MTS 即Make to Stock, 它是針對庫存生產(chǎn)的生產(chǎn)類型;;企業(yè)根據(jù)以往一段時間的銷售情況,制定相應的生產(chǎn)版計劃權,先生產(chǎn)出產(chǎn)品,然后再銷售的模式,現(xiàn)代社會供大于求,所以,該生產(chǎn)方式存在很大的風險,在精益生產(chǎn)中,這種方法很不可取,除非企業(yè)生產(chǎn)的產(chǎn)品在市場上占壟斷地位或者市場上對該產(chǎn)品求大于供;按庫存計劃(MTS)計劃是制造工廠用來匹配未來/預期的消費者需求庫存的一種常用生產(chǎn)策略。這與其他生產(chǎn)方法不同,其他生產(chǎn)方法通常包括生產(chǎn)指定數(shù)量的商品,然后通過嘗試銷售商品來合并銷售。按庫存生產(chǎn)(MTS)估計其產(chǎn)品可以產(chǎn)生多少訂單,然后簡單地提供足夠的庫存以充分滿足這些訂單。
使用按庫存制造(MTS)的方法需要準確預測需求,以正確確定必須生產(chǎn)的產(chǎn)品數(shù)量。如果可以準確估算您的需求,則MTS策略可能對您來說是一個有利的選擇。按庫存生產(chǎn)(MTS)可以輕松降低庫存成本,增加利潤并以更有效的方式幫助您利用材料。話雖如此,生產(chǎn)策略也有一些缺點。
存貨計劃(MTS)的缺點
從理論上說,按庫存計劃(MTS)計劃方法與公司如何為變化的需求做好準備有關。正如我們希望能夠在幾秒鐘內(nèi)為客戶完成訂單一樣,生產(chǎn)根本就行不通。通過基于歷史數(shù)據(jù)和當前需求生成的未來需求預測來獲得庫存數(shù)量和產(chǎn)量。如果預測發(fā)現(xiàn)自己甚至一點點偏離,制造工廠的庫存可能會過多或過少。到目前為止,這些錯誤是使用按庫存生產(chǎn)(MTS)計劃方法的主要缺點。與需求預測有關的任何形式的不正確信息都可能導致過多的庫存,缺貨或更糟的收入損失。
MTS的整體有效性完全和完全取決于其能夠預測未來消費者需求的能力。這種不可靠性對于制造操作而言可能是極其昂貴的。盡管這是最嚴重的缺點之一,但是如果您的生產(chǎn)設備年復一年的需求穩(wěn)定,那么MTS對您來說可能是一個有益的選擇。
按庫存生產(chǎn)(MTS)計劃示例

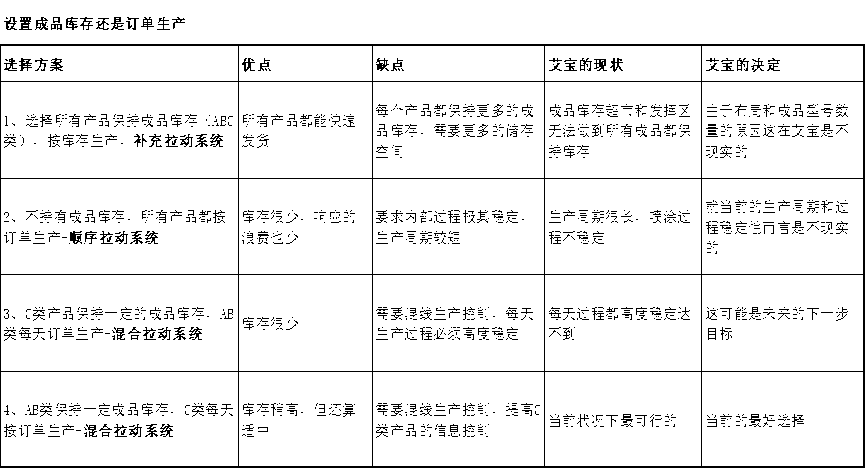
以下是一些最受歡迎的按庫存生產(chǎn)(MTS)的示例:
快速消費品 -按庫存生產(chǎn)(MTS)的主要好處和目標是效率。這樣的一個例子是快速消費品,其中制造設施可以大批量生產(chǎn)物品,從而實現(xiàn)規(guī)模經(jīng)濟和單位成本低廉。
時尚 -再一次,按庫存生產(chǎn)(MTS)依靠可靠的需求預測。時裝公司可能會要求對特定的鞋子設計進行需求預測,該預測會根據(jù)尺寸,顏色和款式變化等因素進行細分。如果預測結果不正確,那么顏色或尺寸最終都將供不應求,甚至如果沒人最終想要這種產(chǎn)品,甚至會浪費掉。
食品 -食品是目前最具挑戰(zhàn)性的庫存之一。由于到期日期是一個因素,因此要準備好及時購買它是很重要的。例如,雜貨店鏈可以根據(jù)諸如假期,氣候,天氣等任何因素來計劃新鮮水果分類的生產(chǎn)。您還可能會看到,當它們的到期日期臨近或某個特定的假期過去時,這些商品會大打折扣。
原始設備制造商 -原始設備制造商是為其他公司的產(chǎn)品生產(chǎn)零件的公司。在很多情況下,此類零件是按庫存生產(chǎn)的,然后出口到服務于不同地區(qū)的倉庫,這最終減少了周轉時間。
某化工業(yè)MTS庫存控制模型及標準定義:
針對備貨式生產(chǎn)及訂單式包裝兩大供應鏈策略的產(chǎn)品種類,某化工公司均需要對其建立成品庫存。為確保庫存量的合理設置,既滿足客戶交付,又不產(chǎn)生庫存過量存儲,因此需要為成品建立庫存控制模型。具體如下:

如上圖所示,對適用于備貨式生產(chǎn)及訂單式包裝兩大供應鏈策略的產(chǎn)成品設置最大庫存與安全庫存兩大標準,客戶產(chǎn)生訂單時直接從成品庫存中取貨,企業(yè)隨時關注成品庫存的消耗情況,當成品庫存水位消耗到安全庫存時即安排生產(chǎn),并當庫存水位達到最大庫存時停止生產(chǎn)。安全庫存與最大庫存的計算公式如下:
