我曾經(jīng)在印度推廣精益。計劃提出后,首先反對的是工會,工會為什么會強烈的反對呢?其中的一個小細節(jié)是,我們要求工人從坐著工作變成站著工作。工會認為這提高了工人的工作強度,堅決反對。這讓印度公司的董事長非??鄲?。
轉變觀念是最重要的辦法。我對他們說:“改善不是提高強度,而是提高效率?!碧岣咝适裁锤拍??某種意義上講就是降低強度,做同樣的工作,人變得更輕松了。
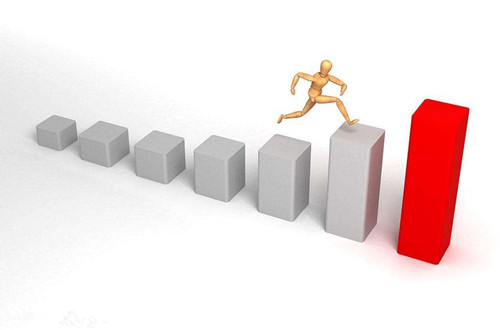
這個概念被印度工人接受和理解了。緊接著,我們宣布一旦提高20%的工作效率,工人加1%工資,工會也因此非常開心。
所以,印度工人的心態(tài)也發(fā)生了巨大的變化:從最初的反對,到后來爭先恐后地要求進入改善項目。對于公司而言,增加1%的工資換來20%的新增營收額,這也是一筆劃算的買賣。
印度工人的另一個特點是,學習速度很快。并且印度工人嚴格遵守改善完的標準,這直接促進了印度工廠的改善推廣速度。
相較之下,在中國的改善推進工作并不那么容易。我曾經(jīng)幫助天津廊坊的一家工廠推進改善。那家公司的廠房根據(jù)TPS布置,從新廠落成的起始,這家工廠就開始了推進改善的進程。但奇怪的是,時間一長這家工廠就會回到老的生產(chǎn)方式上去。其中,現(xiàn)場執(zhí)行人員沒有得到充分的培訓是改善無法持續(xù)的原因。
為了解決這一問題,我只能從外部尋找解決的辦法。比如,工人總喜歡一次做幾十個零件放在一邊,但這并不符合單件流的要求。因此,我們選擇了取消附近放零件的桌子,強制工人一次只能生產(chǎn)一個。另一個問題是,工人喜歡將手頭的工具亂放。于是我們將工具臺設在生產(chǎn)線附近,同時體積小,位置小。工人必須仔細擺放到位,工具才不會掉下來。在后期,我們要求工人將要遵守的流程守則抄寫到本子上,務必保證工人們將內容印到腦子里,而不是敷衍了事。
不少中國工廠在推進精益時,都有類似的問題。第一,沒有系統(tǒng)性,最終不了了之,沒有持續(xù)推進的動力。第二,精益推行的負責人是其他部門經(jīng)理兼任,因此無法帶來積極的部門參與。改善執(zhí)行者如果不投身到實際操作中,就無法帶動團隊來推進改善。第三,在工廠中少有員工有成功精益改善的經(jīng)驗,管理者不知道精益改善能夠做到什么程度,具體有哪些操作方向。第四,成功地精益改善必定從管理高層開始,自上而下地帶動整個公司。但在中國很少有企業(yè)的總經(jīng)理會全部投入到精益改善中,自然中層管理者也不會以此為重點工作。
不止一次,在中國工廠里人們問我,什么是成功的改善?
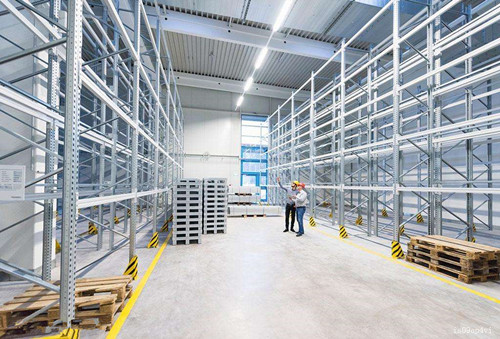
往往人們指出一個改善的成功在于解決了多少,人員效率提高了多少。但這有個前提,改善前期的目標從何而來?這個目標應該是在現(xiàn)場考察商量得來的,應該是根據(jù)生產(chǎn)線的狀況得出的,在專家的評估下,數(shù)據(jù)的整集下,才能最終得出改善的目標。
因此,真正的改善在于意識改善,而非形式改善。公司中要營造改善的熱情,這樣的改善才是一個成功的改善。
文章來自網(wǎng)絡,版權歸作者所有,如有侵權請聯(lián)系刪除