精益生產的兩大支柱之一是JIT和自働化。而JIT的實現方式是拉動式生產。
既然是拉動式生產,必然要有去拉的人(發起者)和被拉的人(被驅動者)。
JIT生產方式的核心思想之一,是要盡量使工序間的在制品數量接近于零。這就是說,前工序的加工一結束,就應該立即轉到下一工序去,這種生產同步化(順暢化)是實現JIT生產的一個基本原則。為了實現這一原則,JIT生產方式在設備布置和作業人員的配置上采取了一種全新的方法:“一個流”生產。
一個流是標準化的必然步驟,沒有標準化就沒有改善。
而流水作業就是先將混亂的流程加以整理和標準化,作為改善的出發點。
精益生產的目的就是通過持續改善來徹底消除浪費。
而改善的第一步是什么,當然是,標準化!
如果你的生產流程如左圖,你能發現問題在哪里嗎?或者說你能很快準狠的找出問題在哪里嗎?反之,如果變成右圖,問題一旦產生,是不是就一目了然?冤有頭,債有主,想賴都賴不了。
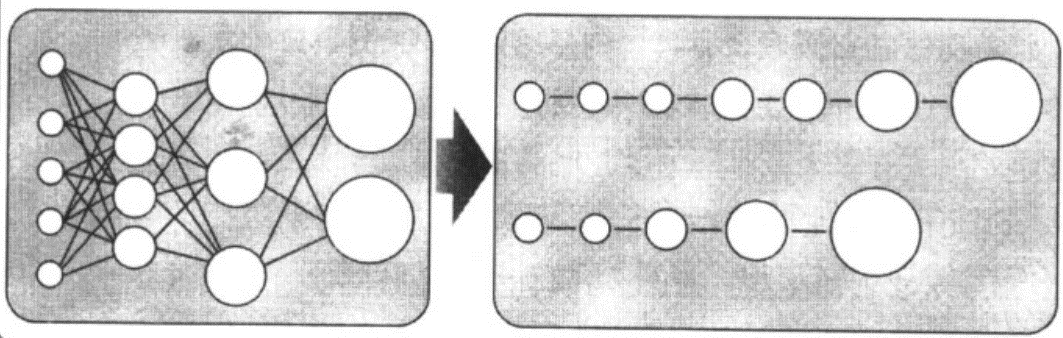
如果沒有流水線化,那么,
--誰來發起?誰來接收?
--如何發起?如何接收?
--用什么方式發起?
--接收后如何反應?
--拉動的信號如何準確,及時,無誤的傳遞?
……
結果自然是亂作一團,拉都沒法拉,流那是更不可能的了。
混亂之中,當然有很多樂趣,然而沒有效率。
流水式的作業方式是最有效的暴露問題的方式(起碼目前如此)。
物料與信息的流程連續不斷時,作業流程的浪費情形就會減少。
這是很明顯的道理。這跟金錢必須流動起來才能產生效益是一樣的。
若存在許多浪費,物流和信息就無法暢通輸送。
而在生產流程中,保持作業步驟之間的無間斷流程將會產生關聯,使每個作業步驟彼此相互依賴。這種相互依賴性及相對較少的阻礙將會使任何干擾流程的浪費更加突出,從而更容易發現改善的機會。
一個流只能在裝配車間。答案是 錯。裝配作業通常更容易實現一個流。但這并不意味著只有裝配車間才能進行一個流。例如壓鑄車間建立一個流的案例的。壓鑄,去水口,機加工,研磨,包裝都在圍繞著壓鑄機形成多條完整的小流水線。
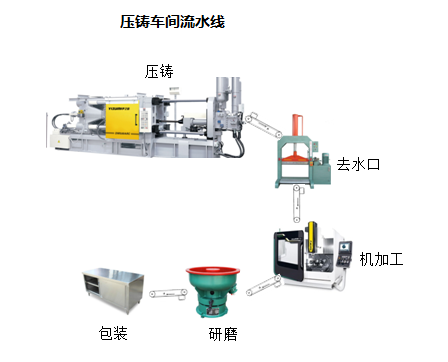
還有家具行業的資深從業人士,我自己也是操持過如何在木加工車間建立一個流的。事實上,理想中的不間斷流應該是從裝配車間發起,聯動到供應商。
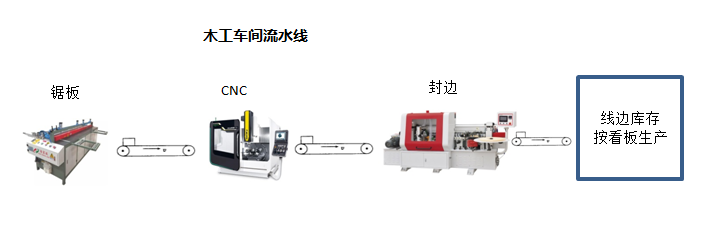
“一個流”生產的八大要點
1.單件流動
“一個流”生產的第一要點就是要使產品生產的各道工序做到幾乎同步進行,使產品實現單件生產、單件流動。單件流動是為了避免以批量單位進行加工,前道工序的加工一結束就立刻轉到下一道工序,從而使得工序間在制品的數量接近于零。
2.按加工順序排列設備
在一些工廠中經常可以看到,不同工序的加工設備之間的距離非常遠,加工過程中產生的中間產品需要花費較多時間和人力才能搬運到下一道工序,這樣的現象被稱為孤島設備。“一個流”生產要求放棄按設備類型排列的布局,而是按照加工順序來排列生產設備,避免孤島設備現象的出現,盡可能使設備的布置流水線化,真正做到只有“一個流”。-
3.按節拍進行生產
“一個流”生產還要求各道工序嚴格按照一定的節拍進行生產。如果各道工序的生產節拍不一致,將會出現產品積壓和停滯,無法形成“一個流”。因此,應該設法讓生產慢的設備快起來,生產快的設備適當減慢速度,每一道工序都按節拍進行生產,從而使整個生產過程順暢。.