安全庫存:SS=安全系數(shù)×日需求量標準差×√(制造周期),是為防止生產(chǎn)需求或采購交付出現(xiàn)異現(xiàn)波動而導致的供應不及時的庫存量;
最小庫存:MIN=安全庫存+日均需求量×制造周期,是為防止生產(chǎn)部門斷貨而設置的必須要進行庫存補充的庫存量;
最大庫存:“MAX=安全庫存+日均需求量×(制造周期+循環(huán)周期)”或“MAX=安全庫存+一次加工批量”(兩者取最大值),是為防止過量生產(chǎn)從而導致庫存浪費而設置的庫存量。
計算因子定義
安全庫存與最大庫存標準的數(shù)值計算包含了安全系數(shù)、日均需求量、日需求量標準差、制造周期、一次加工批量等因子,各項因子的具體定義如下:
安全系數(shù):根據(jù)正態(tài)分布原理,為確保一定的顧客服務水平(即及時向顧客供貨的概率)而設置的庫存調(diào)節(jié)系數(shù),顧客服務水平與安全系數(shù)設置的對應關系如下表:
表3 顧客服務水平與安全系數(shù)設置對應表
及時供貨概率 | 安全系數(shù) | 及時供貨概率 | 安全系數(shù) |
100.00% | 3.09 | 96.00% | 1.75 |
99.99% | 3.08 | 95.00% | 1.65 |
99.87% | 3.00 | 90.00% | 1.29 |
99.00% | 2.33 | 85.00% | 1.04 |
98.00% | 2.05 | 80.00% | 0.84 |
97.00% | 1.88 | 75.00% | 0.68 |
日均需求量:某一產(chǎn)品種類在過去半年的平均日需求量,用以明確產(chǎn)品需求量的整體高低水平,具體計算公式如下:
日均需求量=過去半年總需求量÷過去半年的工作日天數(shù)
日需求量標準差:某一產(chǎn)品種類在過去半年的標準差,用以明確產(chǎn)品需求量的整體波動水平,具體計算公式如下:
日需求量標準差=√∑(每日需求量-日均需求量)2÷過去半年的工作日天數(shù)
制造周期:指一個反應釜的材料從投料到產(chǎn)出之間的平均時間間隔;
循環(huán)周期:指車間供營運的整體訂單循環(huán)計劃,該訂單生產(chǎn)結束后到下一個循環(huán)開始生產(chǎn)小批量完成的時間截止;
一次加工批量:指產(chǎn)品一次性連續(xù)生產(chǎn)的最小經(jīng)濟批量,往往由產(chǎn)品切換時間、一次合格率等因素決定。
庫存標準更新
某化工公司適用于備貨式生產(chǎn)及訂單式包裝兩大供應鏈策略的成品最大庫存標準與安全庫存標準。物流部崗應會同營銷中心市場部崗、生產(chǎn)部崗位等,根據(jù)市場需求及生產(chǎn)能力的變化,每半年對成品最大庫存標準與安全庫存標準計算公式中的各項因子進行定期更新。
庫存控制流程案例
庫存信息查詢
物流部崗負責在每日下達計劃前將前一天成品庫存日報表導入到《公司成品庫存每日監(jiān)控表》中,由Excel自動運算并生成每一種產(chǎn)品種類“庫存過高”、“庫存過低”或“正常”的狀態(tài)提醒。運算完成后,物流部崗應在第一時間將《成品庫存每日監(jiān)控表》發(fā)送給生產(chǎn)部崗。
生產(chǎn)指令下達:在接到《成品庫存每日監(jiān)控表》后,生產(chǎn)部崗應首先篩選出報表中顯示“庫存過低”的產(chǎn)品種類,按照“最大庫存標準-當前實際庫存量+當日預估發(fā)貨量+產(chǎn)品制造周期內(nèi)預估發(fā)貨量”的任務量計算公式將其安排在第二天的生產(chǎn)計劃中。
停產(chǎn)指令下達:除此之外,生產(chǎn)部崗還應篩選出報表中顯示“庫存過高”的產(chǎn)品種類,通知相應車間立即停止生產(chǎn),直至庫存量消耗到安全庫存以下(即《成品庫存每日監(jiān)控表》中顯示“庫存過低”時)方安排生產(chǎn)。
本文為冠卓咨詢原創(chuàng)文字作品,任何人或組織不得對本文進行篡改,轉載或以盈利為目的行為,一經(jīng)發(fā)現(xiàn),將負法律責任。