一、與傳統品質管理的區別
不從根本上保證品質,則不可能全面地實施精益生產。當需要一件才生產一件時,如果某道工序出了不良品,則后續工序將沒有輸入,會立即停工。所有上游工序都必須補充生產一件,這樣就完全打亂了生產節拍。要全面實施精益生產,必須消除不良品。
傳統的品質管理的方法是:加工零件或生產產品→檢查→挑出合格品或合格批次→交給用戶。對于能返修的不良品要進行返修,或降級使用;對于不能返修的不良品則報廢。這種方法主要依靠事后把關來保證品質。實際上,因為錯檢或漏檢時有發生,即使經檢查確定的合格批次,也不能保證百分之百合格。且采用抽樣檢查得出的合格批次中通常都包含一定數量的不良品。
與傳統品質管理不同,精益生產之品質管理強調事前預防不合格品的發生,要從操作者、機器、工具、材料和生產過程等方面保證不出現不良品。它強調從根源上保證品質。
精益生產給傳統的品質管理增加了新的特色。它使“必要的工作”這一模糊的概念變得十分清楚,大大提高了品質管理的有效性。“必要的工作”是指那些增加價值的活動。不增加價值的活動是應該消除的,把不增加價值的工作做得再正確不但是不必要的,而且是浪費。
二、品質保證的五要素
在現場,保證品質的5要素是:
人(Man)
材料(Material)
設備(Machine)
方法(Method)
信息(Information)
簡稱為4M1I,對4M1I精益生產的要求見表6-1:
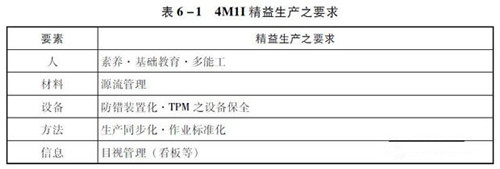
表中五個要素固然都重要,不過,有關設備的防錯裝置化在國內許多企業較少提及,以下重點進行說明。
所謂防錯裝置化,即是讓錯誤不發生或即使發生了也能防止不良品流下去的方法。防錯裝置化對精益生產中是十分重要的。試驗證明,當正確的操作方法比錯誤的操作方法容易做的時候,人們總是選擇正確的操作方法。防錯裝置化的實質就是要使正確的操作容易做,而錯誤的操作難以做或者不能做。例如,設計一種工藝設備,當它安裝得不正確時,它會使機器不能運轉。這就保證工人的安裝錯誤不致影響加工品質。防錯裝置化不僅可用于生產品質控制,而且可用于檢查和產品設計。因此在品質控制中,防錯裝置化與統計過程控制方法同樣重要。這一點國內許多企業管理人員似乎尚沒有足夠的認識。圖6-1、圖6-2、圖6-3、圖6-4、圖6-5說明了防錯裝置化常用的五種手法。圖6-6是防錯裝置化的一個案例。
