精益是借助有效實施載體進行持續改善活動。在進行改善前,我們需要對現狀進行分析,以客戶需求為出發點,以價值流分析(Value stream analysis)為手段,識別整個訂單執行流程中所有不增值(NVA)的活動并加以消除,從而有效降低在制品庫存提升生產效率,改善產品質量和設備,提高最大效益。它的目標是追求七大浪費的不斷消除,追求盡善盡美的境界。
企業推進精益生產首先需要普及精益生產理念和精益生產方式,使管理層及員工認可和接受。與此同時在持續改善推進的過程中,公司需要進行大量的、持續的投入,特別是需要建立推進改善的團隊,團隊成員既要有一定現場工作的工作經驗,更要有充足的時間很多細部的工作,以期取得的成果并獲得更高的效益。
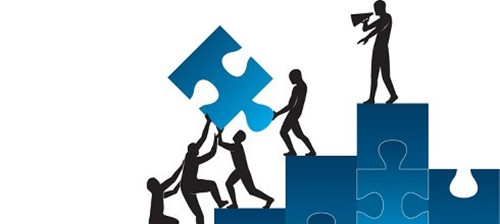
推進精益改善時,需要結合公司的實際情況,集中于對已實現精益轉變的生產線進行持續改善,并以量化評估的手段,確定后續改善的方向和項目改善。改善的著眼點是消除浪費——按照消除七大浪費的思維方法,不斷識別和持續減少生產運作環節中存在的浪費,直至完美。
根據公司期望與項目的特點、難度和范圍,往往通過三種形式實施持續改善:
1. Focus-Kaizen? --針對整體轉型規劃的設計,就較難的改善項目,由專業顧問進行指導,公司成立專項的組織,建立全職推進團隊和現場實施團隊,實施全面的專項改善活動,通常以10-15人3到6個月為宜(包括改善前設計、改善實施、改善后標準化和穩定化)。
2. QCC-Kaizen –根據項目的特點和范圍有選擇的組織相關部門的人員進行局部的改善活動,一般以5-8人為宜,可以根據具體情況突擊完成項目或分段完成,這類改善以品質或設備問題解決主題居多。
3. Cultural Kaizen—主要是為了提升公司的改善氛圍,拉動全員參與,通過一系列的活動,對一些任務難度較小、幾乎不用投資、實施周建較短的項目進行開展,往往與改善提案相聯系,如通用汽車內部的啄木鳥活動、大野耐一環浪費識別活動。
不同類型的改善也是著力于剔除現場的七大浪費,從而達到改善成本(C)、品質(Q)、周期(D)、安全(S)的目的。精益生產是一種持續改善的方法和思想,它提供了改善需要的相關工具和方法,同時,精益生產又是IE的綜合應用,精益生產的改善需要充分利用IE有關現場控制及改善的工具和方法。我們用量化的測量方法評估改善的效果,對一些不能量化的改善,應該用定性的評估方法,比如:員工士氣提高、目視果改善、工作規范化等。并以組織改善分享會的形式,對團隊進行表彰總結和鼓勵。

評估效果時,主要從下幾方面來評估:
1. 效率:定量——評估人員或設備的效率。
??? 人員:人均小時產出/人員減少/單件工時降低
??? 設備:可動率/停機時間/停機次數/OEE/切換時間等
2. 品質:定量——產品的一次通過率和不良率
3. 空間:定量——基于一定產量或人員所需的空間
4. 周期:定量——生產線上在制品的數量
5. 士氣:定性——員工對生產線的參與和滿意程度,
??? 定量——員工改善建議的數量與滿意度,星級班組
6. 系統:定性——工作流程的標準化、系統化和規范化。
? ? ? ? ? ? ? 定量——標準化流程文件數量
7. 5S:定性——現場的目視效果、人員安全
? ? ? ? ? ?定量——5S評分(金銀銅牌認證)
文章來自網絡,版權歸作者所有,如有侵權請聯系刪除