2008年在一次偶然的機會,我看到《目標》這本書,直到2011年經過幾次精益實踐的挫折后,才真正開始采用TOC。
2007年之前,我從事市場和銷售的工作,為了自我挑戰,“轉型”進入生產管理領域,適逢精益生產方式如火如荼,就開始在公司內部主導與推動精益。公司屬于服裝行業,是典型的勞動密集產業,對人力的依賴很強,一直還不能做到“自動化”生產。所以,當時面對的最大問題是“人員管理”!
即使再好的方法、再先進的設備,都需要“人”來執行、操作。由于從業人員的不同技能、知識及文化背景等,出現人員不穩定且流動率非常高的狀況,以致于對生產系統影響非常大,難以維持穩定的生產效果。
那時,工廠開始實施示范生產線,由于有多余“資源”(人、機、料等)的保障,效果相當不錯。比如,成品能很快下線(相較于之前至少需要3天成品才會下線)。如果出現品質問題,很快就被發現并解決,生產線人員配合緊湊,很少出現一會兒這個去廁所,一會兒那個去喝水等散漫的情形。
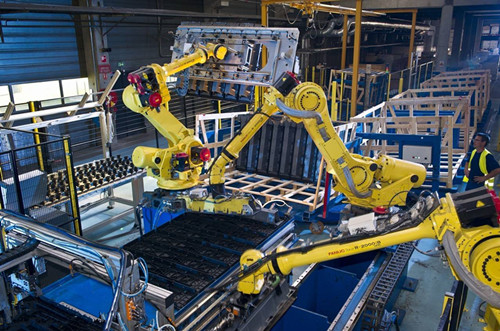
但是,后來全面推廣“單件流”時,諸多問題逐步暴露出來。例如,因為人員流失、設備故障、物料缺失,或半成品品質問題等,經常造成生產線停滯,整個車間的問題層出不窮!剛開始的時候,老板還有耐心,后來問題越來越多,管理人員也經常抱怨,老板就堅持不下去了,“東風重新壓倒了西風”,大家又回到了初始的狀態。這個時候,雖然之前發生的問題依然不斷,如交期延遲、批量的品質不良和返修、設備故障后保全人員的“不緊不慢”等等,但大家似乎比較適應原來的狀態!
由于老板停止了改善項目,我感到非常失落。但是,我堅信改善的方向沒有錯,可能是公司本身的諸多問題造成了這次的不成功(外責于人)。在“英雄無用武之地”下,我離開,去了一家專門做精益生產的公司。但在接下來的諸多企業精益改善項目中(主要是服裝行業),最終的結果大同小異。
這時,我漸漸感到“挫折”,開始反思“精益生產”!我們的團隊在項目實施過程中,都很努力,初期的示范生產線,也都取得了不錯的效果,為什么在全面推廣過程中問題逐漸暴露,我們和企業都“無暇顧及”,最后,都不得不回到原來的狀態?好幾個月的辛苦付出(勞民傷財),最后都是“曇花最初的一現”?
迷茫中,我突然想到了《目標》那本書,高德拉特博士稱之為“簡單有效的管理常識”的TOC!的確,《目標》中提及的都是普通的管理常識,它能解決我們遇到的諸多管理難題嗎?再次讀完整本書,感覺確實“簡單”啊!找到系統的“瓶頸(約束)”,用聚焦五步驟(F5)的基本原理,結合DBR(DrumBufferRope,鼓緩沖繩)的管理方法,管理好系統的“瓶頸(約束)”!帶著疑惑和懷疑,我決定嘗試一下。
這時候,正好有一個做展柜(服裝門店的道具)的朋友,因為訂單的交期問題,答應客戶一個月的生產周期,等到客戶的店面裝修完畢,商場都要開業了,工廠這邊,還有幾個展柜沒有生產呢!運到客戶店鋪的展柜,經常缺這個,少那個,運過去,也無法組裝。客戶每天都在投訴,他每天都在焦慮中(當老板不容易?。?。每天看到他在接電話,不是被客戶罵,就是他在罵員工。
有一次,我們喝茶聊天,我試著用TOC的理念,給他講解了一下,他聽著有道理,讓我幫他搞搞(有種“死馬就當活馬醫”的感覺)。但服裝行業摸爬滾打了這么多年,我還有點經驗,家具行業我不懂啊,“隔行如隔山”!還是朋友想得開,他鼓勵我,說服裝行業和家具行業,本質上差不多。服裝的原材料是“面料”,家具的原材料是“木料”;服裝是把面料裁剪、切割不同的大小裁片,通過“縫線”,組合成一件衣服;家具是把木料鋸成不同的規格、尺寸,通過螺絲、釘子等,組合成一套家具。加工路徑雖然不同,本質還是一樣的(其實,這類企業是TOC企業類型中的“A”型企業,朋友當時就能通過現象看本質,不簡單)。我想想,也是啊,試試就試試!
