生產運營中,過高的庫存不僅占用大量資金與倉儲空間,還會掩蓋生產流程中的問題,成為企業發展的沉重負擔。生產精益管理以消除浪費、提升效率為核心,為降低庫存提供了科學且有效的解決方案。接下來將深入探討生產精益管理如何精準發力,實現庫存的有效降低。
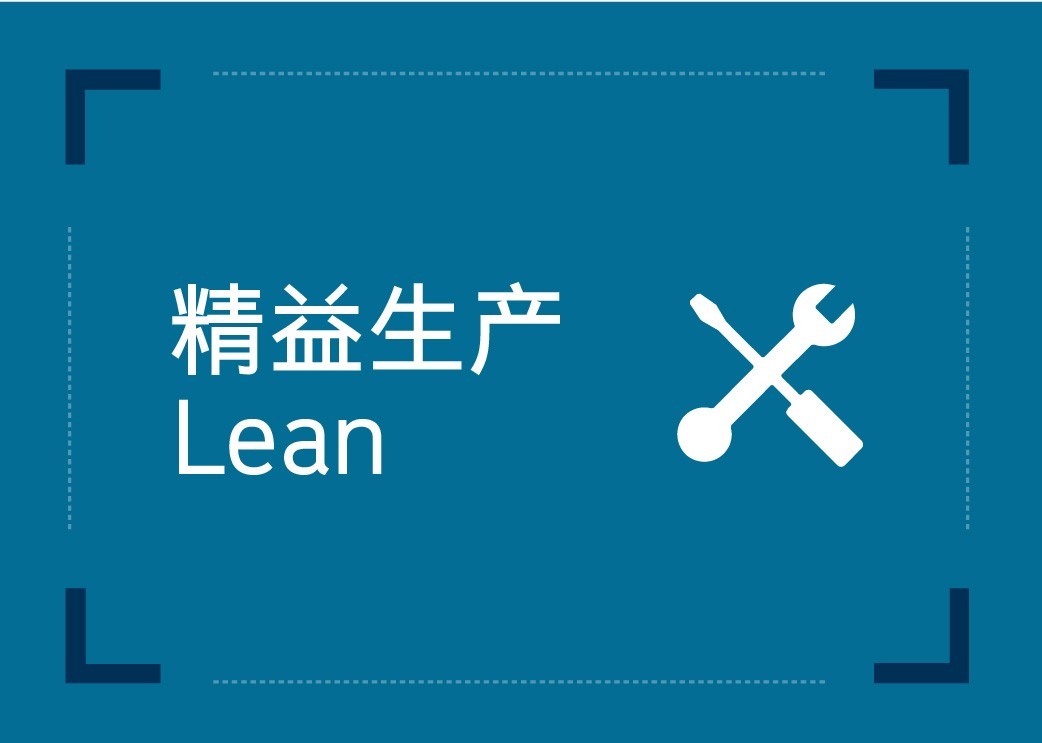
一、明確庫存浪費的本質與危害
庫存本身并非毫無價值,但超出實際需求的庫存便是一種浪費。過多的原材料庫存,意味著企業提前支付貨款,大量資金被閑置;在制品積壓,會延長生產周期,阻礙資金周轉;成品庫存居高不下,則可能因市場需求變化、產品更新換代而面臨貶值風險。這些庫存浪費如同隱藏在企業體內的“暗疾”,消耗著企業的資源與活力,降低企業對市場的響應速度,削弱企業的競爭力。
二、生產精益管理降低庫存的核心方法
1、價值流分析,精準定位庫存癥結
價值流分析是精益管理的關鍵工具,通過繪制從原材料采購到產品交付的整個價值流圖,清晰展現物料與信息的流動過程。在這個過程中,能夠直觀發現生產環節中導致庫存積壓的瓶頸、等待時間過長等問題。例如,某汽車零部件生產企業在進行價值流分析時,發現沖壓工序與組裝工序之間存在大量在制品庫存,深入分析后得知是兩者生產節拍不匹配所致。基于此分析,企業對生產流程進行優化,有效降低了在制品庫存。
2、拉動式生產,按需生產減少冗余
拉動式生產與傳統的推動式生產不同,它以客戶需求為驅動。只有當客戶訂單下達,后續工序出現需求時,前序工序才進行生產。這種模式下,生產節奏與市場需求緊密貼合,避免了因盲目生產而造成的庫存積壓。豐田公司是拉動式生產的典型代表,其采用看板管理系統,前工序根據后工序的看板指令進行生產和配送物料,實現了零部件庫存的大幅降低,同時保證了生產的連續性和及時性。
3、JIT(準時制)采購,優化供應鏈庫存
準時制采購旨在使原材料和零部件在需要的時間、以需要的數量、達到需要的質量,直接投入生產。企業與供應商建立緊密合作關系,要求供應商小批量、多頻次供貨,減少原材料庫存。例如,電子產品制造企業與周邊的元器件供應商達成協議,實現每日多次供貨,將原材料庫存周轉天數從30天縮短至7天,降低了庫存成本,同時提高了對市場需求變化的應對能力。
4、5S管理,提升倉儲空間利用效率
5S管理包括整理、整頓、清掃、清潔和素養五個方面。通過整理,區分必需品和非必需品,及時清理多余物料;整頓則是對必需品進行合理定位和標識,便于快速取用;清掃和清潔確保工作環境整潔有序;而素養的培養讓員工養成良好習慣,維持管理成果。某食品加工廠通過實施5S管理,重新規劃倉儲布局,優化物料擺放方式,使倉儲空間利用率提高30%,減少了因空間不足導致的庫存堆放混亂問題,間接降低了庫存管理成本。
三、生產精益管理降低庫存的實施步驟
1、組建專業團隊,制定清晰目標
成立由生產、采購、倉儲、質量等部門人員組成的精益管理團隊,明確降低庫存的具體目標,如將原材料庫存周轉率提高,成品庫存降低等,并制定詳細的實施計劃與時間表。
2、全員培訓,強化精益理念
對全體員工進行精益管理知識培訓,使其理解降低庫存的重要性和方法,培養全員參與的意識,為實施工作營造良好氛圍。
3、試點先行,總結推廣經驗
選擇一個車間或一條生產線作為試點,應用精益管理方法進行庫存優化。在試點過程中,及時總結經驗教訓,調整改進方案,待取得顯著成效后,再在企業全面推廣。
4、持續監控與改進
建立庫存監控指標體系,定期分析庫存數據,評估精益管理措施的實施效果。根據分析結果,不斷調整優化管理方法,持續降低庫存水平。
四、實施過程中的挑戰與應對
在通過生產精益管理降低庫存的過程中,企業可能會面臨諸多挑戰。例如,供應商配合度不高,無法滿足小批量、多頻次供貨要求;員工對新的管理模式不適應,存在抵觸情緒等。針對這些問題,企業可以加強與供應商的溝通與合作,通過簽訂長期合作協議、提供技術支持等方式,提高供應商的配合度;同時,加強對員工的培訓與引導,通過激勵機制鼓勵員工積極參與,逐步轉變員工觀念,確保精益管理措施順利實施。
生產精益管理為企業降低庫存提供了全面且有效的解決方案。通過運用價值流分析、拉動式生產、JIT采購等方法,結合科學的實施步驟與問題應對策略,企業能夠逐步消除庫存浪費,實現庫存的合理控制,提升生產運營效率,增強自身的市場競爭力,在激烈的市場競爭中贏得更大的發展空間。?