以日本汽車行業為例,日本的汽車工業主要從第二次世界大戰以后崛起的,五大汽車廠商(豐田、日產、東洋工業、三菱和本田)的產量占了全國總產量的八成以上,其中,豐田和日產就占了一半。這個格局持續到了1973年的石油危機,豐田公司憑借其精益管理的優勢把老對手日產公司摔到了后面,結束了日本汽車工業的兩強時代。
?
豐田公司自豪地稱精益管理的源泉——豐田生產方式——為“經濟蕭條時期也能掙錢”的生產方式。1973年以后,日本的其他汽車制造商開始學習豐田的生產方式,形成了各具特色的生產經營方式,但他們的基本特征是相同的。
?
自70年代起,隨著精益管理在日本汽車業的普遍推廣,日本汽車工業開始進入高速發展的歷程,到了1980年,日本汽車的年生產總量達到1100多萬輛,首次超過美國,使美國第一次失去了世界汽車市場上的領先地位。日本在第二次世界大戰結束時是一個汽車小國,又是經濟窮國,能夠取得如此卓越的成就,可以說精益管理起了決定性的作用。
?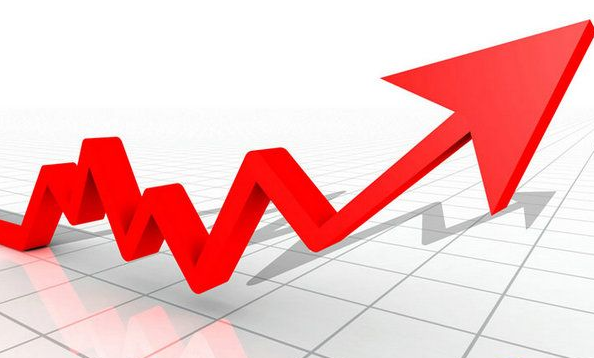
歐美汽車業曾把日本汽車業的成功總結為三條原因:一是日本的低工資;二是日本政府的保護政策;三是大量采用高新技術和先進設備,如機器人等。
?
但進入80年代以后,前兩條理由已不復存在,而歐美各大汽車制造商也紛紛投入重金,采用最新技術,意在提高自己的競爭能力,欲在汽車市場上與日本廠商一爭高低,但并沒有取得明顯效果,最根本的原因是歐美廠商的生產系統的競爭力不如日本對手。精益管理在以下方面具有明顯優勢:
?
1)?人力資源利用優勢。采用精益生產方式,全員勞動生產率是大量生產方式下的2倍。
?
2)?新產品開發周期短。日本企業開發一輛全新的車只需4年左右,而美國需要6~7年。
?
3)?在制品庫存極少。日本企業的在制品庫存量只有大量生產企業的1/10。
?
4)?廠房空間小。采用精益生產,同樣規模工廠的生產面積只有大量生產方式工廠的1/2。投資也只有1/2。
?
5)成品庫存低。由于是準時化生產,嚴格按需要投產,成品庫存是大量生產方式庫存水平的1/4。
?
文章來自網絡,版權歸作者所有,如有侵權請聯系刪除
“感謝冠卓咨詢老師對項目組的全程輔導,通過做項目我們學會了如何用系統科學的方法分析研究問題;開闊了我們的視野并讓我們的管理人員明白了團隊協作的重要性?!?/span>
——北京某電器公司