做QA應該是水無常形,兵無常法。Checklist、指標僅僅是冰山一角,最關鍵需要建立的是人對產品質量態度和責任感。我們經常分享結果(模板、流程),為什么做和如何思考做這個事的思維方式更加值得分享,明白當初為啥做這個事,才可以促進態度和理念的復制,否則只能模仿形而失去了最重要的神。當然,各個優秀實踐,可以作為一種案例可以進行貨架化知識管理,便于查詢。
§實踐篇§
Ascend P1 是我司的第一款旗艦機,高層期望開始創造華為的品牌,責任重大,同時AP+modem第一款商用,HAP 5.2 首款商用,首款LCD/TP一體式來料,華為最薄設計,N個固件新器件…… 困難重重。 最要命的是,Ascend P1 半路接手,同時要求項目提前計劃2個月上市,跟著項目組走過了最瘋狂的一段時間,本著找到關鍵的20%,重點突破,小循環逐步改進的工作思路,做了不少嘗試,有好的結果(我們贏得了100萬,),也有不好的結果(改版次數多,VS試制流程執行不到位),回首看看,有的也有失,簡單總結一下給大家分享,歡迎各位方家批評指正。
一、 確定項目質量工作的思路:
認清現狀:
1、 上海團隊第一次做智能機,能力不足(北研團隊軟件人均問題單修改能力是1.5個/天,上海團隊最多就是1個/天),項目團隊對項目保質按期交付還是存在疑慮。
2、 Ascend P1是華為公司第一款旗艦機,余總及其重視并且要求提前上市,提出提前2個月交付的要求,并許諾200萬項目交付懸賞獎(100萬/月),版本經理比較狂熱。
換位思考,明確工作思路:
“項目團隊不是不希望改進和提升,更多的時候是他們遇到問題不知道如何去改進。”
終端是強項目交付牽引,但是項目運作又是強資源矩陣(至少目前是),項目交付應該還是第一位的,整個項目團隊的成員都還是希望能夠按期交付,按質量要求交付。
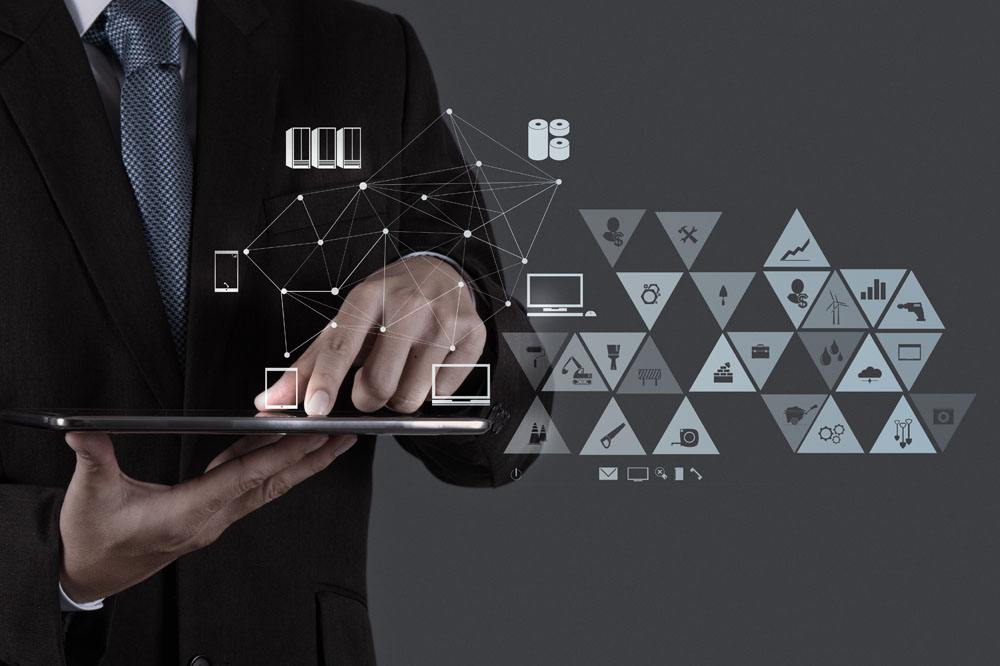
新軟件平臺,新硬件平臺,新項目定位,一定會遇到問題,而且是一堆的問題,拿著質量的要求、標準去要求團隊達成,是一種質量人員的做法;融入到項目運作中,切實的協助項目組識別關鍵問題,解決運作過程中的問題,也是一種質量人員的做法。
項目按期交付,拼命往前沖的大勢無法阻擋,那我寧可選擇融入到項目團隊中,實實在在的將產品質量做好,切切實實的將項目運作過程中的問題解決。雖然將面臨一堆的問題,但是我陽光總在風雨后,不經歷痛苦,哪能感受幸福。 ^_^
找到問題關鍵的20%,集中優勢兵力重點突破,采用小循環的方式逐步改進,成為和U9200一起奮斗過程中的主要工作思路。
二、 扮演好幾個角色:
1)剎車人(狂熱隊伍中的冷酷者)
