企業既不能盲目地推進自動化、機器換人,又不能停留在大量使用人工的作業方式,需要將自動化設備擅長重復性勞動和高速度的特點與工人的靈活性和判斷力有機地結合起來,從而在保證產品質量的基礎上,最大限度地提高生產效率。
我們簡單看下自動化的發展史,
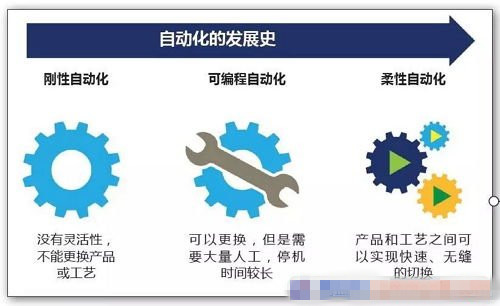
自動化已經從剛性的、只生產一種產品的方式,向柔性、可以無縫切換生產多個產品的方式過渡。
剛性自動化(Fixed Automation)主要設計用于反復高效地生產單個產品。過去,往往只產生一種或有限種類的產品,而且產量很大、變化很小,因此這種模式在生產車間運行良好。由于前期設備成本要低于柔性解決方案,因此對這類生產活動而言,剛性自動化非常適合。如果只生產單一部件,產量就可以得到優化。但是,模塊化通常不是原始設計所考慮的部分,這就意味著將機器設備轉換成支持多個產品配置時,從經濟方面考慮往往并不劃算,因此實施比較困難。
隨后出現了下一代自動化——可編程自動化(Programmable Automation),旨在實現安裝實施后允許某種程度的可配置性。這包括編寫新的代碼來執行新運營的能力,當然這需要手動操作機械裝置來進行轉換。缺點是,轉換過程往往勞動強度大,需要較長的停機時間以便更換工具和更改編程。
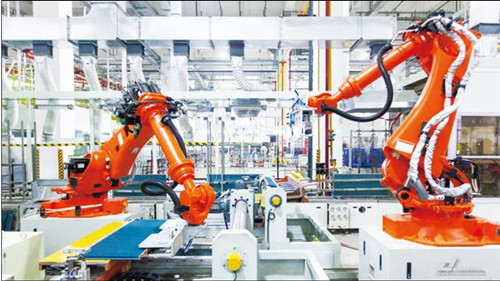
更現代的方法是柔性自動化(Flexible Automation),設備操作人員按下按鈕,就可以利用配方控制和機械自動化無縫地將一個進程轉換到另一個。這使制造商能夠在同一臺機器上生產更多的產品,前提是該機器的設計具有生產其它產品的能力。柔性設備采用機電自動化,將快速、可重復的過程轉換為位置控制。這允許生產線生產各種各樣的產品,而停機時間卻很短。
不同生產模式的制造企業,生產自動化程度差異很大:
1)對于采用大批量重復生產模式的企業,例如電子元器件、標準件、制藥、食品、飲料、鋼鐵、化工等行業的制造企業,無疑需要最大限度地實現自動化、少人化,甚至無人化,人的參與是該行業生產過程中最大的污染源。
2)對于采用小批量、多品種生產模式的企業,例如各類按訂單生產(MTO)的機械制造、汽車零部件和電氣產品制造企業,則應該強調人機結合,將工人的智慧和經驗與自動化設備和產線相結合。對于小批量、多品種,以及單件小批生產的企業,推進零部件的標準化、系列化、模塊化具有十分重要的意義。模塊化程度越高,就越有可能實現生產和組裝環節的自動化。
目前很多盲目上自動化的公司都接受過這樣的教導:為了提高效率,必須提高機器的利用率。即為了最大限度地利用機器,我們必須做到以下幾點:
讓設備不間斷地、盡可能快地運轉,這將會造成過量生產浪費;
保留額外的人員以維持機器運行;
增加在制品存量以掩蓋問題,維持機器運轉。
?
換句話說,盲目追求自動化或者機器利用的最大化就是在制造浪費! ?
?
相比之下,豐田公司設法最大限度地利用人力 - 人的靈活性帶束的好處要大于機器利用率帶來的好處。
比如說,操作員可以做到:
只要有需求,就可以從一臺機器轉到另一臺機器進行生產;
可以輕松地為機器裝載需要加工的部件并傳送部件,而具有自動裝載和自動傳送功能的機器成本以指數形式增加。
輕松調整工作周期以響應需求的變化。
與大型、復雜的機器相比,小型、簡單的機器更可取,因為它們具有以下特點:
更便宜(而且往往能在內部制造出來);
更穩健(很少有移動部件);
可以輕松適應需求的變化(如果需求加倍,我們可以增加一臺機器。如果需求減半,我們可以在低成本的情況下讓機器閑置一般時間)。
精益系統標準作業的重點是人的運動,追求的是順暢、安全、以人為中心的工藝流程。TPS倡導在機器設備進來之前,就開始研究布局,把機器也當做人一樣分析,研究機器是否符合人的動作。
文章來自網絡,版權歸作者所有,如有侵權請聯系刪除