通過現場調研、流程分析,最終確認朋友家具廠的瓶頸是“烤漆”工序(F1:辨識系統的制約)。如何挖盡瓶頸工序(F2:決定如何充分利用系統的制約)?由于不同配方和顏色的漆,需要烤漆房的溫度和時間是不同的,如溫度低,時間長,或溫度高,時間短。還有烤漆房的特性是,升溫快(低溫到高溫),降溫慢(高溫到低溫)。由于前段裁料會按批量鋸割,烤漆房也會按批量加工,造成后端組裝的物料短缺(不“齊套”),等待時間很長。所以,決定應用DBR管理方法,以“齊套”為原則,及按烤漆房的產能最優化排產。就是說,原材料倉庫的出庫和第一個工序的投料,都嚴格按照“齊套”的要求下料并且根據烤漆房溫度由低到高的變化順序排程,使瓶頸資源的OEE最大化(F3:其他一切非系統制約的事物皆全力配合上述的決定)。
上述實施的過程非??欤蠹s一周的時間,朋友也非常重視,親自抓。基本上,我是參照書上說的“照貓畫虎”,他是認真執行。一個月過后,改善的效果出來了,一套展柜從投產到全部出貨15天的時間,組裝齊套率從30%提升到75%(初期的一些問題,確實考慮不周全)。后來,進一步完善流程(中間,也借鑒了很多精益的方法,如Layout、SMED等),生產的前置時間(LeadTime)是3天,從下訂單到在工廠的試裝完成7天時間,現場組裝齊套率提升到100%。朋友很高興,邀我入伙,但我知道,這次可能是比較幸運而已。對于TOC的認識,我缺少的還是很多!我拒絕了朋友的好意,但還是收了他一些咨詢費用,咱也是“生意人”。
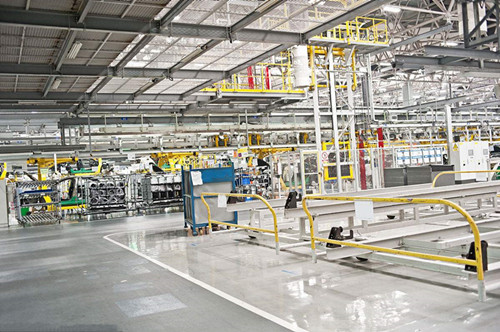
后來,我把取得經驗在幾個傳統行業,如服裝、機械制造等,也嘗試過TOC的改善實施,都在短期內取得了很好的滿意效果??偨Y自己生產改善的實踐經歷,分享一下對于精益生產(Lean Production,LP)和約束理論(Theory of Constraints,TOC)兩大管理理念的感悟。
我認為精益生產和約束理論,都是迄今非常偉大的管理思想!LP來源“豐田式生產方式(Toyota Production System)”,美國借鑒后,成為“精益生產(LeanProduction)”,而Lean的英文本義,是“瘦的、苗條的、少肉的”意思,中文翻譯后,意譯為“精益”,也是非常貼切。企業如何做到“精益”(減肥)?豐田的做法是經過持續的“改善”,減少生產過程中的“浪費”,平衡產能,實現“準時化(JIT)”和“自働化”。在這個過程中,需要長時間的人才培養(“造車之前先造人”),以全員質量管理(TQM)和全員設備管理(TPM)為基礎,打造人員層面、設備層面、供應層面等的穩定性,實現“標準化”作業,使整個系統達到穩定的輸出。所以LP的實施,對系統(人、機、料、法、環等)穩定性的要求非常高。
然而,大多數企業往往不具備“系統穩定性”這樣一個前提條件(關鍵是很多企業沒有太多的耐心做好前面的基礎工作),“墨菲”每時每刻都在沖擊著脆弱的系統,在這樣的條件下,我們怎樣才能快速實現企業的發展“目標”?TOC給了我們一個簡單易行的“管理常識”---聚焦于系統的“瓶頸(約束)”環節,用F5(聚焦五步驟),一步一步穩定實施,能盡快見到效果!做個有趣的比喻,如果兩種管理方式的“目標”都是“減肥”,精益要求打好基礎,持續不斷的“健身鍛煉”。而TOC通過改善飲食數量(控制投料)和飲食結構(優先順序),就能達到快速“減肥”的目標。當然,TOC也沒有忽略“健身鍛煉”的重要性!(關于精益與TOC的經典論述,請參看高德拉特博士的文章《站在巨人的肩膀上》)
TOC是一門博大精深的管理哲學,不僅應用在生產領域,也不僅有DBR等管理技術。針對不同的產業特性,必須發展特定的決定性競爭優勢,故而TOC的應用相當廣泛,管理手法非常豐富,在此不再贅述。
文章來自網絡,版權歸作者所有,如有侵權請聯系刪除