自從摩托羅拉公司提出六西格瑪的管理理念以來,現在已經被世界上的很多國家和地區所采用,為摩托羅拉、通用、戴爾、惠普、西門子、索尼、東芝等眾多跨國企業帶來卓有成效的改善。那六西格瑪管理到底從何而來呢,要從質量開始說起, “質量”的概念最早從制造業提出,從1900年開始到20世紀結束。
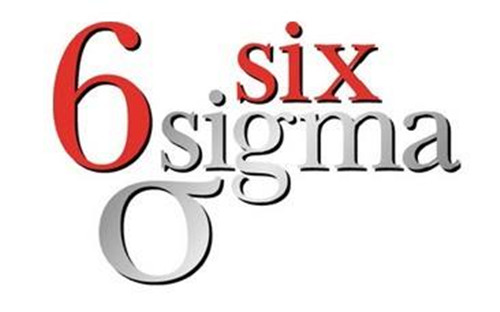
1.操作者時代
1900年的制造業主要以作坊式的生產為主,操作者對產品的質量負責,此時期稱為“操作者時代”。
2.工長時代
1918年,產品的工業化以及專業化分工越來越明確。比如,做鞋子,有人專門負責做鞋底、有人專門負責做鞋幫、有人專門負責做鞋面,最后有人把各部分組裝成成品。工廠中出現了“工長”這一角色,“工長”負責協調、組織和計劃每一道工序,對產品的質量負責。
3.檢驗員時代
1937年,“質量”的概念開始成型。例如,鞋子出廠以后發現有質量問題會被退回廠家,并且要求索賠,于是,工廠開始在產品出廠前對鞋子進行檢查,質量合格的賣給客戶,不合格的要返工或返修,工廠有了專職的檢驗員以及相應的檢驗標準、檢驗設備和檢驗方法。
4.統計SPC時代
一方面,冰箱、洗衣機、電腦以及手機等產品在出廠前都經過檢驗,檢驗內容包括材料、工序以及成品,但最終到達用戶的產品還是會有質量問題,這是因為產品的檢驗是抽樣檢測,不是全檢,否則成本太高。
另一方面,像衛星、航天飛船等產品數量極少,并且每個產品都要進行檢測,偶爾也會出現質量問題,這是因為產品的檢測方法有局限性,也就是說,產品的很多質量特性是不能夠檢驗的。比如,鞋子的粘合力與制作時的力度有關,力度越大,越不容易開膠,檢驗鞋子的粘合力需要用拉力機,但測試完粘合力以后,被檢測的鞋子也就被破壞了。
此外,檢驗永遠不可能檢查全功能,如可靠性、壽命等因素是無法檢驗的。
檢驗是一個基本的質量手段,一定要有,但質量檢驗有兩個功能無法達到:第一,檢驗只能區分好與壞,不能阻止次品的產生;第二,檢驗永遠不可能檢驗全功能,有些功能是不可檢驗的。
人們控制不了結果,就想到了控制過程,于是在1960年出現了SPC,即統計過程控制(Statistic Process Control)。

5.全面質量管理時代
“全面質量管理”的概念在1980年被提出。
案例:手機返修隱藏的成本
手機剛剛問世時,返修率高達10%。假設一個廠家每年生產1000萬部手機,10%的返修率意味著每年被退回100萬部,而維修又伴隨著一系列相關的費用,比如,運費、每個城市布點的費用以及更換零部件的費用,如果每部手機的維修費用平均是100元,那么100萬部手機的維修費用就是1億元,這些費用全部由廠家承擔。這還只是因為質量不好而帶來的損失,如果加上返修的損失,更是一個驚人的數字。
產品質量出現問題,責任不只在質檢部門,因為質檢只能區分好壞,而且質檢不可能檢驗全功能,所以,生產部門、研發部門、采購部門都有責任;產品質量與產品標準、人員、設備等也都有一定的關系。質量問題是系統問題,不是某個人或某個部門能夠解決的,因此,1980年出現了“全面質量管理”的概念,進入全面質量管理時代。
6.六西格瑪時代
1990年出現了六西格瑪管理的概念,六西格瑪的出現推動了所有部門、所有環節參與到質量管理中。
以上是質量管理在西方國家發展的一百年,中國真正開始實施質量管理是20世紀80年代以后的事情。
那么,什么是西格瑪呢?西格瑪又叫做標準偏差,是一個數值概念:西格瑪值越大,說明標準偏差越大,一組數據的波動性也越大;西格瑪值越小,說明標準偏差越小,波動性也越小。在實際工作中,如果采用平均值的思維,會讓業務遭受損失,因為波動性無處不在。例如,A、B兩個工廠每年分別生產12000支筆,即平均每月生產1000支,A工廠在某四個月的訂單分別是100、1900、200、1800,B工廠在某四個月的訂單分別是800、1200、900、1100,雖然平均產量相同,但A工廠的成本肯定會高于B工廠,因為A工廠會因產量不穩定而產生閑置費用和加班費用,所以波動性越大,成本越高,質量越不穩定,對客戶滿意度的影響越大。
六西格瑪是流程能力的衡量尺度,能夠達到六西格瑪水平,說明每100萬次的動作中只有3.4次缺陷的機會。經營公司有很多環節,每個環節都可能出現差錯,如果每個環節出現差錯的幾率都非常小,整體出現差錯的概率也會很小,成本就會下降,質量就會提高,所以,六西格瑪是一個衡量指標。六西格瑪能夠把全面質量管理的思想變成現實,全面質量管理的核心有全員參與、客戶導向以及持續改進,這三條奠定了全面質量管理的基礎。
文章來自網絡,版權歸作者所有,如有侵權請聯系刪除