、還是人員訓練不足、設備穩定度不好還是治工具設計不良或是耗損…。
當差異因子被充分掌握了,才知道標準是否有必要變動。(如果標準作業與規范沒有變化,工時為何會變呢?)再提醒說明下:不是消滅差異而是管理差異。
永遠要記得總結
當歷經新產品導入的快速調整,以及后續不斷檢討分析差異,進行了許多的改善,個別產品完成量產的使命了,很多企業在工時管理的過程,忽略了最后一個環節,那就是歷程的檢討!
因為企業的許多產品都有系列關系,或是基于類似的制程工藝生產,所以經過這樣的改善經驗后,下一個接續產品的開發,不就有了一個相當好的對標基礎?而且是全周期的參考,除了在個別作業的工時,還可以作為產品爬坡提量的參考,也就是應該會對后續產品提供最佳實證的歷程參考。但是目前大部份的企業都忽略了將工時的過程作完整的紀錄(改善履歷),而這個履歷正是提供新產品設計的可量產性(Design for Manufacture, Design for Cost…)重要的指導。
標準工時的管理是伴隨產品生命周期的管理,同時產品的BOM以及損耗也有類似的特性,所以同樣也可以應用在標準成本的管理上,目前也已經有成熟的信息系統可以協助企業進行工時的管理與后續的應用。所以,千萬不要忽略了這看似基礎而且又繁雜的工作,對于制造管理來說,是至關重要的一個能力。
文章來自網絡,版權歸作者所有,如有侵權請聯系刪除