任何企業都是獨一無二的。想要實施精益的企業在設計運營系統時都必須考慮自身的特殊情況:需求、資產、目標等等。復制其他組織的運營系統,或遵循某種樣板或指南,都既不可行也不理想。不過,我們還是根據精益運營系統的特色,歸納出了七大要點。
到此為止,我們在談到價值流時,都是假定價值流已經存在。事實上,流程可能相當雜亂且不連續,使得價值流的概念失去意義。因此,精益運營系統的第一個原則,就是必須以類似產品組合起來形成的價值流為基礎。
產品的確切組合方式需視各個企業的實際狀況而定,但標準應該包括需求模式、產品特色以及工藝路線。許多時候,利用產品和工藝來分類,就能比較容易地界定出價值流。比如一家減震器的制造商有兩個價值流,其劃分依據是流程下半部分需要不同設備提供的兩種不同技術。
在其他情況下,用產品劃分較不是那么清楚。比如有家化妝品工廠重新安排了運營系統,一條價值流負責生產固定產品(即便種類繁多),另一條價值流則負責需求特點完全不同的促銷品。至于空中客車英國公司則是將價值流分成窄體、長程以及寬體飛機。
在服務業需要有創意的思維來識別價值流。以旅館為例,價值流的界定可能依照顧客需求來劃分,例如住宿、餐飲和娛樂。這樣劃分可能需要改變流程設計與資源分配。比如說,支持住宿(例如洗衣服務)的物流就要與支持餐飲(訂餐和送餐)的物流分開處理。
JPF保險公司的處理方式是把幾種相關的工作組合在一起,比如“接單與分類”,以及“系統錄入與分流”。一旦以這種方式建立起價值流,就能決定每條價值流將處理的預期量。
企業建立了價值流之后,就要設計自己的運營系統,以確保從價值流的起點到終點把價值順暢地交給顧客。許多時候,“價值”可能是指一臺汽車或是一條面包等產品。價值流的配置,應該確保產品能在最短的交貨周期內完成訂購、生產與交貨。
就實際而言,這意味著要盡量讓價值流擁有專用設備,以免流程因為必須共用設備而中斷。一旦價值流中斷,生產流程就會延遲,而庫存就會增加。雖然共用設備有時不可避免(尤其是昂貴或復雜的機器),不過通常共用機器的原因,錯誤地試圖降低單位成本,而不是去努力優化總成本。

設備共用本身就有成本,在共用資源過程中所出現的瓶頸問題就是很好的證明。雖然把設備和資源分配給單一價值流可能會使投資凈額增加,不過由于可以降低庫存、縮短交貨周期和減少質量風險,因此長期來看往往更具成本效益。
維持價值流順暢還有一個隱含的目的,那就是把價值流中所可能發生的漏損降到最低。困難之處在于如何建立一個可以同時增加價值和消除漏損的有效流程。以價值流中過多庫存所造成的漏損為例,這可能是因為作業員國積庫存,以防不可靠的機器隨時出狀況。如果機器可靠性提高,那么作業員就不需要累積過量庫存,而漏損也就能得到防堵。
要把產品或服務送到顧客手上,必須結合三種流動:
·物料流(material flow)是原材料經過各個流程轉變,最后交到顧客手上的整條路徑。
·信息流(information flow)是顧客需求或訂單沿供應鏈得到溝通的過程。通過讓每個流程了解下一步該做什么,信息流可推動企業系統確保把正確的產品或服務在正確的時間送達正確的地點。
·人員流(people flow)是人員在流程內與流程間的移動。人員流包括把人員分配到各價值流,以及在價值流之內人員使用設備的方式。
