長久以來,經常有人會提出問題,有關精益與其他方法的不同點,諸如豐田生產系統(TPS),六西格瑪,全面生產維護(TPM),業務流程再造(BPR),需求流動(Demand Flow),約束理論(TOC)等等。我總是會給出同樣的回答:一個完美的流程是準確地滿足客戶的需求,不產生任何浪費。以下是我的幾點想法。
為了創造客戶所需的價值,我們必須按照合理的順序,進行一系列的步驟。我希望大家都同意這點。這些步驟組合在一起,就是所謂的價值流,當我走訪任何一個價值流時,我都會提出以下的問題。
這個步驟有價值嗎?如果其中的某一個步驟被取消,客戶會對產品同樣的滿意嗎?舉例來說,有哪些是返工的步驟?如果有,我稱之為“第一類浪費”,盡快消除它們!另一種浪費,我稱之為“第二類浪費”。比如說把半成品從一個區,搬運到另一個不相連的工作區,這個步驟雖然不會為客戶提供價值,但當前的廠房無法立即改變來消除這種浪費,因此是流程中必須要有的步驟。這種浪費也應該消除,但通常需要較長的時間。
這個步驟能否滿足客戶的需求?能否每次按標準作業執行,都可以得到同樣的結果?這是六西格瑪的起點,但永遠不是終點。
這個步驟在需要時,能否正常運轉?會不會因為設備停機或者周期時間有波動,而導致你無法在需要時啟動生產?這是全面生產維護的起點,但也不是終點。
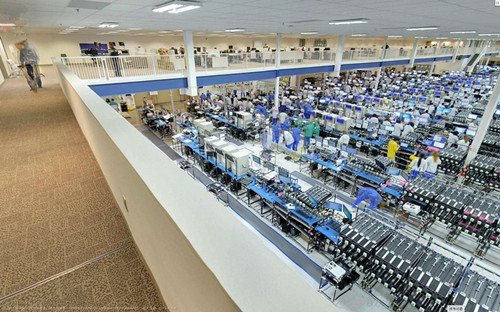
這個步驟的產能是否能滿足需求?有沒有足夠的產能來滿足價值流的需求?有沒有瓶頸?瓶頸分析是約束理論的起點。在今天的環境里,我們可能更需要去分析產能是否過剩?精益思想者往往通過小幅度地去增加產能,而不會大幅度地增加,以避免產能過剩的問題。同時,產能有時也可以臨時增加或減少員工來調節。
這個步驟是否能柔性地做調整,以滿足客戶需求?是否能快速地從生產綠色的產品切換到紅色?這個換模過程能否不影響產能、可靠性和客戶需求?柔性生產會根據客戶需要,快速調整生產計劃。豐田生產系統在這方面做得最好。
如果你價值流中的每一步驟都有價值,能滿足客戶需求,有足夠的產能,在需要時能夠運轉,并且可以按需求調整,你已經做得很好了。剩下的是怎么去完善步驟之間的銜接。
生產步驟之間有沒有拖延?亨利·福特(Henry Ford)在1914年,創建了“流水線生產”,讓生產的過程移到產品所在地,而不是移動產品去將就制造的過程。他不僅在汽車組裝線上,同時在零部件的制造線上,創造了近乎連續流的生產方式。但是,福特的流水線,當時還無法滿足客戶需求的變化;也不能在同一條線上生產多種不同類型的產品。但豐田后來在福特的流水線架構上,開發了豐田生產系統,來填補這個不足,創造了少量多樣的流動生產。
產品是不是只在下游拉動時才開始生產?這是及時化生產(Just-In-Time)的核心思想,也是豐田生產系統的主要支柱之一。
生產流程是不是從客戶端,就開始考慮均衡化?必要時可以設立成品庫存。均衡生產不僅確保整個價值流的通暢,并能保證有足夠的靈活性,能滿足客戶的需求。這是豐田生產系統的另一特色。
我們雖然還沒有創造出完美的價值流,可能永遠也達不到。但如果大家把精神都放在對比和評論各種不同的改善方法,而不去追求完美的價值流,那是我們亟須消除的一種浪費。
文章來自網絡,版權歸作者所有,如有侵權請聯系刪除