如果說質量中最不愿見的是“變量”,項目管理中最不樂見的是“變更”,那么項目運作過程中最害怕的是“狂熱”,團隊一旦開始狂熱,如果不及時的剎車,那么項目運作必然失控。
前段時間我們HR祈宇,和我交流時說:“如果別人離職,我可能還會想法挽留一下,但是你小子太冷酷了,要么不干,要干就一定想清楚了,而且是無法被動搖的。” 沒錯,在狂躁的項目運作過程中,你一定要冷靜,甚至冷酷,要仔細觀察,認真分析,撥開迷霧看到本質,因為真相只有一個。
? 音頻TDD改版
TDD是系統性問題,TR4A后出現了反復,修改音頻問題,結果導致射頻性能出現了下降,因為需要提升射頻性能,達到公司要求的余量要求,急著要改版。
要保證修改的有效性,因此直接回的郵件“不同意改版,需要將修改方案評估清楚”(可惜原郵件找不到了 ^_^),拉上射頻有線、天線、音頻、硬件基帶的人一起評估修改方案,現場討論中發現了幾個新問題,重新進行方案驗證……
Tips:
各部門的研發兄弟都有一個向上的心,都希望自己的領域沒問題,往往容易犯顧頭不顧腚的毛病。我們希望各領域優秀,但是我們更加希望產品是優秀的,因此就需要取舍和平衡,作為PQA應該系統的去思考問題,要引導產品達到最佳的平衡,當然建議在平衡的前提下,也可以獲取某方面的最優化(賣點、亮點)。
在交付壓力的牽引下,一定會想方設法的去趕試制,但是多次試制更多的可能是帶來資源的耗費,畢竟華為公司每個項目上的資源并不充分。要冷靜對待問題,珍惜和把握每一次機會。
心若冰清,天塌不驚;
萬變猶定,神怡氣靜;
塵垢不沾,俗相不染;
虛空甯宓,渾然無物;
無有相生,難易相成;
份與物忘,同乎渾涅;
天地無涯,萬物齊一;
飛花落葉,虛懷若谷;
千般煩憂,才下心頭;
即展眉頭,靈臺清幽;
心無罣礙,意無所執;
解心釋神,莫然無魂;
水流心不驚,云在意俱遲;
一心不贅物,古今自逍遙!…… ——《風云》中聶風的冰心訣
豐田的案例:
大家都知道豐田汽車公司,可能這家公司是當今社會被人研究最多的企業之一。該公司的經營和管理哲學獨樹一幟,其中最著名的管理模式是“豐田生產方式”(TPS),業界稱為“精益生產”。“豐田生產方式”的核心是PDCA。有人說,當一個典型的美國公司遇到一個問題的時候,如果這個問題必須在一年內解決,該企業會用3個月來做計劃,用另外3個月來執行,再用6個月來做微調,處理遺留問題。而豐田在面對類似形勢的時候,會用11個月來做計劃,用1個月來實施(根本不會留下任何遺留問題)。這種說法雖然比較夸張,但是它體現了豐田對于PDCA的獨特理解和經驗總結。豐田人認為:計劃至關重要!只有徹底的計劃(從多個角度全面了解了形勢、準確地發現了問題產生的根本原因、考慮可能發生的各種變化、以及參與者的認可或者上級的批準后),實施、檢查、處理的結果才能高效達成預期的目標。
?
