制造業(yè)競爭白熱化,機(jī)械加工車間作為產(chǎn)品生產(chǎn)的核心環(huán)節(jié),普遍面臨著生產(chǎn)效率低下、資源浪費(fèi)嚴(yán)重、產(chǎn)品質(zhì)量不穩(wěn)定等難題。傳統(tǒng)生產(chǎn)模式下,設(shè)備閑置、物料堆積、工序銜接不暢等現(xiàn)象屢見不鮮,不僅增加了生產(chǎn)成本,還影響了企業(yè)的交付能力和市場競爭力。精益生產(chǎn)以消除浪費(fèi)、優(yōu)化流程、提升價值為核心,為機(jī)械加工車間突破發(fā)展瓶頸提供了科學(xué)的方法論和實踐路徑。
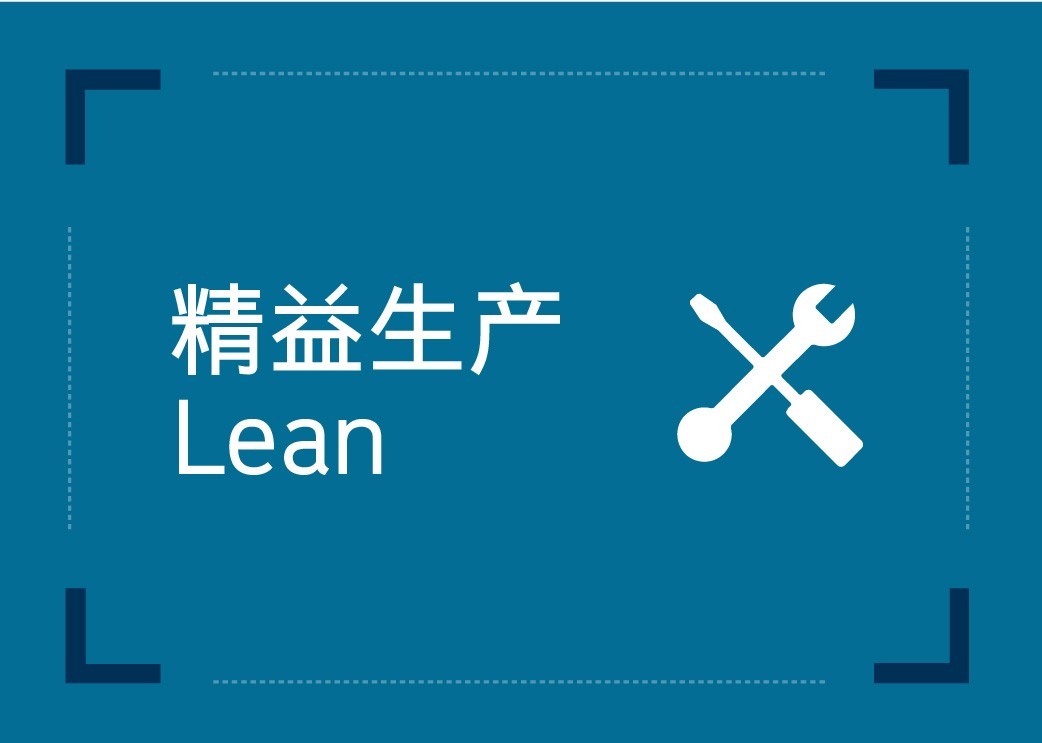
一、機(jī)械加工車間現(xiàn)存問題剖析
機(jī)械加工流程復(fù)雜,涵蓋車、銑、刨、磨、鉆等多種工藝,生產(chǎn)環(huán)節(jié)繁多,這使得車間管理難度增大。生產(chǎn)現(xiàn)場常常出現(xiàn)物料擺放雜亂無章,工人尋找工具和零件耗時過長;設(shè)備故障頻發(fā),缺乏有效的預(yù)防性維護(hù)計劃,導(dǎo)致停機(jī)時間增加;生產(chǎn)計劃安排不合理,工序之間銜接不順暢,存在大量等待時間;質(zhì)量檢測環(huán)節(jié)滯后,不良品無法及時發(fā)現(xiàn)和處理,造成返工和資源浪費(fèi)。這些問題相互交織,嚴(yán)重制約了車間的生產(chǎn)效率和經(jīng)濟(jì)效益。
二、精益生產(chǎn)理念在機(jī)械加工車間的應(yīng)用核心
精益生產(chǎn)的核心思想是通過持續(xù)改進(jìn),識別并消除生產(chǎn)過程中的一切浪費(fèi),包括過量生產(chǎn)、等待時間、運(yùn)輸浪費(fèi)、庫存積壓、動作浪費(fèi)、加工浪費(fèi)和不良品浪費(fèi)等“七大浪費(fèi)”。在機(jī)械加工車間,精益生產(chǎn)強(qiáng)調(diào)以客戶需求為導(dǎo)向,優(yōu)化生產(chǎn)流程,實現(xiàn)生產(chǎn)的均衡化、標(biāo)準(zhǔn)化和自動化;通過價值流圖(VSM)分析,梳理整個生產(chǎn)流程,找出瓶頸環(huán)節(jié)和浪費(fèi)點(diǎn);運(yùn)用5S管理(整理、整頓、清掃、清潔、素養(yǎng))規(guī)范現(xiàn)場管理,營造整潔有序的生產(chǎn)環(huán)境;借助全員生產(chǎn)維護(hù)(TPM)提升設(shè)備綜合效率;并通過持續(xù)改進(jìn)(Kaizen)的方法,鼓勵全員參與,對生產(chǎn)流程進(jìn)行不斷優(yōu)化,從而提高生產(chǎn)效率、降低成本、提升產(chǎn)品質(zhì)量。
1.優(yōu)化車間布局,實現(xiàn)高效流轉(zhuǎn)