對這三種流動必須同時加以優化,雖然通常來說很困難。以某電信公司為例,該公司想改善修理故障電話線的流程。客服中心接到報修申請之后,必須傳給負責診斷故障、規劃工作和進行維修的小組。確保信息流實時順暢流動,維護數據的完整性,是創造出有效的端對端流程之關鍵所在。進行維修的現場技工(即人員流)的工作量與調度,是決定故障維修周期和人員生產力的要素。物料也需有效率地流動,才能確保現場小組始終擁有維修所需的工具與零件,并確保企業不會因為持有非必要庫存而造成負擔。
前述三項精益原則,處理的都是一個較大的課題:如何配置資產與資源來創造通暢的物料流。不過,首要問題其實應該是如何最好地把顧客需求導入價值流,而這也是精益運營企業彼此分出高下之處。創造流暢的流動本身并不會形成精益系統,因為顧客需求并不是固定的。
真正的絕招并不是針對既定的顧客需求來優化流程,而是要創造出一個自我校正的運營系統,能以最少的資源與配置成本適應顧客的需求。精益運營企業應該能盡其所能滿足顧客需求,而它所采取的行動或推出的產品特色又不會徒然增加成本而無價值產生。這需要企業對顧客需求有真正的了解,并能靈活調整運營規模與步調,以追隨顧客需求而動。
拉動原則往往被具體轉化為看板工具,而通過彈性運營來滿足顧客需求的原則則常常是通過節拍時間的概念來表達。假設一家擅長某種手術的私人醫院一天的手術需求有16次,而手術室每天運行8個小時,那么節拍時間就是30分鐘。這表示資產(手術室、床位、設備、手術工具)以及資源(醫生、護士、管理者)應以每30分鐘完成一次手術的方式來進行組織與優化。現在,假設冬天每日手術需求變成24次。那么節拍時間會縮短至20分鐘,而資產與資源就會需要重新安排(可能需要擴大),才能達到這個目標。
如果價值流不必處理不連續的單位,或是處理量很大時,比如在化工廠或煉油廠,那么節拍時間的概念就需要修正。比方說,化工廠的產品組合必須要能盡量符合需求,即便實際生產率是由化學過程或設備因素所決定。
季節性很強的市場會帶來不同的挑戰。以冰激凌制造商為例,其運營系統必須要找出彈性生產的方法,以適應顧客需求的大起大落。比如在高峰時間找臨時工,或者讓員工在夏天加班,把工時累積起來到冬天休假。
在零售行業運營系統則要能應付午餐時間的需求高峰。也就是說,在高峰時段必須有具備多種技能的員工來處理面向客戶的交易,等到高峰期過后這些人員才又回到后臺的崗位。
在流程的越后面導入越好通過集中規劃或排程職能來管理運營,就好像管理中央控管的經濟體一樣,理論上可行,但實際上卻很少可行,因為要實時管理各種變動并不容易。集中式系統有賴于幾條基本假設,一旦這些假設發生問題(比如交貨延誤、一批零配件存在缺陷,或機器發生故障),那么系統狀況會很快惡化,導致排程越來越依賴個別干預而非集中式系統的惡性循環。
假設生產割草機金屬零件的簡單流程可分為三個步驟:壓模、焊接、上漆。假設某一天顧客需求是300個相同的零配件。一般生產控制系統會依照這個要求,為每個流程列出生產清單。假設依照過去的記錄,壓模平均次品率為5%,焊接為10%,而上漆為20%。那么,生產控制系統會要求壓模流程生產440個零件,才能確保交出300個零件給顧客(300除以累積正品率,0.95×0.90×0.80)。然而波動是一定存在的。或許某天的次品率不是5%、10%、20%,而是10%、10%、25%,這么一來,最后就只剩下267個零件,足足少了33個。提高產量目標不是解決之道;假如某一天的次品率模式不同,那么一開始要求的440個就可能導致大量過剩。