2)公正的中立人(公正公平,但是一定要保持中立)
質量人員在華為的定位是中立的,因此總會有這樣那樣的糾紛問題要質量人來仲裁,希望得到中立的評價意見。當然在研發內部出現類似情況仲裁還可以,因為我們畢竟還呆在研發區。但是對于出現跨研發領域的時候,和大供應鏈體系(制造&采購)交流的時候,供應鏈體系經常認為我們是屬于研發體系的,容易存在略帶敵對的和我們交流。如此情況下,我們應該如何的處理?
?
Tips:
我分享一下我的做法:
1、首先是澄清具體問題,不要和對方陷入到度量指標,考核指標的漩渦中去(影響產品的具體問題都已經解決了,指標不滿足要求也難)。
2、對于問題要制定應對措施和具體責任人,從問題后續的實際表現去評估活動是否有效和相應的進展(避免出現活動做了,但是沒有效果)。
3、該踢一腳的還是要踢一腳(忍無可忍無需再忍),當時言辭要客觀,避免采用主觀類的語言(這個時候就需要體現質量人的專業素養了 ^_^)。
?
U9200-1 TR6直通率問題 案例:
TR6的時候最容易遇到的就是因為直通率問題,制造體系和產品較勁。U9200-1 爬坡后,為了解決直通率問題,研發體系一直是有人制造現場的(具體的派兵布陣也有一個小實踐,在后面和大家分享),組裝段的一次直通率從爬坡的20%,一直穩定到了85%以上,而且還有不斷上升的利好趨勢。當時因為SMT段的一次直通率低,而且不穩定,直接導致全工位一次直通率就被拉到了80%以下,而且極不穩定。
客觀公正的給制造體系的各位老大分析了一下U9200-1的直通率趨勢,和TR6的一些要求,SMT段的問題很快得以控制和解決。
?
我發的郵件:
制造體系回復的郵件:
鄒總的郵件:
?
制造代表主導直通率提升:
三、 一點點實踐,一點點認知:
1) 關于產品質量評估:
產品質量評估是QA是一定要做的,但是如何做,各地有各地的模板,各人有各人的習慣,我的思考和寫作方式分享給大家,請各位方家拍磚。
質量評估對于領導們來說,是希望看到一份產品質量狀態的全貌,能夠包含產品各方面的完整信息,它除了用于領導的監控,其實也應該是很夠很好的引導版本經理規劃后續的重點工作,因此可以聯合版本經理一起來寫,在寫的過程中,同時也是對項目狀態的一個梳理。第一期可能比較困難,當時后面的只要逐漸更新即可。
我們寫一份報告,首先需要列清楚需要體現的維度,然后是收集寫作素材(往往會有現成的素材),最后再用客觀語言來表述。原始的素材不一定需要重新開始,往往周圍的領域已經有人在做了,因此要注意積累渠道和信息源。 積累人脈和渠道的最好方式是分享,將你的工作成果和他人分享(包括業務部門的人),尤其是提供信息給你的那些兄弟,并且要心存感激。 —— 有感于李志《其實你不懂項目管理》
對于產品質量狀態,我通常會從如下的角度思考,當然針對不同的項目背景,所處階段進行調整,這個需要從實踐中積累經驗。
?
