下面筆者就來介紹一下跨越“單人式單元生產”的第二個障礙——質量確保的方法。筆者對設計的基本看法是“產品生產的95%由設計(產品設計及工序設計)決定”。也就是說,要想彌補人類集中力和注意力不好的弱點,跨越建立質量管理體制這個障礙,就必須在設計上下功夫。
因此,首先要轉變思路,由“不制造次品”轉變成“制造不出次品”。這相當于防止交通事故中的主動安全。也就是說,要想確保質量,關鍵是構建“制造不出次品的設計體制”。
其方法有很多,而現在的主流方法是三維CAD、田口方法(質量工程學)、公差分析、FMEA(失效模式與影響分析)及這些方法的組合。筆者采用的三維CAD接合FMEA的方法。
筆者把從設計部門拿到的三維CAD數據作為數字樣品,徹底評估有可能出現組裝失誤的部分。比如,檢查零件有沒有正反面,忘記擰螺釘時能否檢查出來等要點。也就是從生產現場的視點出發,對零件和工序逐一進行評估。
FMEA通常采用1~3分或1~5分的評分等級,而筆者采用的是0~2分的三級評分。基于FMEA的檢驗單如圖3所示,筆者簡化評分等級是為了加快評估速度。因為筆者在羅蘭公司工作時負責的產品是大型噴墨打印機,必須評估幾千個零件。
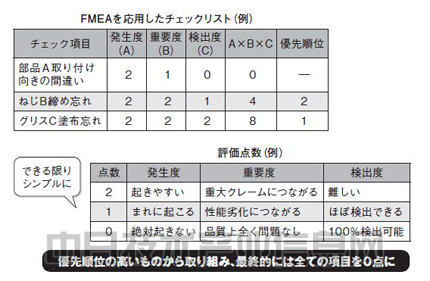
圖3:利用FMEA方法制作的檢查單
彌補人類集中力和注意力不好問題的體制之一。為了能在設計和設備兩方面“防錯”而進行檢查。對最好的情況給“0”分,更容易表示極端狀態。
之所以采用“0”分,是因為筆者覺得“發生度”、“重要度”、“檢出度”這三個檢查項目都最好為“0”。也就是說,目標是發生度×重要度×檢出度=0。最好是發生度為0,也就是說絕對不會出現質量問題。重要度為0,就意味著可以去掉這些零件和工序。最后一道防線是,一定能檢查出問題(沒有漏檢),即檢出度為0。
然后就是把生產部門按照上述方法進行的質量評估的結果反饋給設計部門,不過此時有件事情應該注意,那就是拿出備用方案。如果只是對忙碌的設計負責人說“這里會出問題,想想怎么解決”,設計部門和生產部門的關系就會出現隔閡。而如果這樣說,“我覺得這部分如果這樣調整一下設計,發生度就會變成0。我已經按照生產部門的情況修改了零件的數據,請您確認一下。這樣還能削減成本”,設計者就更容易接受。
徹底的防錯設計要一直持續到試制階段,這是應該凝聚工程師智能的地方。這樣,設計部門和生產部門齊心協力,還有利于形成能在短時間內開發出優秀新產品的競爭力。
工序中的防錯機制
如果鑒于技術原因和成本原因,在設計中無法引入防錯機制,那么就需要在工序中引入防錯機制。下面舉一個使用高度尺確認高度工序中的例子。
高度尺分模擬讀數和數字顯示兩種,使用模擬讀數型高度尺時存在視差,本來刻度的讀取方法就不好掌握,而使用數字顯示型高度尺就很少出現讀錯數字的情況。
于是,筆者在該工序中導入了組合使用可將測量值無線傳輸到PC的數字式高度尺和接觸式探頭、對測量值和PC上設定的閾值進行比較的方式。這樣就能減輕工作負擔,工人無需讀取測量值,如果PC上顯示藍色的“OK”則進入下一工序,而如果顯示紅色的“NG”則重新調整。這樣一來,工人不需要刻意做檢查,而是在工序中自然進行檢查。
本來最終檢查就是為了分出合格品和次品。流水線生產會在最后工序設置最終檢查,但如果到這個階段才發現次品,損失將不可估量。而且,有時還會影響到負責問題工序的工人與終檢負責人之間的人際關系。因為,無論是誰,被別人指出自己的錯誤都會不舒服。
