1987年夏天,我在麻省理工學院的辦公室里見證了一個新名詞的誕生。當時我們正預備出版一份國際汽車工業的研究報告,經過詳細的的研究和評估后,我們發現了一個新的管理體系,因此需要一個新的名字。
一位年輕的研究員約翰·克拉夫西科(John Kraficik),建議大家從這個新的系統中,包括產品和流程開發、價值流(從接單到生產再到運送)、供應商管理、客戶服務以及行政管理等不同的領域,去找出該系統與其他系統的不同點,然后再根據這些特點來命名。
我們在一塊白板上寫下了豐田/本田制造系統與傳統大批量生產的差異:
① 較少的人力來設計與制造產品,并且提供產品的售后服務;
② 較少的投資來實現相同的產能;
③ 較少的不良品以及返工;
④ 較少數目的供應商,但卻有更強的生產能力;
⑤ 較短的時間和較少的人力,來完成從概念到生產、從接單到交付、從問題到維護的過程;
⑥ 較少庫存;
⑦ 較少的安全事故。
約翰面對列舉出的不同點,看了幾分鐘后說道:“這個系統在創造價值的流程中,對各種需求都比較小,不如就叫它‘Lean’吧!”就這樣,“Lean” 這個名詞就誕生了。(約翰到麻省理工學院進修之前,曾在豐田汽車和通用汽車在加州的合資公司工作。之后,他為福特汽車公司工作了14年,并擔任SUV的總工程師。現在他是現代汽車公司美洲地區的總裁。)
當時看來一切都那么自然單純,但我們很快就發現,創建一個新體系就像生孩子一樣。父母腦子里對子女的未來發展有明確的方向,但孩子長大后卻往往有自己的想法!
隨著時間的流逝,我們好像在建造一座高塔。“精益”被廣泛地用來表示:目標(高質量、低成本、短時間)、方法(及時生產、自働化)、工具(看板、錯誤預防)以及生產方式(均衡生產、標準作業、改善、生產穩定性)等等。
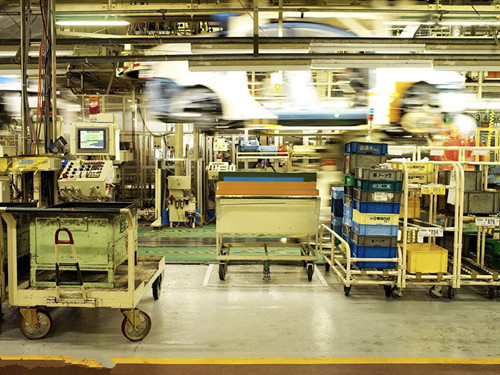
但每當我聽到一些人對“精益”有錯誤的理解或狹隘的解釋時,都會有些激動。我最近曾讀到一位杰出的生產系統專家所寫的文章,竟然指出“精益不包含標準作業”。我想我最好再次澄清“精益”的含義:
(1) 精益思想永遠從客戶的需求開始。
(2) 客戶希望得到價值:一個正確的產品,在正確的時間、正確的地點、以合理的價格和完美的質量來幫助他解決問題。
(3) 企業運營的價值——產品或服務,或者兩者的組合,都需要經過一個流程生產出來(流程包括產品設計、制造、為外部客戶提供的服務以及內部客戶的業務流程)。
(4) 每個流程都由一系列的步驟所組成,按照順序、在合理的時間內完成。
(5) 如果這些步驟中沒有浪費,用戶的價值就可以最大化(我相信你已經了解七種浪費:過量生產、等待、返工、多余的搬運、多余的庫存、多余的移動和次品)。
(6) 為了實現零浪費,創造價值的每個步驟都必須能提供價值(valuable),每個操作過程都能達標(capable),需要的時候設備能正常運轉(available),有足夠的產能滿足客戶需求(adequate),以及柔性生產線能調換生產多種產品 (flexible)。這些步驟必須準確地響應用戶的拉動,并流暢地把產品和服務傳遞給客戶。
(7) 一個真正的精益流程是完美的,完美地滿足用戶的需求,沒有浪費。
(8) 我們很少看到一個完美的流程。但精益實踐者始終相信,只要持續改善、精益求精,就能越來越接近完美的流程。
請注意:以上所提到的認識價值流、創建連續流,以及拉動系統等等,并不是精益實踐者的目的,而是為了達成完美價值流和零浪費的必要條件。而看板,防錯和其他方法,都是實現這些步驟的輔助措施。
要想把價值流轉變為精益,必須做到以上提到的每一點,它們相輔相成、缺一不可。比如,如果沒有標準作業,流程就不可能可靠和流暢;如果沒有改善,整個流程也不可能有很大的進步。只有當我們整合所有的方法、追求完美的流程、為用戶創造價值時,“精益”才能發揮神奇的功效。
文章來自網絡,版權歸作者所有,如有侵權請聯系刪除