需求實現:在TR4之前需要重點關注,尤其是軟件需求。可以聯合SQA做些事情,Ascend P1就很感謝于姐姐,組織軟件、測試、SE等領域做了三次需求實現梳理&排序,明確下來哪些必須在啥時間點完成,哪些需要CCB裁剪。因為需求的顆粒度不同,很多細節上把握不到,Ascend P1需求評估會上明確哪些可以裁剪、哪些必須實現后,對于實現過程中的細節問題,允許通過CCB的方式進行裁決。(對于渠道銷售的可以參考操作,對于運營商定制的,一定要和運營商PK,北京這點應該做的挺好,上海火候還差點。)
軟件單元測試:現在項目都敏捷了,單元測試如何做,如何評估充分性,沒有啥心得,我一般都咨詢SQA。
硬件單元測試:主要關心沒有測試通過的項目,對于新器件的驗證情況也需要重點關照,我沒有現成的Checklist,更多的是和開發人員、器件組負責人交流驗證方案和結果。建議多看看硬件組器件相關的案例,測試對于器件替代的方案,供應商器件出廠的測試要求,帶著疑問去和器件組的兄弟們交流(我作為QA參加過LCD、音頻的器件組工作,梳理過音頻流程、整理過音頻小組的運作方式。),花點功夫在平日,積累交情的同時也能學到不少東西。
硬件測試(含可靠性測試):除了關注測試的結果和發現的問題以外,我更關心的是測試的覆蓋度(所有用例是否都覆蓋,V試制和VN試制是否都完成應該的測試覆蓋)和問題發現趨勢(如果前幾次測試沒有問題,但是后面有問題,一定會追問一下為什么),歷次修改方案也需要和測試用例進行一個比對,防止方案遺漏。Ascend P1 這個工作其實是我提供想法,工具表單的支撐,數據整理工作基本上都是硬件測試接口人做的,需要感謝一下陳雪蓓MM。
軟件測試:前期更多地都是關注DTS上的問題,Ascend P1因為和Ascend D1是同軟件平臺,所以修改問題評估的時候一直是一起評估的,盡管工作量大點,至少避免了遺漏。其實還有一個不同軟件版本的關系樹可以參考,軟件組兄弟應該是有在維護的,我前期基本上是通過交流獲取方法,去確定評估方案,最后看到這個樹的時候,后悔了好一陣子。這個樹可以幫助QA理清楚問題評估方案,以及關鍵問題的修改合入策略,簡單有效。
準入測試、Beta測試、現網測試:這個是測試經理制定的,只是在方案確定的時候,需要和測試經理交流一下,我是借用的信息。就是在識別和評估發現的主要問題上和測試經理交流了不少。
Ascend P1測試這塊的信息基本上都是測試經理錢群JJ總結的,非常全面&完整,我就是應用&提煉。
試制問題:DFx or 試制代表手上有非常完整的試制問題清單,最好Review一下,根據經驗判斷一下那些是TOPn和必須解決的。我有幾年制造端產品質量管控的經驗,所以判斷相對比較容易,其實就是判斷此問題是否影響產線效率,因為產線進行的是機械的、重復的操作,簡單的才不容易出錯,高效的才容易落實,對于產線問題處理要記住“簡單就是美”,所以解決方案重點要思考工具&方法的輔助,盡量減少配置或者選擇。其他的問題比例、危害度之類的需要辨證的看,不要被數字欺騙,PQA有機會還是多去產線轉轉,經驗還是需要積累的。
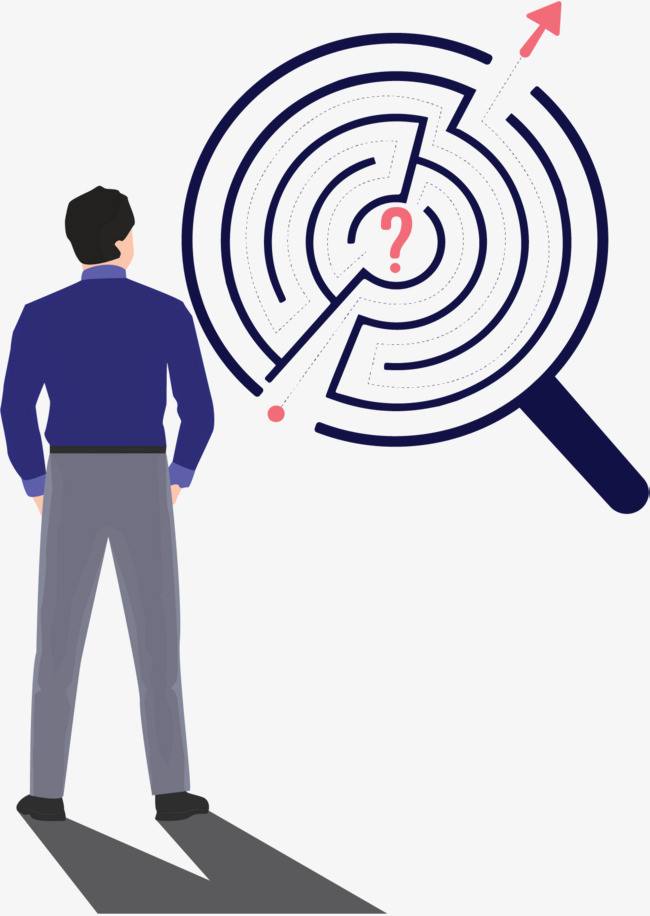
