理念:數據的改善是暫時的,只有思想的改善才是永恒的。
系統方面:豐田生產方式以徹底杜絕浪費為目標“一個目標”;在連續改善的基礎上“一大基礎”;采用準時化、自動化的方式、方法“兩大支柱”;追求制造產品和理性的生產方式。
重點學習收獲:
一、如何杜絕浪費?
1、每減少一個生產隔斷點、中轉的庫存、等待和搬運……等,浪費就能減少一些,生產周期同樣縮短。(5個主要方法:斷點合并、迂回到直傳、無序到有序、亂流到整流、分工到合作)。
2、精益不只是清除浪費,而是要剔除無價值的,并做好有價值的(找出因果兌現邏輯;針對結果目標;建立標準-維持標準-管好三變-持續改善)。
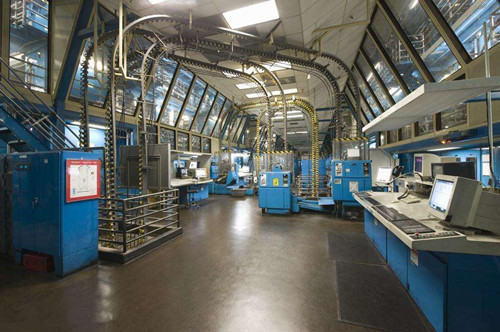
二、如何持續改善?
任何一個改善成果都不會直接變成真金白銀,一定要走完最后一個過程,要兌現,并且是全公司、全口徑角度的核算兌現,否則就是紙上富貴。改善成果考慮公司整體利益最大化,不盲目追求單工序的產能最大化。
如何進行現場改善診斷?
人:
1、人的時間去哪了?利用山積圖分解工作流程,查找如拆、吊、裝、試對應的時間合理性;利用面條圖連接現場各進料、生產、庫存、倒運的關聯點,尋找合理的匹配性;
2、操作技能有無差別?利用餅形圖統計各班、各人的日、周、月指標對比,確定技能差異;
機:
1、效率,設備的時間去哪了?利用設備綜合效率(OEE)方法,收集設備的時間損失,如計劃外停機、故障停機、生產轉換、空轉、速度緩慢、不良品產出等;
2、維護保養是否到位?查找并核實自主點檢、現場記錄、保養周期的執行落到程度及真實性;
3、工具、工裝的問題點及可改善性;
料:
1、流動的合理性?利用物料流動圖來明確流動路線,查找搬、倒、發運的浪費;
2、品質的保證?從來料質量、過程質量、返工狀況三方面進行統計分析;
3、庫存的合理性?利用庫存地圖觀察庫區匹配,并通過庫存天數觀察與生產周期的匹配浪費;
法:
(這里想到了三基管理)作業操作是否符合標準?檢驗、檢查制度的合理性及是否執行?管理標準的落地及可持續性?
環:
現場的5S管理、安全意識的養成、現場溫度、濕度的變化、空間的合理利用。
三、如何準時化、自動化生產?
1、準時化(JIT):將“終點”變為“起點”,以最終客戶的需求為生產起點,強調物流平衡追求零庫存。主要做法有拉動式生產(生產進度-運輸定量-1小時庫存-生產停止-物流停止-訂單減少-在庫量恒定)、看板管理(實時的生產型號、數量、指標、異常顯示)、設備的合理與快速轉換調整(可保證多車型在線混流生產)全員的現場持續改進活動、專業化分工協作。
2、自動化:為防止自動化在機器出現異常時,自動生產出大量的不合格品,豐田推行帶有人字旁的自動化,是一種發現并且糾正異常的技術,達到了異常自工序完結的目的。
四、其他亮點:
1、培養人:設有人才培養中心,新人培養三個月達到崗位要求后上崗。
2、尊重人:5kg原則,操作5kg以上零部件均配備有重力輔助裝置,可減少人員作業疲勞。
3、布局:整體布局緊湊,全立體空間利用(車架、座椅、車門、玻璃有序穿插),并有良好的道路規劃,員工、無人駕駛、有人駕駛設專用道。
4、供應商:周邊12家主要供應商有序排列,成立供應商支持中心,提升其質量保證的能力,并通過取消入廠質檢,給予其質量保證的壓力。
5、現地現物:
對每件事都要重復問5個為什么,直到找到問題的根本。
各層管理者,想做好工作,想執行到位,除了親自到籃球場上去投籃,沒有更好的辦法。(比如:①地上一灘油?設備滲油。②為什么設備滲油?油封損壞。③為什么油封損壞?質量不好。④為什么就這臺有問題?設備振動。⑤為什么設備振動?水平儀摔壞,找正問題。)從原因、目的、后果、條件、制約全局觀考慮,防止局部或不徹底改善。
6、如何自身精益轉型?
①識別自身系統、人員的理想狀態。
②識別自身系統、人員的現在狀態。
③識別自身系統、技術的目標狀態。
④制定自身系統、技術轉型路線與計劃。
⑤識別自身適應與人員的目標狀態。
⑥制定自身適應與人員(知識、技能、心態、行為)轉型的路線與計劃。
⑦設計與展開自身系統與人員的改善行動。
文章來自網絡,版權歸作者所有,如有侵權請聯系刪除