而單人式單元生產不設檢查人員。由工人自己“在適當的時候,用適當的方法,檢查適當的特性”。這被稱作“自我完成型單工序保證”,如果不合格就不進入下一個工序。采用的是引入了防錯機制的“不依賴人,而在工序內打造質量”的做法。如果徹底貫徹這一機制,即使是擁有幾千個工序的組裝,也可以很自信地說,“進入最后工序的產品全是合格產品”。
由于工人通過自我檢查親自找出自己的工作失誤,因此不會因為“被別人找出錯誤”而感到不舒服。他們反而會想,“呀,這次失敗了,下次絕對不再失敗了”,會產生上進心。這也是單人式單元生產能夠營造“輕松愉快的工作氛圍”的原因之一。
共享檢查設備
下面就來介紹跨越第三個障礙——設備成本、也就是實現沒有浪費的設備投資的方法。就拿前面提到的帶有無線數據發送功能的高度尺和接觸式探頭來說,這樣一套裝置并不便宜。如果每人一套,投資額就會增加,不僅很難實現,而且還會形成巨大的浪費。
解決這個問題的好辦法就是在組裝單元群中設置一定數量的檢查單元(圖4)。在羅蘭,這叫做“Special Shop”(特殊工作臺)。工人在自己的組裝單元中工作,快到要使用檢查設備的工序時,組裝單元上設置的顯示器上就會顯示“請到特殊工作臺”。這時,工人和帶腳輪的工作臺上放置的產品一起移動到特殊工作臺進行檢查,如果顯示OK,就再返回自己的組裝單元。

圖4:利用單人式單元生產打造質量
不僅是產品組裝,單人式單元生產在檢查的時間、特性及方法方面都很恰當,還能迅速反饋到設計上。其中,數字測量發揮了很大的作用。
有時需要排隊等待,不過基本不會出現所有工人一起涌到特殊工作臺的情況。如果經常出現3、4人排隊等待的情況,工人肯定會提出要求。這時,可以考慮增設特殊工作臺。
根據每件產品的平均組裝工時和使用該設備的檢查工序的時間比例,可以計算出幾個工人共享1臺設備比較好。能夠準確測量這些時間(POP=生產時點)也是“數字單元生產”的一大優勢,詳細內容將在后面介紹。
生產手冊的數字化之路
筆者在前面已經介紹了彌補人類弱點——集中力和注意力的方法,但還沒介紹彌補記憶力的方法。雖然我們都知道人的記憶力是有限的,但還是想讓所有工人都能獨立完成有幾千個零件、需要幾十個小時的大規模組裝。這樣怎樣實現呢?
我記得羅蘭公司開始考慮由流水線生產轉為單元生產是在1996年。筆者當時是生產部門的小組長,還處在年輕氣盛的年紀。當時,筆者反對單元生產,還曾跟生產部長爭辯說“這根本不行”。沒想到將來會成為單元生產的專家。
當時生產部長說,“不管行不行,先試試看”,筆者只要答應說,“好吧,我研究一下”。結果一研究才發現“這或許可行”。于是筆者決定讓一名老工人看著有500頁A3紙的生產指南,組裝當時最復雜的產品。結果,他一個人就完成了。
不過,因為是有經驗的老工人,所以才做得到。怎樣才能讓當時近50名工人全都做到呢?正當筆者為此苦惱的時候,用三維CAD制成的一目了然的設計圖出現在眼前。
當時,中端三維CAD已開始普及,在經營會議上負責開發的董事說:“以后將在設計中采用三維CAD,但是,僅設計部門使用三維CAD沒有意義。所有部門如何使用三維CAD將關系到今后公司的命運,以后的主題將是‘數字工廠’。”筆者聽到這番話的瞬間,腦海中浮現出了“直接使用三維CAD數據的既美觀又好用的數字指南”,筆者覺得,如果使用數字指南,任何工人都能夠進行單人式單元生產。
文章來自網絡,版權歸作者所有,如有侵權請聯系刪除