4.站立式走動作業
在很多工廠的生產現場都可以看到,工人們幾乎都坐著工作,他們的很多動作都屬于浪費。從JIT的角度來講,為了調整生產節拍,有可能需要一個人同時操作兩個或多個設備,這就要求作業人員不能坐著工作,而應該采用站立走動的作業方式,從而提高工作效率。
5.培養多能工
在傳統生產方式中,工人通常只會操作一種設備。當A設備的生產能力很強而B設備的生產能力較弱時,很容易造成A設備的操作工人空閑而B設備的操作工人過于繁忙,從而導致生產不均衡。因此,“一個流”生產要求工人能夠操作多臺生產設備,通過培養多能工來均衡整個生產節拍。此外,培養多能工還有利于人員的增加或減少。
6.使用小型、便宜的設備
由于大型設備的生產能力很強,很容易讓后續工序無法及時跟上,從而導致大量的中間產品積壓。此外,大型設備還會造成投資和占地面積的增加。因此,JIT不主張采用自動化程度高、生產批量大的設備,而主張采用小型、便宜的設備。在不影響生產的前提下,越便宜的設備越好,這樣不但投資少,而且靈活性高。
7.“U”型布置
如果將生產設備一字擺開,工人從第一臺設備到最后一臺設備就需要走動很遠的距離,從而造成嚴重的人力浪費。因此,“一個流”生產要求將生產設備按照“U”字型來排列,從入口到出口形成一個完整的“U”型,這樣就可以大量的減少由于不同工序之間的傳遞而造成的走動,減少時間和搬運的浪費,增加生產效率。
8.作業標準化
作業的標準化就是要求每一個崗位、每一道工序都有一份作業指導書,然后檢查員工是否按照作業指導書的要求工作,這樣就能強制員工嚴格按照既定的生產節拍進行生產。如果作業沒有標準化,那么生產一個產品的時間就得不到控制,無法控制生產節拍,更無法保證形成“一個流”。
很多公司在實施“一個流”作業時沒有取得想象中的成功,只是因為犯了三個常見的錯誤。
(1)建立了“假流程”
假流程最明顯的特征是,按照工藝順序將各種設備揉和在一起,創造出一個看著象的生產流程。但是每個階段都進行大批量生產,完全沒有節拍時間的概念。這樣的后果是表面上看起來是一個流,實際上就是大批量生產。所以最終導致各個工序之間的物料堆積,跟以前離散式的并沒有什么差別,同時讓場地更擁擠。因為設備(工序)弄到一塊來了。
(2)公司在發現一個流帶來問題和沖擊后,退回到原路。很多人對于精益生產的態度實際是葉公好龍,愿意把一些精益工具當成玩具,傾向于玩弄一些虛無的概念。但在實際應用這些概念而導致一些短期成本和痛苦時,就不是那么回事了。稍微出現一點打亂正常生產的問題,就方寸大亂,進而全盤否定。事實上,設備故障,物料延遲,質量問題等導致的停工和延遲,一定會發生,尤其在初期。而這,正是解決問題,努力改善的大好時機,可很多公司卻白白浪費,甚至否定精益和連續流。
(3)欠缺標準化作業
這其實是個最常見的問題。許多公司的標準化作業極其薄弱。在這種模式下應用不間斷流的概念,只會死得更快更難看。就好像一個本身心臟有問題的人,你偏要通過劇烈運動來康復,這跟自殺沒有什么區別。不積跬步,無以至千里。所有的事情都要先從基礎做起。精益的基礎就是標準化。
所有這些因為因為道聽途說而實施一個流的人的失敗都是可以期待的,雖然并不值得同情。因為他們總是習慣于將精益工具擺在優于理解的地位,從而缺乏對精益生產一些基本概念的理解和探索。
本文為冠卓咨詢原創文字作品,任何人或組織不得對本文進行篡改,轉載或以盈利為目的行為,一經發現,將負法律責任。