這個例子表明,傳統的生產控制系統往往通過增加批量規模與緩沖庫存,來抵消無法達到客戶需求的風險。這種做法會增加成本,延長交貨周期。而大多數流程復雜度更高,因而問題只會更嚴重。除了對次品率的管理,運營系統還必須考慮,對機器故障與換機次數等因素的假設。隨著產品與流程復雜度的提高,管理信息流的挑戰也更加艱巨。
那么,精益系統有什么不同?精益系統會導入能確定顧客需求的信息,以避免中央計劃經濟或大批量生產的生產過剩或短缺問題。其關鍵是在流程中接近價值流的單一一點導入信息,而不是在價值流中的每一點或遠離價值流的某一點導入信息。之后,把所有其他流程都通過這個導入點與信息相連接,這樣,生產與需求間的具體連接就建立起來了。這是辦得到的,因為控制生產速度的節拍時間本身就是由實際需求所決定的。一旦導入了確定顧客需求的信息,系統便有了依據,能在價值流中拉動產品或服務。但實際上所用的機制,則視運營交貨周期與顧客交貨周期的差異而定。如果前者比較短,那么產品就按訂單來生產;如果較長,則按庫存來生產。
回到先前割草機的例子。假設割草機零件的生產交貨周期,比顧客交貨周期來得長。在精益系統里,我們必須在上漆流程之后保持一定的成品庫存量。(這些用來緩沖生產的中間庫存被稱為“超市”或是“商店庫存”,必須以其位置、數量及補充方法來確定。)如果今天的需求是300個特定設計和顏色的零件,那么這個信息會傳送到商店庫存,并從那里取出零件,送上卡車,交到顧客手上。而取出了這些零件,就會把看板送到油漆流程,告知需從未油漆的零配件庫存中取出300個來上漆,以取代交到顧客手上的零件,并依此類推到價值流上游。
采取這種生產控制法,就不需要預測各種不確定因素。如果要從一批300個上漆的零件中報廢20個,那么上游商店庫存就會再拿出20個替代零件,并發出信號要求生產20個零件來補充庫存。換句話說,實際(而不是預期的)需求會沿價值流傳上去。
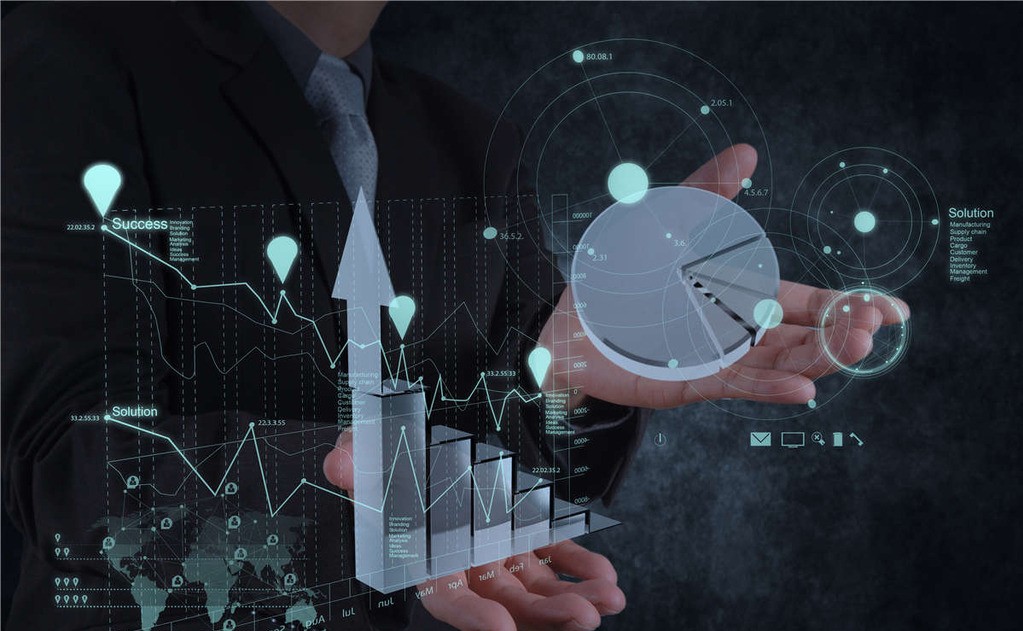
在諸如零售與裝配等行業,價值流難免會在運營過程中斷。究其原因,可能是因為一個流程必須要用到多個價值流共用的昂貴設備,比如油漆設備,或者因為價值流并非依據能夠事先決定的流程,而是依據人與人之間極為多變的互動來組織的,比如租車。這種情況下所產生的價值流就不太確定,其流動易受偶然中斷的影響。要把中斷而造成的損失降到最低,最好的辦法是采用“拉動式”的方法來管理流動的調節。
以油漆流程為例,假如下游各條裝配線所需要的零配件要以批次方式漆成不同的顏色。顯然,每條生產線一直維持連續流動是不可能的。不過建立簡單的拉動式系統,就能減少流程中斷的情形。我們可以在油漆流程后面儲存一定數量已上漆的零件,供裝配線按需取用。一旦一箱零配件被取用之后,箱子上所附的看板就會回到油漆流程。一旦看板累積到預定的數量,油漆流程就會換機為零配件上漆,以替代已取用的零件。這種調節機制簡明有效,可決定流程何時應當換機,以及生產的內容與數量。這樣就使流程可以維持零配件的供應,同時盡量減少庫存。