傳統(tǒng)機(jī)械加工車間多采用功能布局,將相同類型的設(shè)備集中放置,這種布局方式會導(dǎo)致物料運(yùn)輸距離長、工序銜接不暢。精益生產(chǎn)倡導(dǎo)采用單元化布局,根據(jù)產(chǎn)品加工工藝和生產(chǎn)流程,將相關(guān)設(shè)備組合成一個個獨(dú)立的生產(chǎn)單元。每個單元負(fù)責(zé)特定產(chǎn)品或零部件的生產(chǎn),物料在單元內(nèi)實現(xiàn)快速流轉(zhuǎn),減少了運(yùn)輸浪費(fèi)和等待時間。例如,對于生產(chǎn)小型機(jī)械零件的車間,可以將車床、銑床、磨床等設(shè)備按照加工順序組成一個單元,工人在單元內(nèi)完成從毛坯到成品的全部加工工序,大大提高了生產(chǎn)效率。
2.推行5S管理,規(guī)范現(xiàn)場秩序
5S管理是精益生產(chǎn)的基礎(chǔ)。在機(jī)械加工車間,首先進(jìn)行整理,區(qū)分生產(chǎn)現(xiàn)場的必需品和非必需品,清理掉多余的工具、報廢的零件、過期的文件等,釋放空間;接著開展整頓工作,對保留的物品進(jìn)行合理定位和標(biāo)識,如在工具柜上繪制工具形狀,使工具使用后能準(zhǔn)確歸位,在物料架上標(biāo)明物料名稱、規(guī)格和存放數(shù)量;定期進(jìn)行清掃,確保設(shè)備、地面、工作臺面等干凈整潔,及時發(fā)現(xiàn)并處理設(shè)備漏油、漏水等問題;將整理、整頓、清掃的成果制度化,形成清潔的工作環(huán)境;zui后通過培訓(xùn)和日常監(jiān)督,培養(yǎng)員工良好的素養(yǎng),使5S管理成為員工的自覺行為。通過5S管理,車間現(xiàn)場變得井然有序,工人能夠快速找到所需物品,設(shè)備故障率降低,生產(chǎn)效率得到提升。
3.實施全員生產(chǎn)維護(hù)(TPM),提升設(shè)備效能
設(shè)備是機(jī)械加工車間生產(chǎn)的關(guān)鍵,設(shè)備故障會嚴(yán)重影響生產(chǎn)進(jìn)度。TPM強(qiáng)調(diào)全員參與設(shè)備維護(hù),將設(shè)備維護(hù)責(zé)任落實到每一位員工。制定設(shè)備點(diǎn)檢表,明確設(shè)備的檢查項目、標(biāo)準(zhǔn)和周期,操作人員每天對設(shè)備進(jìn)行日常點(diǎn)檢,及時發(fā)現(xiàn)設(shè)備異常;專業(yè)維修人員定期對設(shè)備進(jìn)行全面檢查和維護(hù),制定預(yù)防性維護(hù)計劃,更換易損件,調(diào)整設(shè)備參數(shù),避免設(shè)備突發(fā)故障。同時,開展設(shè)備操作和維護(hù)培訓(xùn),提高員工的設(shè)備操作技能和維護(hù)意識,使員工能夠正確使用設(shè)備,并及時發(fā)現(xiàn)和報告設(shè)備問題。通過TPM的實施,設(shè)備綜合效率(OEE)得到顯著提升,停機(jī)時間大幅減少。
4.運(yùn)用價值流圖(VSM)分析,優(yōu)化生產(chǎn)流程
