要盡量剔除看板
走進(jìn)一汽豐田天津第二汽車制造廠的總裝車間,第一印象就是整潔、有條理,各類區(qū)域劃分清晰,物料堆放量很小。
門邊的配貨區(qū)整齊地碼放著裝滿零部件的物料筐,每個物料筐上都有一個用透明膠帶粘貼著一張裝在小小的透明塑料袋中的紙卡片。
每個筐里工件的種類和數(shù)量都和那個紙卡片相對應(yīng),同類的被碼放在一起。旁邊有好幾個工人在忙碌,將物料筐移到推車上,裝滿一輛車后整裝待發(fā)。那些裝在袋子里的紙卡片就是豐田生產(chǎn)線上最典型的一種“看板”。
這種看板上標(biāo)明了供應(yīng)商的名稱,生產(chǎn)廠的收貨部門,使用該工件的場所,零件的編號、名稱及數(shù)量??窗迳线€有條形碼以便實(shí)施自動化分揀。
傳統(tǒng)的生產(chǎn)系統(tǒng)是一種“推進(jìn)式”系統(tǒng),只能根據(jù)預(yù)測進(jìn)行不均衡的生產(chǎn)。豐田的精益生產(chǎn)方式則是依靠且只依靠客戶的真實(shí)需求拉動、運(yùn)行生產(chǎn)系統(tǒng)。
其無浪費(fèi)的理想狀態(tài)是形成一個不間斷的價(jià)值流,只在客戶需要的時(shí)候才提供其所需數(shù)量的產(chǎn)品。
“看板制度是在無法實(shí)現(xiàn)真正的零庫存不間斷生產(chǎn)的情況下,不得已采取的一種在必要的地方建立緩沖存貨的有組織的制度?!?/span>
精益管理專家杰弗里·萊克曾這樣提醒道,“真正的挑戰(zhàn)在于必須建立起一個懂得尋找方法,減少使用看板制度,以降低存貨,且最終解除緩沖庫存的學(xué)習(xí)型企業(yè)?!?/span>
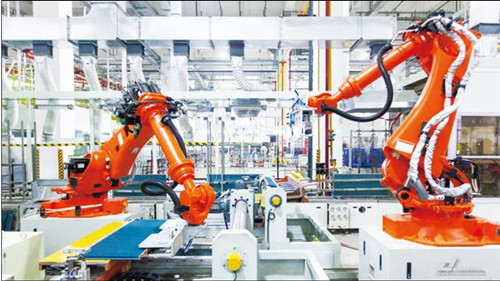
機(jī)器只是人力的延續(xù)
豐田有一個理念,堅(jiān)信機(jī)器只是人力的延續(xù),所以人們應(yīng)該致力于使機(jī)器更加適應(yīng)站在機(jī)器旁邊的操作者,而且所有的工人有責(zé)任和義務(wù)讓自己和他們的設(shè)備確保不將次品傳遞到下一道工序。
這和國內(nèi)許多企業(yè)的做法形成了鮮明的對比。在許多標(biāo)榜“以人為本”的企業(yè)里,機(jī)器、設(shè)備是企業(yè)集體的財(cái)產(chǎn),當(dāng)機(jī)器出現(xiàn)異常時(shí),機(jī)器的真正使用者,生產(chǎn)第一線的工人沒有權(quán)力擅自排除故障,必須遵守一定的程序,要向?qū)iT的維修部門報(bào)修,等待專門的維護(hù)人員來處理問題。
并非為了整潔的整潔
據(jù)說,20世紀(jì)七八十年代,去日本的豐田工廠參觀的美國人,第一反應(yīng)高度一致,全是感嘆車間的干凈、整潔。
有的甚至使用了這樣的話語:“哇,這個車間干凈得你可以把掉在地板上的東西撿起來吃!”這也是我們踏入總裝車間之后的感受。
不過,對于豐田人而言,他們在這方面的重視和努力可并非只是為了維持工廠的干凈整潔而已。
推行“6S”是支持無間斷流程與生產(chǎn)間隔時(shí)間,讓損害品質(zhì)或者導(dǎo)致機(jī)器故障的異常情況盡早浮現(xiàn)的一種視覺管理工具。
“6S”方案的一項(xiàng)重要工作就是設(shè)置工具圖像告示牌。比如,當(dāng)某個工位的工人因?yàn)榘l(fā)現(xiàn)異常而拉響生產(chǎn)停止拉線時(shí),和生產(chǎn)停止拉線相連的懸掛在車間安全通道上方的電子顯示屏上對應(yīng)的工位就會變成紅色。
正如天津大學(xué)經(jīng)濟(jì)管理學(xué)院院長齊二石所言:“豐田精益生產(chǎn)管理方式由管理模式和管理工具兩大部分組成。其中,管理工具是可以被模仿的,無法復(fù)制的是豐田式精益生產(chǎn)的管理模式?!?/span>
豐田精益生產(chǎn)方式使所有人對自己的工作負(fù)責(zé),鼓勵人們?nèi)ゲ粩喟l(fā)現(xiàn)更好的方式完成自己的工作。也正是因?yàn)榻o人們創(chuàng)造了發(fā)揮自己最大潛能的機(jī)會,豐田精益生產(chǎn)方式才得以成功。
文章來自網(wǎng)絡(luò),版權(quán)歸作者所有,如有侵權(quán)請聯(lián)系刪除