Ascend P1 有一個關于返工的優秀實踐,對于產線上出現的故障機維修后,統一升級軟件到PT測試之前,然后直接往下走流程,深得制造兄弟的喜愛,因為沒有那么多狀態需要控制。對比北研的返工升級方案,每個測試工位的工具都有返修流程設置,我們研發的角度想,是給了你很多的選擇,可以從不同的工位進行返工,但是我們似乎忘記了,產線玩的是海量制造,不是手工作坊,原則越多,產線不同的產品狀態越多,越不容易控制,越容易出現疏漏。如果簡單的到只有一種返工方式,那么我們核心需要改進的點就是如何減少返工,而不用關注如何增加返工的途徑。
物料問題&器件驗證:影響產線的制程問題從試制問題清單中單獨拎出來,還要關心的是器件驗證的情況(新器件引入&器件替代),直接在PDM上看BOM編碼的發放情況就能知道器件驗證的進展,然后有針對性的去咨詢相關的責任人。
問題單:P1這個軟件新平臺到目前為止一共發現了14K以上的問題,分布在P1、D1不同的子版本上,還是花了一點小心思的,后面再細講。對于質量評估而言,要體現一個整體的趨勢(問題發現趨勢,遺留問題趨勢,DI趨勢……),根據展示即可。不要忘記了,調處你認為最關鍵硬件、軟件、制造類問題明確的寫出來。
市場:這個基本上是版本經理在關心,我了解相關信息,只是用于調整相應活動的開展方式。質量評估上基本不涉及。 ^_^
收集完數據后,就需要整理成文章了,可以看看下面兩個膠片,學習一下應該如何匯報和延時,附了一份早期的產品質量周報。
?
一份好的質量評估報告,其實是可以被復用的,我寫的P1質量報告就被用于給余總萬總的匯報,EDCP發貨的評估。一份好的質量評估報告,首先要有一個好的框架,第一份可能困難點,但是后面的話就是不斷對信息進行刷新。(多么希望后續產品的信息可以集成化在一個系統中,方便查詢和展示)
?
2)項目問題&風險跟蹤:
對于FP時代,產品開發規模小,一個項目組例會就可以Cover,但是我們已經步入了智能機時代,開發Ascend P1 這樣一款旗艦機,曾經開玩笑的和版本經理數過人頭,FP的30個人,已經演變成了300人以上的隊伍,還是一個項目周例會解決問題的效率會比較低下。
P1 采用的實踐是每日站會的方式,各領域代表將各領域前一天的工作進行總結,將這一階段的主要問題進行反饋,五角經理輪流主持(雖然能夠起到練兵的作用,但是也有不好的地方。),統一寫在白板上,進行信息共享和展示(不知道會不會有信息安全隱患^_^)。
項目問題、事務、風險統一跟蹤,采用Excel自帶的共享工作簿功能(不會的同學自己百度、Google,打電話給我也行 ^_^),項目組全員共享,每個責任人對自己任務進行進展更新,支持多人同時更新。
?
待改進點:
1、 項目在一開始的時候還是有一個FMEA的項目風險跟蹤表,我是中期介入的,沒有很好的延續用起來,盡管我將遺留的未關閉問題已經放到共享工作簿中,但是后面的監控沒有做起來,執行效果不是很好。
2、 每日站會的效果不錯,但是五角的主持風格和思路不太一致,內容更新上延續起來比較差。
3、 各領域的信息匯總各領域代表各有風格,信息不能很好地實現對接,靠單人力進行拉通,工作量巨大。
?
改進建議:
1、 各責任人需要將跟蹤起來,項目POP可以作為跟蹤責任人。最關鍵是,要跟蹤的事務和項目各領域代表日常工作銜接起來,利用這個牽引各領域代表開展項目工作。
?
2、 五角都比較新,能力需要培養,如此方式可行,但是要統一會議主持的規范化內容(具體哪些塊內容需要問),在白板上的謄寫規則也要有大的定義,更換周期不要太頻繁,雙周或者一個月換一個比較靠譜(雖然說68天是讓人養成一個習慣的建議時間,當時偏長了因此借用以前高考中的一個推薦記憶方式7天一學習周期,7天一復習周期,隔2周一個再復習周期)。
?