價值流圖是精益生產(chǎn)中分析和優(yōu)化流程的重要工具。通過繪制當(dāng)前生產(chǎn)流程的價值流圖,直觀展示物料流動、信息傳遞、生產(chǎn)周期等環(huán)節(jié),識別出生產(chǎn)過程中的浪費(fèi)和瓶頸。例如,發(fā)現(xiàn)某道工序加工時間過長,導(dǎo)致后續(xù)工序等待,就可以對該工序進(jìn)行分析,通過優(yōu)化工藝參數(shù)、改進(jìn)工裝夾具或增加設(shè)備等方式縮短加工時間;又如,發(fā)現(xiàn)物料配送不及時,造成生產(chǎn)中斷,就可以調(diào)整物料配送計劃,采用看板管理等方式實現(xiàn)物料的準(zhǔn)時供應(yīng)。通過不斷對價值流圖進(jìn)行分析和改進(jìn),使整個生產(chǎn)流程更加順暢高效。
5.建立標(biāo)準(zhǔn)化作業(yè),確保質(zhì)量穩(wěn)定
標(biāo)準(zhǔn)化作業(yè)是保證產(chǎn)品質(zhì)量和生產(chǎn)效率的重要手段。對機(jī)械加工車間的每一道工序,制定詳細(xì)的作業(yè)標(biāo)準(zhǔn),包括操作步驟、工藝參數(shù)、質(zhì)量要求、安全注意事項等。通過培訓(xùn)使員工掌握標(biāo)準(zhǔn)化作業(yè)方法,并在生產(chǎn)過程中嚴(yán)格按照標(biāo)準(zhǔn)執(zhí)行。同時,定期對作業(yè)標(biāo)準(zhǔn)進(jìn)行評估和修訂,根據(jù)工藝改進(jìn)、設(shè)備更新等情況及時調(diào)整標(biāo)準(zhǔn),確保標(biāo)準(zhǔn)的有效性和適應(yīng)性。標(biāo)準(zhǔn)化作業(yè)的實施,不僅提高了產(chǎn)品質(zhì)量的穩(wěn)定性,減少了不良品率,還使新員工能夠快速掌握操作技能,縮短培訓(xùn)周期。
6.引入看板管理,實現(xiàn)拉動式生產(chǎn)
傳統(tǒng)的機(jī)械加工車間多采用推動式生產(chǎn),即按照生產(chǎn)計劃大量生產(chǎn)產(chǎn)品,容易造成庫存積壓。看板管理是一種拉動式生產(chǎn)方式,通過看板傳遞生產(chǎn)和物料信息,實現(xiàn)“在需要的時候,按需要的量,生產(chǎn)所需的產(chǎn)品”。在車間內(nèi)設(shè)置生產(chǎn)看板和物料看板,生產(chǎn)看板顯示當(dāng)前生產(chǎn)任務(wù)、進(jìn)度和質(zhì)量情況,工人根據(jù)看板信息進(jìn)行生產(chǎn);物料看板則標(biāo)明物料需求信息,當(dāng)工序需要物料時,通過物料看板通知物料配送人員及時配送。看板管理的引入,使生產(chǎn)過程更加透明,有效減少了庫存積壓,提高了生產(chǎn)的靈活性和響應(yīng)速度。
在機(jī)械加工行業(yè)競爭日益激烈的今天,精益生產(chǎn)改善是車間實現(xiàn)轉(zhuǎn)型升級、提升競爭力的必由之路。通過優(yōu)化布局、規(guī)范管理、提升設(shè)備效能、優(yōu)化流程等一系列精益生產(chǎn)方法的實施,機(jī)械加工車間能夠有效消除浪費(fèi)、提高生產(chǎn)效率、穩(wěn)定產(chǎn)品質(zhì)量,實現(xiàn)從傳統(tǒng)生產(chǎn)模式向精益生產(chǎn)模式的轉(zhuǎn)變,為企業(yè)的可持續(xù)發(fā)展奠定堅實基礎(chǔ)。?