2012年福明從日本三菱回來,在電梯這個行業耕耘10載,尤其在電梯設計方面。他帶給我最為重要理論和案例——基于模型的數字研發。
比如和電梯相關的參數:長寬高,井深……等一系列相關的參數,建立電梯的標準模型,等到有新的客戶有新的需求,只要把客戶的參數往軟件里面一輸入,圖紙自動完成,自動完成成本核算。這個工具太偉大了,徹底把人從繁瑣的勞動中解放出來,完全符合工業4.0只從事創造的原點目標。
去年我的合作伙伴給日本一家企業實施類似的軟件信息化系統,非常順暢,但是到了國內,即便是臺灣的企業,問題就來了。研發這個東西在國內覺得是多么高大上的東西,充分發揮人的想象力,結果同樣的產品不同的研發,制造工藝都出現了不同,是不是很熟悉啊,我去過很多的企業,我給很多的客戶說你們的產品復雜度太高,必須回歸到統一的設計理念上來,而且按照標準的模塊進行設計,新的產品必須在老的產品上進行迭代開發,日本馬自達的發動機研究所甚至規定,不準設計當前模具無法加工的新的發動機,就是使產品的研發和制造能夠統一。
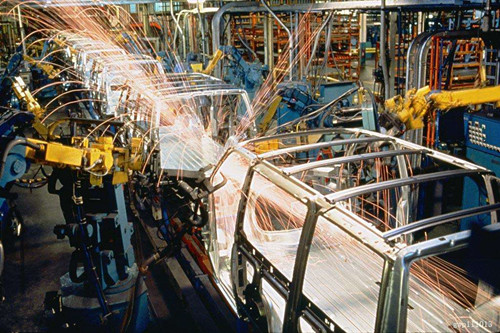
去年去一家國內頂級的家電廠家,他們希望我們可以給他們開發一套檢測設備,但是因為電線的連接采用的是固化在電路板上,又因為不同的型號是不同的人群開發,從而使產品的種類無限多,但是客戶僅僅要求對電路板的導電性進行測試,但是因為電線過多,不但亂而且容易造成電線相互纏繞,為處理這些電線的方向問題需要付出極高的成本,因此建議客戶采用電路板和電線分離的設計這樣不但在測試階段而且在組裝階段的自動化成本都非常低廉,機械實現的裝置也非常的簡單。
最近又去了一家家電企業,問題基本類似,研發的產品對于制造的重視度不夠,但是這家企業的負責人告訴我們現在已經簡化很多了,螺絲過多,對不同部件的鏈接手段的過于單一,產品設計模塊化不清晰,為了使這家公司能夠盡快的導入數字化制造,我們建議客戶首先對研發設計的管理進行重新的規劃,這樣才可以通過PLM軟件生成正確的BOM 和CAPP(輔助制造工藝)再通過MES傳遞到生產線,從而實現使人脫離中間的不創造價值而且繁瑣易錯的工作中。
國內企業目前的上層管理:運營、設計、采購……無論是組織模式還是運作模式的人為隨意性是信息化第一步建模無法完成的工作,無法建模則無法利用算法實現脫離人的檢查、確認、調整……工作,比如:現在用ERP經常在采購的時候進行庫存清點,因為對于中間的數據搞不清楚,也不清楚不良品,但是智能化的生產線會自動的采集各個段的生產數據,及時的更新到MES里面,進而更新到ERP的庫存數據里面,不存在數據調整和確認的問題,新的訂單輸入只要確認一下采購方即可,如果是單一供應商則可以根據當前的訂單情況,自動完成該任務,從而使具體的采購行為消失,進而無法完成這樣的信息化系統。從而使后面因為信息輸出的變異性,導致現場和具體運營混亂無章,這樣的企業無法實現4.0工具的具體導入,就是導入也會因為后期的上層的改變而發生重大改變。
國內4.0第一步可以從智慧工廠開始,而智慧工廠的前提是必須對研發進行梳理,使其實現迭代研發,然后利用感應器和在線測量技術進行質量和設備預維修的工業大數據采集系統,實現整個工廠運作數據的實時性和可控性,進而在利用其數據準確性,優化運作環節,建立標準模式,利用信息化完整運作的無人化,從而實現工業4.0制造的基本。
文章來自網絡,版權歸作者所有,如有侵權請聯系刪除