單件流生產方式是按產品別布置的多制程生產方式,產品在生產過程中實現單件流動,它是準時化生產的核心,是解決在制品的秘方,是消除浪費的最好方法。
單件流生產方式主要優點:
1.生產周期短:單件流生產方式采取分工原則,要求各工序不是批量生產后再流轉下工位,而是生產一件(是否一件是最高效最經濟需結合具體行業,以設定標準)就要流轉下工位,并要求各工位按統一節拍生產,以實現生產過程順暢,在制品不積壓,快速得到成品,根據節拍和生產工時就可得知完成產量所需總周期,根據目標差異就可靈活應對,保障交貨及時。
2.在制品少:單件流生產方式是連續流動生產,突出特點是在制品得以極大的壓縮。
3.場地占用少:單件流生產方式極大的削減了在制品,減少在制品場地占用,工廠空間得以解放。
4.靈活性大:單件流生產方式,企業在制品總量極少,原材料的投入短周期內就轉化為成品,對于客戶需求變化的應對能力均大大提高,對于不同產品品種轉換時間能大幅削減。
5.避免批量缺陷:單件流生產方式能快速出成品,各工位生產是有序銜接按節拍生產,通過本工序的自檢和下工序的互檢及質檢員專檢能及時發現各工序存在的質量問題,及時進行糾正,能有效避免批量質量缺陷。

單件流生產方式建立步驟:
步驟1 全員的意識建立:觀念上必須改變,堅持以一個流生產方式作業,尤其是干部。
步驟2 成立示范改善小組:不同部門的中堅干部成立示范改善小組。
步驟3 選定示范生產線:應從最容易的地方下手作示范。
步驟4 現況調整分析:選定示范線后,應先充分分析產品的生產狀況(如生產流程圖,生產線布置方式,人員的配置,庫存時間及設備稼動率等)。
步驟5 設定T.T時間:以每日的工作時數除以每日市場的需求數----即目標時間。T.T受出勤時間及訂單量的變化而變化,與現場的設備、人員的生產能力是無關的。許多改善的出發點以T.T為依據。
步驟6 決定設備、人員的數量:根據T.T、各作業的加工時間和人力時間,計算出設備需求數和作業人員的需求數,設備不足,應分析稼動率,進一步改善以提高設備產能;而人員不足,則必須努力設法將零點幾個人的工作量予以改善并消除掉。
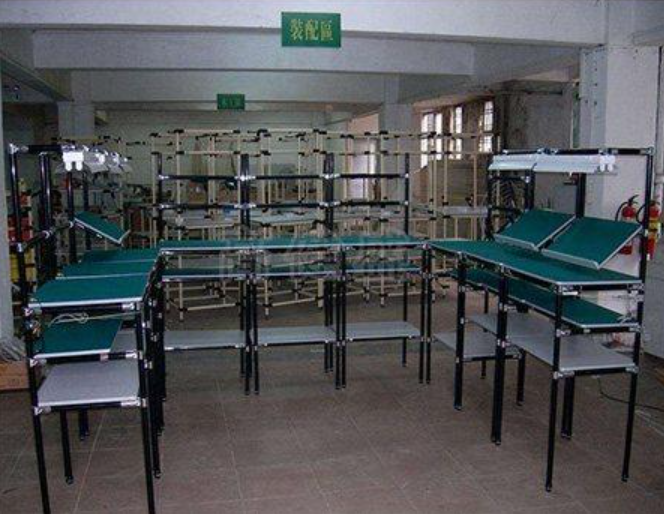
步驟7 布置一個流的生產線:根據作業加工順序,以逆時針流動,設備盡量拉攏以減少人員走動及物品搬運的距離,設備小型化、滑輪化、專用化。
步驟8 配置作業人員:以“T.T”為目標,將各作業內容分配到每一個作業員,使得每一位作業員所分配到的作業時間的總和能無限接近“T.T”甚至完全一致。作業員必須要是多能工,才能有效充分的利用人力時間。
步驟9 維持管理與持續改善
步驟10 水平展開與少人化目標
本文為冠卓咨詢原創文字作品,任何人或組織不得對本文進行篡改,轉載或以盈利為目的行為,一經發現,將負法律責任。