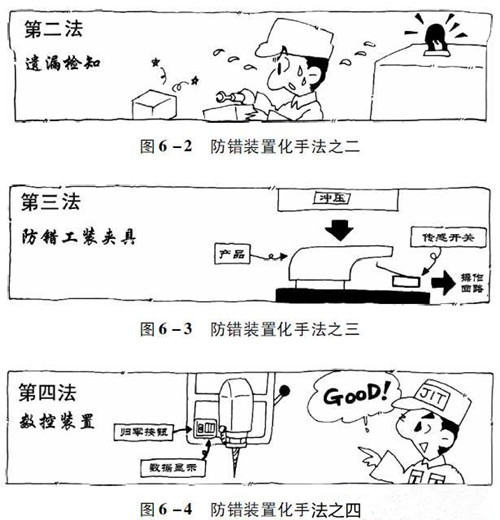
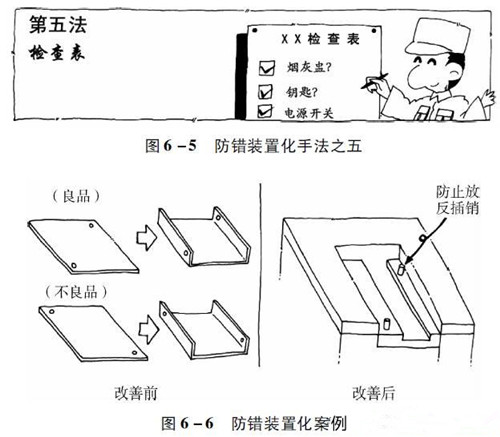
防錯裝置化對錯誤的防止有三種方式,即停止、防備、警報。不良品的狀態分為“即將出現不良”與“已出現不良”兩種。“即將出現不良”稱為“預知”,“已出現不良”稱為“檢知”(檢查后知道之意)。圖6-7為防錯裝置化處置流程圖。
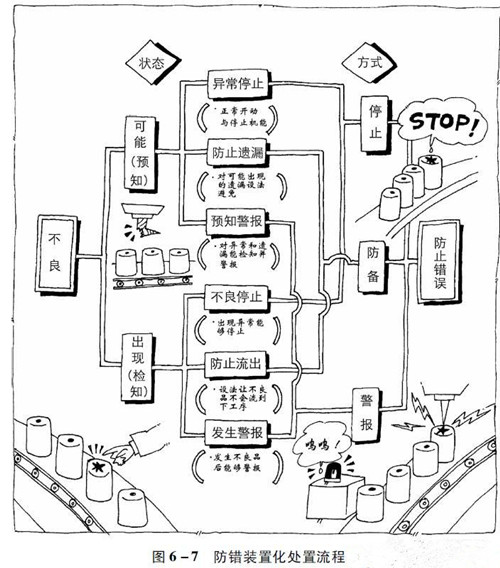
如果能達到圖中之要求,就能實現“讓錯誤不發生或即使發生了也能防止不良品流下去”之目標。
三、從事后把關變成事前預防
使品質管理工作從事后把關變成事前預防,必須使生產過程得到控制,這就需要做好兩件事:一是操作人員的參與,二是要解決問題。操作人員的參與對于工序品質的控制至關重要。工人在操作過程中要收集必要的數據,發現問題,實行自檢。解決問題要采取正確的方式,正確的方式要求采用必要的診斷方法,找出影響品質的根本原因。
是否找出根本原因有一個標準可衡量:該問題是否重復出現。如果沒找到根本原因,不采取措施消除產生該種品質問題的根本原因,則這種品質問題一定會再現。錯誤的方式就是“有病亂投醫”,只求解決品質問題,將能采用的方法都用上,不管真正起作用的是什么辦法。結果,問題還可能出現。即使問題不再出現,也不知是什么辦法使之不再現。
一旦生產過程處于控制狀態,就要維持這種控制狀態,才能保證品質。維持控制狀態可以采用三種方法:操作者更多的參與、統計過程控制、防錯裝置化。
要使操作人員參加維持控制狀態的活動,首先要使他們了解后面工序的要求。其次要有反饋機制,通過控制圖使工人了解工序是否處于控制狀態。第三要使工人懂得如何采取行動,糾正所出現的偏差。

統計過程控制基本上是一種反饋控制機制,即通過過去的信息去控制將來的操作。僅僅有反饋控制對精益生產是不夠的,應該采取事前控制,即當缺陷出現之前就采取行動,防止缺陷出現。統計過程控制方法一般適用于可以定量的場合,如長度、直徑、重量、數量等。但生產控制中有更多的因素是非定量的,比如機器運轉的聲音、環境的污染、不正確的設備調整和誤操作等,是不能用統計方法進行控制的,這些就需要防錯裝置化。
文章來自網絡,版權歸作者所有,如有侵權請聯系刪除