有人認為精益是一種高度標準化的工作方式,把員工看成機器里的齒輪,不適合特別復雜或波動的作業。這是種常見的錯誤認識。正好相反,正確的看法是,標準化是為實現真正的彈性打下基礎的必要步驟,它為員工帶來了培養新技能的機會,讓他們享受更多彩多姿的工作。
以溫布爾登網球場球童處理波動的方式為例。他們服務的“顧客需求”是出界的網球,這是不可預測的,不過球童卻有辦法對付,因為他們有一套標準流程。這套流程規范了從球童在球場上的位置到網球的取回和交還方式等一切相關活動。球童受過培訓之后,就可以自己做出決定,而不是尋求上級指示。他們可以在身價非凡的國際網球明星身邊若無其事地做自己的工作,既不會造成球員分心,也不會擋了球員的路。
精益環境也很類似。只要能夠讓員工獲得適當培訓,并被賦予維持標準的責任,那么標準就能創造彈性。但是,如果缺乏詮釋的自由度,那么標準化就會淪為種種限制。
運營標準可確保最安全有效率的工作方式被確定下來并重復采用。這對大家都有好處,顧客會得到更好、更一致的質量;股東會因為生產力提高而獲利;員工則有清楚安全的程序可遵循。運營標準還可大大降低新產品引進或流程變更的相關風險。
就最基本的層面來說,標準能確保任務以同樣的方式完成,而無論由誰去完成。標準也為培訓提供了基礎,為改善提供了基準。而標準應被視為靈活的文件,應由運用標準的工作小組來持續更新。一旦流程改善,標準也應該更新,以跟上變化的情況,而新標準也就成了繼續改善的基準。
無論是在酒店接待賓客、在客服中心接聽電話,或在工廠制造汽車,標準都能確保作業質量,并保護品牌與其所能取得的市場溢價(marketpremium)。而標準對彈性人員配置系統來說也十分重要,它可使員工在各種任務或工作單元之間輕易地互換。這么一來,公司就能更快地回應顧客需求的變動,從而使生產力最大化。
在工作場所應用可視化管理,是將彈性引進運營系統的重要關鍵。這樣除了可以使物料與工具的位置清楚可見,還能在不同工區、不同工作現場之間創造出共同性,因而更容易轉換人員。
精益運營體系的最后一個原則與質量管理有關。在豐田汽車工廠中,裝配線員工若發現無法在正常工作周期內解決的問題,則有權停下整條生產線。在這種資本密集度極高的環境中,停止生產的成本是很高的,但是豐田認為,產生次品的成本更高。
不僅如此,豐田相當信任一線員工對于質量問題的判斷。這很特別;在其他企業中,產品缺陷通常以兩種方式處理。其一就是把質量專責小組叫來調查問題所在,并決定如何處理;其二,則是把質量問題層層上報,直到有人有責任或勇氣來處理問題。但是采用這兩種方式,從問題被發現到得到處理都會經過較長時間,而在此期間可能還會繼續生產出有缺陷的零配件。
精益運營系統正好相反。異常狀況一發生就會被發現,如果可能的話,流程就會停止,直到根本原因被確定并得到控制之后,流程才會重新啟動。
這迫使組織把問題解決能力制度化,并推動組織轉向持續改善。這樣嚴格的流程對顧客大有好處,因為它可以消除有缺陷的產品與服務、縮短交貨周期并降低成本。
文章來自網絡,版權歸作者所有,如有侵權請聯系刪除
“精益六西格瑪讓我們的質量、效率、成本、管理上了一個臺階,并得到了美國質量協會、中國質量協會等單位的獎勵和認可。”
———上海貝爾阿爾卡特朗訊經理