3、 各領域的日常事務跟蹤和項目的能夠進行匹配,最好統一使用項目集成跟蹤表的格式,便于后續的復制粘貼,如果能夠實現系統化就好了(PLM項目的時候,有幸和三星顧問交流過,三星當前基本上用的就是一個系統進行項目任務的跟蹤,羨慕中)。
?
3)DTS問題:
DTS 問題單是每個QA都需要關注的,那么應該怎么看?
1、 問題單看是要看的,對于智能機那么多問題咋整,首先要學會的是增量的看。DTS問題單號都是體現了一定的順序,上次看到哪個了,下次從下面一個看起。或者借助工具標示出來哪些是新增的。(自己寫了一個小工具,后面會有共享)
2、 問題要學會分類看,可以按照當前責任領域看,可以按照問題模塊看(雖然測試和研發的分類不太一樣,當前填寫的也不準)。
3、 對問題狀態有變化的需要關注,特別是狀態往回退的。(當然都可以借助于工具)
但是最最最重要的,是將產品的問題單跟蹤和統計規則歸一,過多的方式,只能夠產生混亂,大量的時間浪費在澄清和扯皮中,對我們已經被壓縮的不能再壓縮的進度是一種極度浪費。
?
我們在Ascend P1上都做了什么?
?
A、問題單作為數據源的運用:
1、 問題單統計工具歸一:
軟件有軟件的統計方式,測試有測試的統計方式,產品有產品的統計方式,OK,我們首先做到的就是工具表歸一化,做了一個工具表,這個世界平靜了。其次,統計規則統一,P1、D1軟件類問題合并在一起統計(優先將試制提的問題直接剔除,其他的評估時候再判斷),評估為不修改、非問題的直接不統計,問題單繼續走。
?
2、 問題單排名方式歸一:
以前做QCC的時候,有一位同事說過,如果要讓這個活動搞起來,就要讓馬賽起來,要形成競爭。OK,規則和統計方式已經統一了,按照資源組的方式(軟件細分到各小組),進行當前問題單狀態排序,每天通報。工具相對比較傻瓜化,自己先發幾期,后面找一個慧通的兄弟,教會他使用方法,都是他來發,軟件問題就這樣活性競爭起來,大家也知道如何做了。
?
3、 問題單評估記錄歸一:
智能機問題實在是多,P1、D1新平臺旗艦機,問題尤其多14K啊,排序找重點問題,通過會議紀要的方式記錄,后面跟蹤有困難。OK,沒問題,會議紀要照發,但是每個問題單的結論統一記錄到工具表單中,評估結論直接放在里面,便于查詢、篩選,狀態也一目了然,簡單&直接,大家都喜歡。
上面說的天花亂墜,其實就是一個Excel表+Vlookup函數,所有需求都搞定,而且盡可能采用自動化處理,每天0.5-1小時工作量,大家方向很一致。
原來還想再優化優化,現在看來要留給后面的有志之士了。 ^_^
?
B、DTS 問題單數據如何展示:
數據源既然已經有了,如何用呢? 做一個有心人,看看我共享的“咨詢工具”系列吧,里面會給你靈感的。
1、 展示問題發展趨勢:
最常見的展示方式,大家大家最愛用,大家也都能看得懂。
到底哪種趨勢比較適合P1,我下了不少功夫,北研M860、C8860、U8860、S8600、U8600的數據圖形我都做過,大家不妨也看看,其實用用R版本度量工具,一切其實很簡單。
2、 展示研發和測試的PK:
折線圖也可以這樣用哦,研發解決問題和測試發現問題可以這樣對比,是推研發解決問題還是測試發現問題,很清晰。
3、 展示研發解決問題的速度:
地層圖的使用,這個是和總體組一個GG學的,研發能力基線也可以得到驗證哦。
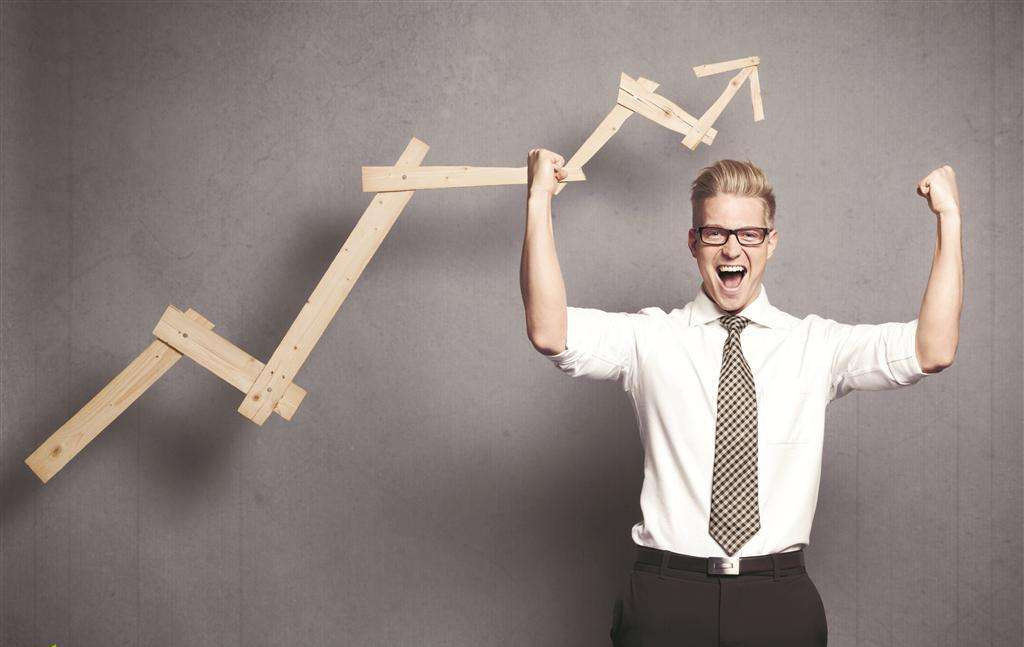
?
C、關于DTS問題單,不得不說的痛:
1、 步驟之長世所罕見:
我經歷的那么多家公司,我們終端用的流程真可謂歷史之最,大量的問題單采用的是13步,基本上是業界的2倍。增加了那么多審核&確認的步驟,是為了啥?問題單我的理解,就是驅動研發工作的一種工具,研發人員日常的工作就是解單,慎重合入,其實控制一個合入入口就可以了,將問題修改方案的評估做在平時,為啥還要體現流程,結果現在問題單反而流不起來了,過TR點還要催單,純粹的人力浪費。走一個問題單,需要多少人力成本,不知道有沒有人算過。
?
2、 必填項填不準,如何利用數據:
和軟件開發的兄弟交流過,問題模塊分析,居然軟件和測試的不太相同,那應該如何去正確理解呢?是不是需要培訓? 同時也折射出一個問題,測試能力問題,如何判斷這個是一個問題,是測試的必備能力,但是現在似乎差好幾口氣。
DTS原始數據上那么多的問題點,數據分析如何進行? R版本度量工具基本上是有力使不上。當前的DTS數據我對它是又愛又恨,真的像是一盤沒有絞肉的麻婆豆腐,真希望有哪位大俠可以像《中華小當家》中演的那樣,創新改良后作出一盤沒有絞肉的夢幻麻婆豆腐(大豆做絞肉)。
從DTS問題中折射出的測試問題:
?
1、 測試只管發現問題,不管判定是不是問題:
海思的測試同事曾經很好奇地問過我,終端的測試很奇怪,判斷是否是問題居然說是研發來做,研發的時間最寶貝,這個不是應該測試來完成么? 因此在海思能夠看到測試的兄弟,整出來各種腳本,測試工具,羨慕啊,啥時候我們也可以才這樣?
過年前,P1的問題發現比較少,因此嚴重反饋過幾次,導致結構問題大量上升,結果后來一打聽,原來測試開展了外包和華為測試的大比武,大搞自由測試求單,是我們的用例發現不了問題,還是我們的測試用例不完整,那為什么不在10幾K的用例開開刀,改良改良呢? 3-4重交互后發現的問題,是否可以將解決的程度降低?
以前李小龍曾經說過,做小靈通的時候總共的用例才1K,但是已經比CDMA FP的幾千條用例發現的問題多了。其實,測試用例是貴精不貴多,如果是界面全覆蓋,那想辦法自動化即可,對于交互類的問題,可以人工測試,哪些是常用的交互,哪些問題是用戶最關心的,800熱線、FFR退機,都可以找到線索。
?
2、 只關注了數量,忘記了質量:
如何去評判測試的質量,其實很簡單,看看對于測試提交的問題,多少個問題研發是需要修改代碼的就行了。那么我們P1 一共有14K多的問題,我簡單的統計過,對于已經關閉或者撤銷的問題,已經表示是問題解決的應該不超過60%。HAP平臺也的進行總結的時候統計過,一共處理過8K的問題單,但是需要改動代碼的不超過40%。 那么剩下的那些問題都是咋整的? 這些問題是不是浪費了呢? 我沒有仔細去分析過,建議測試總結的時候可以看看。
4)試制現場質量控制:
?
幾個現象:
1、 大家都很忙,各忙各的,一旦是重大項目,各部門都出差,出差日報就滿天飛,后端的兄弟很郁悶,到底應該看那份信息,哪份信息最準確?
?
2、 DFx或者試制代表統籌組織,但是“布朗運動”比較明顯,問題攻關全面開花,對于本次試制而言到底哪個問題需要重點解決,優先解決?兄弟們很困惑。
?
3、 我們在現場改善了很多東西,需要落實的要求很多,EMS的技術員一個人接口我們很多人,我聽誰的?EMS的技術員很郁悶。
?
4、 我們落實了不少方案,效果咋樣,有沒有新增問題,產線報表、數據咋沒有人看呢?
在Ascend P1上的實踐:
產線跑不順,出現的各類問題無非是物料、制程、設計三類。物料問題直接進行篩選,和供應商明確后續的交貨和驗貨要求,基本可以告一段落。制程問題關鍵是看提升員工的熟練度和核心工位操作的正確性,這個是需要一點點看,一點點糾的,只看報表而不在現場是解決不了問題的。設計問題一旦出現,必然是高比例的不良,那攻關一定避免不了。針對上述的認知,進行了如下人員布局:
? 跟線人員分為兩個職能組:巡線組和攻關組,各設立組長一名。
? 巡線組:量產爬坡EMS配得都是新手,因此要加強巡線動作,重點關注關鍵工位的操作正確性和可能由于操作、夾具不良導致的潛在問題。巡線組比較辛苦,跟著實際生產班次走。
? 攻關組:負責關鍵遺留問題的攻關。
? 信息交互方式:每日9:00早站會,小組長將兩組信息總結并交流互通,制定新一天的工作計劃。
? 改進效果確認:每日產線問題的梳理,各種問題的趨勢判斷,識別需要重點關注的問題(之前是我主導,后續教會DFx或者試制代表)
? 成果及時落地,關鍵工位識別,相關注意事項增加到偉創力IPQC的巡檢要求和操作指導中。
待改進點:
當前試制開工會關注度不足,每次試制需要關注啥,上次遺留的哪些問題已經解決,具體落實了哪些措施和活動,哪些問題不解決,一定要試制前達成一致。
試制的資源是有限的,試制的次數應該是需要受限的,版本經理需要珍惜每次一試制機會,QA能夠制止試制,當然是最好的。^_^
?
5)EWP分析
EWP分析的目的應該有兩個,1)早期發現問題,將后續會影響故障率的問題扼殺在搖籃中(判斷準確需要經驗);2)解決的問題作為經驗優化到設計規則或者經驗案例中去,未解決的遺留問題合并到FFR改進中跟蹤。 當前我們更多關心的是第一個目的,這個無可厚非,也是正確的,但是我們手頭的資源是有限的,問題一定要排序解決,不能全線作戰,否則一旦產品過多,紊亂場面無可避免。(北京楊海波EWP分析經驗不少,可以咨詢。 上海沒有專職團隊對EWP負責,對資源的利用和配置要求更高。)
文章來自網絡,版權歸作者所有,如有侵權請聯系刪除
精益六西格瑪讓我們的質量、效率、成本、管理上了一個臺階,并得到了美國質量協會、中國質量協會等單位的獎勵和認可。”
———上海貝爾某某公司
?